A look at new coatings
Organic greens and sages are the color trends for 2022; manufacturers focusing on UV-cured, powder coat and waterborne finishes
Finishing keeps evolving in terms of the technology we use to apply coatings, the chemistry involved in manufacturing them, and the range of colors and textures that are available. This last is the segment most appreciated by customers, as it’s the most visible and tactile. Over the past few years, the major paint manufacturers have presented woodshops with a palette of Colors of the Year that have leaned heavily on blues, greens, grays, and pastel versions of these. Woodworkers may want to keep those hues in mind going forward, as they’re still quite popular.
Colors of the year
For 2022, Axalta has created Wood Vibes: Blossom, which is “inspired by nature, centering on soft, neutral and soothing color palettes that will induce the feeling of comfort and well-being as the world continues to navigate through unprecedent events and consumers seek healing and harmony”. The company is looking at the restorative power of horticulture, flowers and plants as guiding themes, and the collection introduces white, beige, brown and lavender to balance the ubiquitous blue, green, and gray trends. Wood Vibes also explores Black Rose as “dominant and dramatic, providing boldness and elegance to a home”. The overall feel of the collection is soothing, minimalist, calm and cozy.
The Behr’s COY, Breezeway (MQ3-21), “evokes feelings of coolness and peace while representing a desire to move forward and discover newfound passions. A silvery green shade with cool undertones, the color is inspired by naturally stunning sea glass found on the shores of salty beaches.” Breezeway is part of the company’s Color Trends 2022 Palette, a 20-color collection of soothing shades and warmer tones that run from white to terracotta red. The theme here is also hopeful and optimistic.
October Mist (1495) is the Benjamin Moore COY. This gently shaded sage “quietly anchors a space, while encouraging individual expression through color”. Benjamin Moore says that it evokes “the silver-green stem of a flower”. There are 14 colors on the palette, and they range from luminous pales through botanical hues and primary shades. There’s a handy interactive tool online that lets a designer demonstrate the colors for a client by clicking on a room and then on any of the colors. The tool then ‘paints’ the room.
PPG says that “homeowners, designers, architects and facility managers are craving authenticity, nature and meaningful human interaction after living in a mostly digital world” during the pandemic. The company’s COY is Olive Sprig (PPG1125-4), which is described as a mid-tone, neutral, lush green with an organic green undertone. PPG suggests pairing it with soft rose tones, and the shades, accents, ceiling, and trim palette moves from a very pale sage to an almost-purple pastel. The overall feeling here is a mild, calming, very organic green. The PPG website offers the opportunity to upload a photo and view Olive Sprig in a virtual room of one’s own choosing.
Sherwin-Williams’ COY is also a muted green. Evergreen Fog (SW 9130) is “a versatile and calming hue, a chameleon color of gorgeous green-meets-gray, with just a bit of blue. It’s a simple but sophisticated wash of beautiful, organic color for spaces that crave a subtle yet stunning statement shade.” As with the other trend setters, the immediate reaction to Evergreen Fog is calm, peaceful, comfortable, and quite reassuring. Sherwin-Williams also has an interactive tool on the website where a designer can see examples of this and other shades and colors in various rooms.
Color trends aren’t limited to paint and foil. In December, Iowa-based Old Masters posted a project suggestion to its blog that picked up on currently popular tones and created a small, inspirational project using its Santa Fe collection of wood stains. The palette offers “soft, contemporary stain colors popular with today’s modern style. These unique colors can be achieved by using Old Masters Pickling White as a tint base. Santa Fe colors will produce an intense, vibrant color when tinted with wiping and gel stain. For more subdued tones, tint with fast dry stain and water-based wood stain.” The project was a five-part wall shelf made up of grained and painted hexagons.
Technology trends
LIFE is an environmental program created by the European Union to financially support green economy manufacturing. Just over a year ago, iVM Chemicals (the parent company of Milesi) partnered with LIFE to open a new plant in Parona, Italy, that will produce UV coatings that are made with bio-renewable raw materials. They are from waste vegetation that’s not intended for human consumption. The innovative, highly automated factory is named LIFE BioPaint, and has as one objective the reduction of CO2 emissions by 30 percent a year. Currently, many UV coatings are solvent based. Bob Flexner told Woodshop News readers in 2017 that “UV-cured finishes contain a resin to achieve build, a solvent or substitute for thinning, a catalyst to initiate the crosslinking and bring about the curing, and some additives such as flatting agents to provide special characteristics. A number of primary resins are used, including derivatives of epoxy, urethane, acrylic and polyester.”
