Ahead of the curve
Have you ever tried using “lattice” or “living” hinges to bend wood? As anyone who has looked into adding a laser to a CNC knows, you can do that with…
Have you ever tried using “lattice” or “living” hinges to bend wood? As anyone who has looked into adding a laser to a CNC knows, you can do that with a laser. Today’s lasers don’t just engrave. They can also cut all the way through wood, plywood and other sheet stock such as plastics and thin metals.
They’re also less labor intensive and far more precise than most woodworking machinery, so they’re definitely worth considering for shops that want to offer something unique or perhaps add the ability to make wooden parts for other industries.
It’s surprising how many CNC routers can be adapted to use a laser head, so shops that are upgrading might want to check with the manufacturer before they sell the old CNC. And there are a number of small desktop lasers available at surprisingly affordable prices that allow a shop to dabble a bit and learn something about the technology before making a major investment.
A laser might be able to enhance current production, introduce new techniques and abilities and will definitely get the creative juices flowing. Designers who are competent in CAD and CAM will love the idea of being able to create a toolpath that is smaller and thinner than anything a router can manage. The lattice hinge, for example, means that a designer can bend wood by creating a cut pattern that is essentially just a series of interlocking fingers. The magic here is that there is only one long, continuous cut and when that’s done there are no parts to assemble.
The process is explained in more detail on Epilog Laser’s website (epiloglaser.com) on the Sample Club page. If you’re mulling over the decision to buy a laser and are worried that you won’t find enough ways to use it, the laser manufacturer’s site offers dozens of how-to projects with engraving files and laser settings, so they’re easy to replicate or customize. Other examp
Kern Lasers also features sample projects on its website (kernlasers.com) on the Applications page.les include fabricating 3-D models of furniture and casework.
Options galore
The ability to manufacture absolutely identical parts with razor-thin cut lines and corners means that a woodworker can begin to consider using downtime between cabinet jobs to enter new markets. Using a laser in conjunction with the shop’s existing skills and equipment can open up the possibility of building everything from award plaques to games to gearstick knobs or perhaps even jewelry boxes and other high-end gift items.
Lasers can also add a whole new catalog of kitchen upgrades from photo engraved wooden door or appliance panels to glass or acrylic accents. In fact, they’re so versatile that a shop really needs to choose a direction before choosing a laser.
That’s an issue for woodshop owners who are out there shopping for the perfect laser. The technology has come a long way in a short time and the number of options available are staggering. How does a woodworker narrow the field and find exactly what he/she needs and wants?
For example, Universal Laser Systems offers more than 1,000,000 different laser system configurations. Rather than being overwhelmed by the magnitude of that statement, a small woodshop owner should find solace in the fact that Universal Laser Systems — and most other leading suppliers — can design and deliver a system that perfectly suits a shop’s needs. The first step is to visit the company online (ulsinc.com), click on the Purchase page and use the Build Your Laser System app. It walks you through the options, beginning with choosing the material. Type “wood” in the search box and it will take over from there, offering choices that include hardness; whether you’ll be cutting, engraving or marking; part sizes and so on. The site also offers dozens of application ideas.
The learning curve
Adding a laser is usually a comfortable transition from an IT viewpoint. Every woodshop already uses a computer in some way, whether it’s for CNC routing, CAD, estimates, optimizing or even bookkeeping, so the essential computer skills are already in place. While the majority of laser cutting and engraving systems will work on a Windows platform — and many run on a Mac — there are some with their own integral system. For example, Limtech Industries (limtechindustries.com) offers an entry-level “LL” CNC series with an industrial software/hardware configuration that’s built on its lines of larger, industrial CNC routers. Limtech stresses that this means there’s no PC to crash and no software to update.
For small shops or shops with limited plans for a laser, then retailers such as Rockler Woodworking & Hardware (rockler.com) might be a good place to start. The advantage here is that a woodworker can choose from several desktop models. There are some very affordable and easy to learn options that allow a shop to test the concept of lasering without going broke.
One of the least expensive options is to invest in a laser module for a Shark HD3 and HD4 or Piranha desktop CNC from Next Wave Automation. This laser engraver module (Rockler item 59803) retails for $800 and is easy to install and use.
Rockler also offers about half a dozen other desktop and small stand-alone laser engraving and cutting machines in the $2,400 to $15,000 range. At the top is an industrial-sized 51” x 34” CO2 machine from Full Spectrum, equipped with two laser cutting heads with two independent laser tubes, to cut twice as fast. That’s a nice feature: if one head was to fail in the middle of a job, the project could still be completed by the other while parts were being ordered and shipped.
