A Trusty Tool
CNC for smaller shops can be counted on for its consistency, proficiency and labor-saving benefits.
Are you making multiples?
That’s probably the most common question that’s asked when a shop is deciding whether or not to invest in a CNC router. One of the strongest attributes of this technology is its ability to repeat accurately. A CNC router can turn out exactly the same part over and over again.
Next in line is its craftsmanship. Furniture artists and other highly creative people have discovered that a CNC can take their shop drawings or sketches and, with a dash of CAD, can usually produce better and more accurate work than they can do by hand. This also applies to prototypes, replicating parts for repairing antiques, making unusual moldings and so on. Plus, it can open the door to engraving cabinet panels, making fretwork or perhaps doing a little sign-making.
The third reason that woodshops get into CNCs is time. The automated router may actually take a little longer to complete a task than it would take a woodworker who is using jigs and a portable tool, but it does the work while that shop owner is doing other things. Buying a small-shop CNC is kind of like hiring an academic relative – they work slowly, but very meticulously. The difference of course is that once it’s paid for, the CNC works for a lot less money.
There’s another reason a woodshop might invest in a small CNC – training. For a couple of thousand dollars a shop can buy a very basic desktop unit and experiment with CAD (design), CAM (creating instructions for the CNC), and concepts such as fixturing and parts management, all before investing money and training in a larger platform.
Among the reasons that small shop owners are hesitant to invest is a reluctance (and perhaps a little fear?) about learning the computer skills required, doubts about whether the machine will stay busy and pay for itself, and the amount of time it will take away from general shop production tasks. There’s also a nagging worry that the machine either won’t be able to complete much of the current workload, or else that it will quickly become obsolete.
Most of those concerns are a little dated.
Is it hard to learn? Software has come a long way and is far more intuitive now than it was a few years ago. There’s an organic set of skills that we have learned from using home computers and smart phones that leapfrogs us past many of the basics in CAD. Even when they’re new to us, the design programs are somehow familiar and far easier to use than they were.
Will it pay for itself? Just like laptops, the cost of a basic CNC router has come way down due to the huge number of choices now available. Competition in this market is cutthroat, and the margins have steadily fallen. That means the initial investment can be quite small, so it doesn’t take more than a handful of jobs to recover it. Your regular customers are going to be interested in your new capabilities, and once you let them know what you can do, they will probably keep the machine as busy as it needs to be.
Will it eat shop time? Yes, initially. But the learning curve is short, and pretty soon it will be saving you time. Besides, getting it up and running is actually quite enjoyable, and very rewarding when those first few parts are made successfully. Most software programs will let you store jobs, too, and build a library. That can save a lot of time because you can begin with something functional and make a few size adjustments, rather than having to start from scratch every time.
Will it do any work? Well, a small CNC isn’t going to build kitchens for you, but it can handle a surprising number of tasks, especially in the area of joinery. It can change the way you build, too. A CNC may encourage a shop to move from fixed to floating tenons or start using RTA (ready to assemble) connector systems. A small CNC can also become a potent partner when milling for pocket screws.
What to look for
There are certain parameters and features that one should keep in mind when shopping for a small CNC. The first of these is the process area, which needs to be large enough to allow the tool in the spindle to reach all parts of the work. In some machines, the process area and the table size are the same, while in others the tool doesn’t quite reach the edges of the table. For example, Axiom Precision’s Iconic series has a table that is 28.4” wide (it comes in several lengths), and the spindle’s X travel (left to right) is 23.81”. Highly reputable manufacturers such as Axiom will explain this up front on their websites and in brochures, while some machine manufacturers tend to use nominal dimensions and the woodworker only discovers limits when setting up a job. Some machines are confined on all sides while others are open-ended or open-sided, so larger parts can be repositioned (tiled). This is handy if you’re making long, skinny parts such as mortised door jambs, or perhaps decorative edges for mantles.