This new European effort to create bio-renewable UV coatings is reflective of the larger move in the coatings world from solvent to waterborne bases. One of those is a relatively new waterborne topcoat from M.L. Campbell called Arroyo 1K. This is a pigmented topcoat designed to reduce emissions and environmental impact while improving productivity. Arroyo is a single-component hybrid water-based urethane system for interior use. It was developed to have an unlimited application window, and it reduces waste while eliminating additional mixing steps. It’s Greenguard certified and M.L. Campbell says that it has exceptional self-sealing, film build and film formation properties. It’s a ready-to-spray formula with no reduction or catalyzation required. There are no pot-life restrictions, and very good color stability. It exhibits high performance and chemical resistance per KCMA and AWI standards, and it is appropriate for interior use on kitchen and bathroom cabinets, commercial millwork, and household and office furniture.
Chemcraft’s FlexGlaze Zero VOC (825-48XX) has the same outstanding attributes as the company’s FlexGlaze such as increased open time and “the shortest application time in the industry”. The Zero VOC version is a true sustainable glaze, and the increased open time improves workability and allows it to stay open on large surfaces. It can be top coated sooner than industry standard products, and it can be uniformly blended after the original application.
Last March, Benjamin Moore launched Corotech Command, its newest offering for facility maintenance and property management professionals. This is a single-component, multi-substrate solution that saves time and enables painters to tackle multiple jobs with speed and confidence. It’s a waterborne acrylic urethane enamel that dries quickly to touch in just 15 minutes and enables return to service traffic in 24 hours. Ideal for commercial settings, the durable coating has a block-resistant, tack-free formula, is flexible enough to resist cracking and peeling, and can be applied in temperatures as low as 35 degrees Farenheidt. Formulated for wood and other substrates, the recommended areas for use include safety markers, handrails, stairs, doors, windows, and shelving. Command is available in satin and gloss finishes, plus five ready-made colors. It can also be tinted in more than 3,500 Benjamin Moore colors.
The new Cetol WF 98xx range from Sikkens Wood Coatings is a collection of translucent waterborne single pack topcoats for wooden windows, doors and siding. The coatings are suitable for all kinds of woods and provide excellent application properties, transparency and high durability. Available in different gloss levels and appearance, they deliver no dirt pick-up and excellent leveling. They also come with a seven-year extended warranty (two years for light colors), and they can be tinted using Aquaflex tints. The low build nature of Cetol WF emphasizes the natural qualities of wood.
In these days of global health issues, Emerald.com published a recent study that was designed to explore the benefits of adding citric acid to epoxy acrylate, which is commercially used in UV curable coatings. Citric acid (CA) is economical as well as being a bio-based compound that possess an antimicrobial activity. The purpose of the research was the preparation of a CA-based oligomer which could be incorporated with epoxy acrylate and tri (propylene glycol) Diacrylate (TPGDA) to form a UV curable coating, and the subsequent study of its antimicrobial property. The results exhibited good mechanical, chemical and thermal properties, and the zone of inhibition against staphylococcus aureus bacteria was enlarged when increasing the content of CUV in the coating formulation.
Taking a powder
There’s a strong trend in wood finishing toward powder coating, and last spring AkzoNobel opened a new research center in Como, Italy, to develop products for precisely that niche. The new facility includes an application lab, a process lab, and an analytical and testing lab. The center is “dedicated to delivering low cure powder coatings for use on heat-sensitive substrates such as MDF, plywood, thermoplastics and composites”. The focus is on developing an expanding portfolio of low cure solutions including low bake, UV and ultra-low bake (ULB) powder technologies so that woodshops can use less energy during production, speed up the coating process, and boost their sustainability profile. And responding to those benefits, AkzoNobel now has plans in place to open additional R&D centers in Asia and North America.