Beyond cutting and engraving
The incredible accuracy of lasers in both engraving and cutting tasks can deliver a degree of precision that is virtually impossible to replicate with any other woodshop equipment. Lasers can even enhance other machines, such as CNC. For example, the British company Leica Geosystems (lasers.leica-geosystems.com) offers a laser that can very accurately measure parts, and the dimensions can then be imported into a CAD program so that a CNC can replicate the part with exquisite precision.
In another application of lasers in the woodshop, SL-Laser makes laser projectors that can take the time and guesswork out of CNC setups and changeovers. They allow an operator to quickly and accurately place pods and fixtures where the laser light shines, eliminating pin stops and enabling the nesting of small parts anywhere on the table. The accuracy of the laser light makes it possible to remove and then reinstall previously cut parts for a second operation. The laser also helps with physical optimizing: it can accurately show a tool-path, which means that smaller blanks can be very precisely placed and this can save some material. And by having the laser light physically project the pod locations, an operator can reduce the chances of costly tool/pod collisions. That can save a lot of money. Maybe even enough to justify the purchase of a new laser.
This article originally appeared in the November 2016 issue.
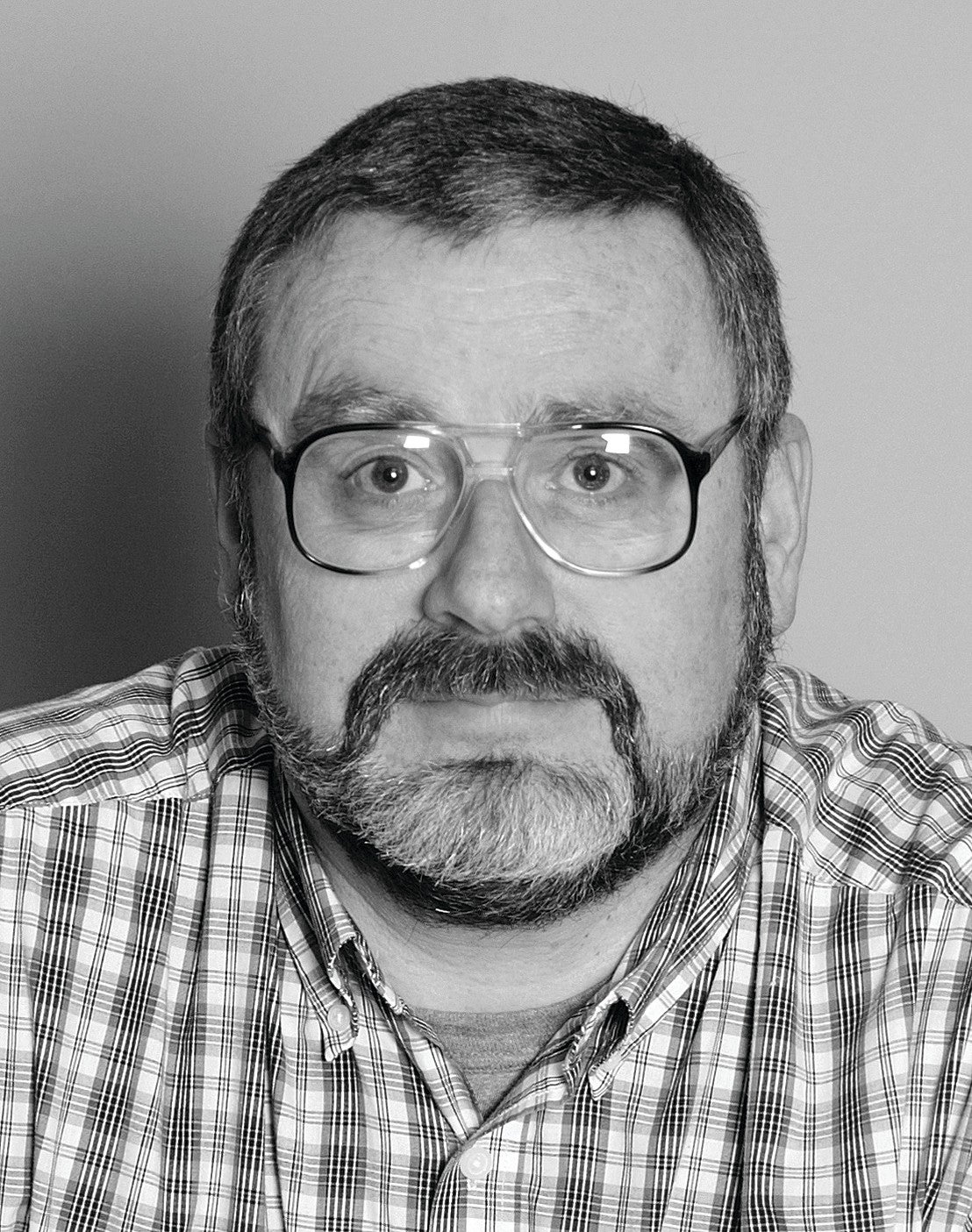