If there’s an enclosure available, there are good reasons for spending a little extra for that upgrade. For example, Techno CNC Systems in Ronkonkoma, N.Y. offers housings for both of its small CNCs, the BT1212 and the HD II. In addition to reducing noise and facilitating dust collection, the company says that these lockable safety enclosures offer protection, especially for students in learning environments and new employees. If you’re working on small parts, the Nomad 883 Pro from Carbide 3D is a fully enclosed CNC that lists for $2,499. The cutting area is 8” x 8” x 3”. The company also offers three larger Shapeoko brand models.
If your budget is in that range, Baileigh Industrial offers three desktop and two floor models ranging from $1,756 to $9,595. The three smaller models are designated as engravers and handle work from 17” x 17” to 20” x 27”, which is larger than most cabinet door panels.
And Zenbot CNC has models that start at just $1,099 (without the router).
Some shops may not even need a benchtop or floor model CNC. Those may be best served by a portable CNC such as the Shaper Origin or the pick-up-and-carry HandiBot from ShopBot. Or they may want to take a look at the full-size portable CNC called the Yeti Smartbench. The HandiBot comes with FabMo software, which lets a woodworker control and monitor the tool from any WiFi-enabled device including a Mac or PC computer, an Android or iOS phone, or any tablet.
Speaking of software, several machines come with their own dedicated laptop or tablet with the controls already on board. For example, the Stinger 1 from CAMaster comes with a control PC that runs Windows 10 PRO and has a 19” LED monitor. The PC is preloaded with WinCNC and is tested with the machine it will be shipped with. The Stinger also comes with Vectric’s VCarve Pro design software. WinCNC provides a customizable, easy-to-use interface to control the CNC using the mouse and keyboard. Button customization allows for simple point and click control, so there’s no need to learn G-code commands. The button and toolbar size can be enlarged so a woodworker can add a touch-screen monitor, and remote control can be added using a wired or wireless hand-held keypad.
Get specific
The spindle is a critical element. The least expensive benchtop models will use a standard portable router, and this is a perfectly acceptable solution if you occasionally prototype or are just learning. Once the shop begins to think production runs, the upgrade to a dedicated spindle makes sense. That’s not as expensive as it sounds. For example, the Laguna Tools IQ benchtop CNC router starts at $7,045 for the 24″ x 36″ model and includes an industrial-grade, liquid-cooled electro-spindle. Despite its smaller footprint, this gives it the same accuracy and cut quality of much larger machines.
In the same price range, Velox CNC makes a couple of interesting small machines with wider tables that are well suited to furniture and sign making.
Minnesota-based Shop Sabre notes that ShopSabre 23 “is the first desktop model with the rigid build of an industrial CNC machine”. It has industrial ball screws on every axis.
Ask about tool-changers. This is a feature that simply won’t be an option with most smaller machines, but if it is, then give it some serious consideration. A tool-changer lets the machine automatically change between different tools (cutters, bits) without shutting down. Eliminating that downtime can be a serious timesaver, especially in more complicated jobs where there are several processes involved.
Will you be making spindles, newels and other round objects? If so, Legacy Woodworking Machinery offers some slightly more expensive but very versatile entry-level machines that can do all the things that most machines do, but also offer a fourth axis that allows a shop to turn between centers. The smallest model, the 3’ x 5’, handles work up to 56” long with an optional extension. Legacy specializes in turning, indexing, spiraling and tapering.
For shops on a stricter budget, there’s a Fourth Axis accessory for the CNC Shark from Next Wave Automation that runs $799. It “gives you the ability to create precision turned spindles or columns that include intricate carvings and designs that will astonish your clients,” according to the company.
Beyond turning, another specialty task for small shop CNCs is engraving and most of the machines mentioned here will do that handily. Vision Engraving & Routing Systems in Phoenix has made a specialty of this, and the company offers a very wide range of routing and lasering options.
Familiar names may be reassuring for some woodworkers, and both Grizzly Industrial and Powermatic offer small-shop CNC machines that are well priced and sturdy. And shops that want a full-size, entry-level machine with no programming required might want to stop by the Thermwood website and take a look at the Cut Ready model.