Although powder coating on MDF and other wood products is one of the fastest growing segments of the finishing industry, it hasn’t had an easy start. Wood, unfortunately, is not as well-behaved as the metals used in other manufacturing where powder coating is ubiquitous. Wood expands, contracts, splits, warps, twists and cups, among other mischievous trends. Even resin bound MDF and multi-layered plywood tend to inherit these qualities to some degree. Plus, cabinet shops need to be able to coat more than flat panels. Finishes need to be durable and well-seated enough to survive wear and tear on profiled edges, exposed corners, and even horizontal surfaces. How many times does a customer open a base cabinet door by reaching for the top edge rather than bending down a few more inches to grab a handle? Those edges are going to be washed and perhaps even scrubbed every now and then with abrasives, and if the hinges aren’t soft close there’s an impact and a shock every time the door closes. The coating needs to be able to survive all of that. Powder coatings are generally resistant to water, scratching, and even some level of heat.
Successful powder coating on MDF starts with using the highest grade of sheet stock available to avoid chipping, delaminating, bowing or other problems over time. Even the resin used by the board manufacturer needs to be somewhat heat tolerant. Then, because the process is based on an electric current passing through the MDF, the doors or panels need to be a bit damp. Not wet, but humid. There are conductive coatings for this that can be applied by a gun, a robot or even by hand, but it’s a time-eating process and the actual coating then needs to take place quickly before the humidity evaporates. That’s especially critical when the MDF is pre-heated to enhance adherence. Once applied, the powder needs to be cured quickly, too. That can be done with a low temperature oven, or a UV system. So, timing is critical at every stage. Essentially what is happening is that the woodshop is applying a thin powder (a solid) to a surface, and then melting it into a liquid so that it will flow into minute pores on the surface and then build up as a level film that crosslinks (cures and hardens) into a continuous coating. Once applied, the steps are melting, flowing, curing, and cooling.
Advances in all these stages have made powder coating possible in woodshops. A couple of the bigger changes have been the introduction of low-temperature, fast-curing powder, and the idea of using both infrared and hot air in the same oven. The investment in machinery (both applicators and ovens) can still be quite substantial, so many smaller shops are opting to have specialists such as BTD (btdwoodpowdercoating.com), DVUV (dvuv.com) and other experienced outsourcing companies handle the coating for them. Powder coating offers a fast cure, very little waste (almost all the overspray can be harvested and reused), few if any airborne emissions, an exceptionally tough surface, seamless joints, a vast array of color choices, and even the ability to add various grades of texture. A shop can offer options such as hammered, metallic or even pearly finishes. And the environmental advantages can be a significant marketing tool. Traditional spray coatings can produce a lot of overspray, and thermofoil can also generate a lot of wasted material. However, there is some impact from powder coating on the shop’s carbon footprint because of the use of heat to melt and cure.
In other news…
RPM International is a specialty coatings manufacturer with brands that include Watco, Rust-Oleum, Zinsser, Varathane, and Dap. In January the company announced that its Varathane Super Glaze, the pourable epoxy system from Rust-Oleum, is now available in pre-tinted colors. Woodworkers can now avoid the task of mixing clear epoxy with dye because Tinted Super Glaze already has color added, so no additional mixing is required. The pourable epoxy resin delivers a high-gloss finish that’s as thick as 75 coats of varnish. It leaves surfaces durable, waterproof and resistant to heat and chemicals, and it’s ideal for indoor projects such as tabletops, furniture, and bar tops. It’s available in clear, Charcoal, Classic Gray, Aged Wood, Turquoise and Metallic Blue.
For shops that take a while to use cans of spray booth product, Bloxygen.com is now offering free shipping on all orders that are placed directly on the website.
Illinois-based Aqua Coat offers ecofriendly waterborne coatings and the company added a video on its website (aquacoat.com) last fall about a process called cerusing, or liming. This is an old technique that has found new life of late, and it’s designed to draw out the detail and highlight the beauty of a wood’s grain. The open grain is lightened up and accented against a darker, contrasting base color. On some light species, the opposite effect can be achieved. It’s a type of decorative finish that involves using different colored pigments to highlight a wood’s natural grain pattern, and the process is relatively straightforward. In the Aqua Coat video, the grain whitening technique uses the company’s white cabinet grain filler.