This article was originally published in the October 2020 issue.
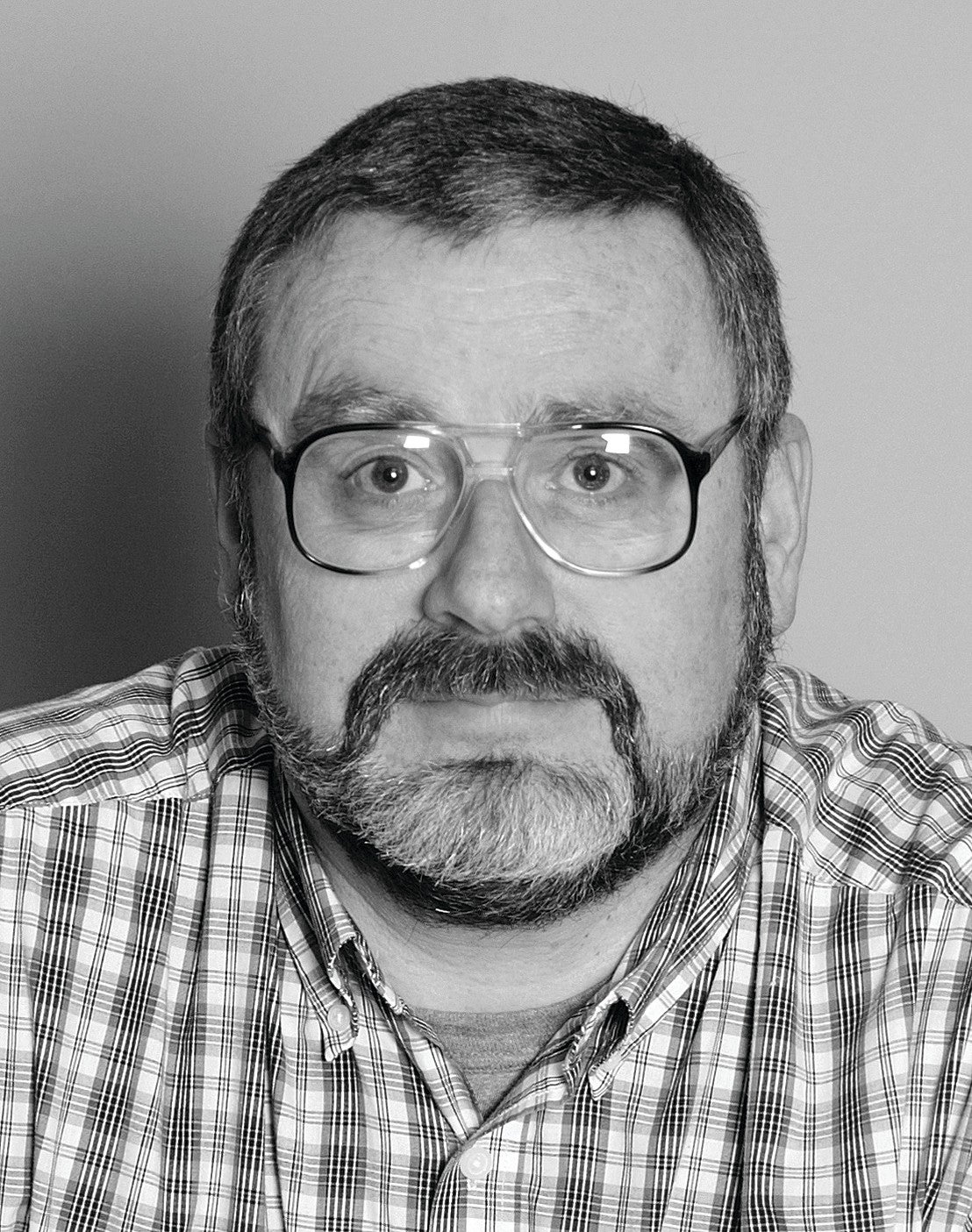