Rubio Monocoat (rubiomonocoatusa.com) also offers a blog entry on how to create a cerused wood finish. The company says that “liming wood originated in the sixteenth century in Europe, where a caustic paste of slaked lime (not very healthy stuff) would be rubbed into the open grain of the wood to deter wood-boring insects. This lime washing somehow resulted over the centuries in a decorative look that is popular among modern-day designers and decorators.”
What goes around…
This article was originally published in the March 2022 issue.
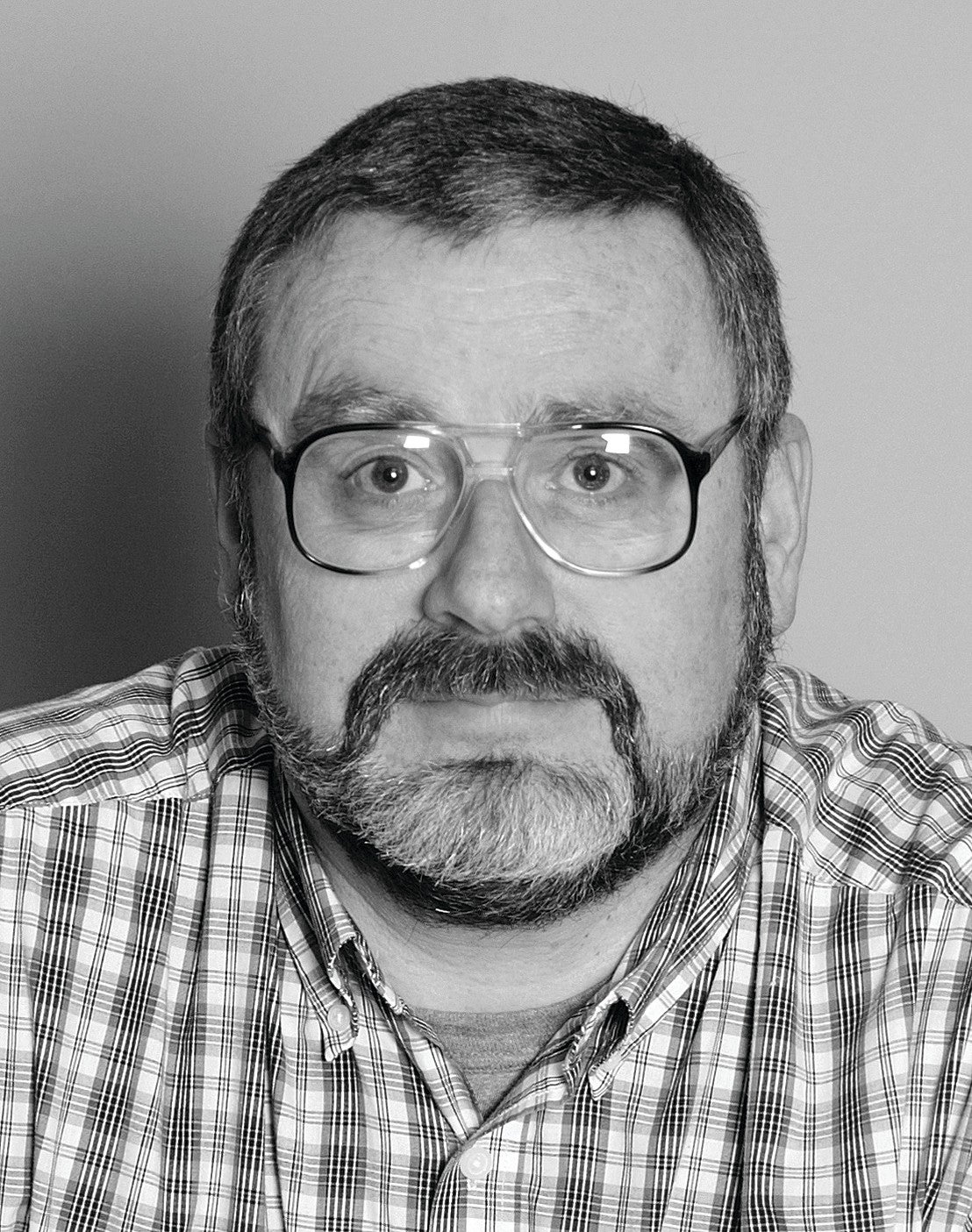