A link to the past
Ten miles north of Mitchell, S.D., a ring-necked pheasant crosses the gravel between snowy ditches. Beyond her is a wide lot surrounded by barns, sheds, a couple of newer metal…
Ten miles north of Mitchell, S.D., a ring-necked pheasant crosses the gravel between snowy ditches. Beyond her is a wide lot surrounded by barns, sheds, a couple of newer metal buildings and, to the south, a handful of lonely cottonwoods hugging a draw. This is "Dances with Wolves" country. Wide open, endless sky. The only sound is wind.
And then a wheelwright's hammer cracks the silence.
Inside the biggest building, the crew at Hansen Wheel and Wagon Shop are repairing and reproducing horse-drawn vehicles. Everywhere one looks, there are remnants of the 19th century - freight wagons, surreys, stagecoaches, sleighs, even some working cannon. There's a paint room, a leather shop and a forge, but the heart and soul of the operation is the huge woodshop.
Back in high school, owner Doug Hansen fell in love with horse-drawn vehicles. His hobby became a business in 1978, and for the last 30 years his wife, Holly (the company accountant), has helped him grow the shop into one of the country's leading builders and restorers of wagons and carriages.
According to Hansen's tour guide - retired teacher and current carpenter Richard Henn - the distinction is important. "Wagons haul freight," he says, "and carriages haul people." The half-built stagecoach behind him is a carriage and the shop has built a whole lot of those for companies such as Wells Fargo, as well as museums, military re-enactors, tourist attractions, private and institutional collectors and, of course, restorers. The business is one of a small handful that still builds custom wheels and it also sells a huge array of parts from brakes, bows and doubletrees to brass sleigh bells.
Built to last
"Most of our raw wheel hubs are turned on the lathe from white oak," Tim Hoffman says. He has interrupted his finish work on the door of a sheep wagon to explain. "The spokes are formed and shaved by hand and they're oval in shape, which makes them stronger. The outer rim of the wheel is made up of several short arcs called felloes." The wagon he's working on is a precursor to the modern RV, although it is used for work rather than recreation. Equipped with a small wood stove, a water barrel and stark living quarters, sheep wagons have been home to herders in the foothills of the Rockies (a day's drive west of here) for more than a century. The original versions are prized by collectors who value both the economy of design and the intelligent craftsmanship that has allowed them to survive not only for decades, but the endless wind, harsh winters and drought-ridden Western summers.
There is a constant buzz of activity in the shop. The crew is currently working on building several new stagecoaches, restoring a handful of buggies and getting ready to apply final paint to several working cannons. Structural elements for these vehicles are usually milled and shaped from kiln- or air-dried ash or hickory, while much of the paneling is kiln-dried poplar. There are 12 employees and Hansen is always looking for another skilled woodworker who has a special bent for the intricacies of this peculiar trade.
"It takes someone special," he laughs. "We do a lot of half laps, mortise and tenon joints, even dovetails - but almost none of them are at 90 degrees."
Way in the back of the shop, surrounded by massive mills and metal lathes, a new hammer sounds. This is the blacksmith's shop where, for the last nine years, Joe Westberg has teased and trained soft iron into the hardware of his trade. On this day, his task is hand-forging straps and hinges for two large finger-jointed poplar boxes that will hold ammunition for the cannon. Modeled on post-Civil War originals, the ironwork mirrors the quality wrought by those old-time artisans.
Historical accuracy is paramount here. Hansen is a walking encyclopedia of carriage building and he grows animated and intense when poring over original blueprints from renowned designers such as Ed Murphy, who established the Pontiac Buggy Company in Michigan in 1893. (Yes, that Pontiac. The company didn't switch to automobiles until 1907.) A surprising number of household names began in the wagon trade, including John Deere, Studebaker, International Harvester and Sears Roebuck.
In the main shop, carpenter Andrew Fridley is painstakingly replacing trim around the door opening of a small buggy, removing a few inches at a time with a back saw and hand tools. Like most of the crew, Fridley is adept in several areas including casework, upholstery and leather.
All about authenticity
About 40 percent of the workload is restoration and the rest is replication. The shop builds about three new wagons a month, including some scaled-down models. That's made possible by what they have learned during decades of restoring. There's a boneyard out back, but there are very few pieces in great condition, so the original parts are mostly used for patterns. Hansen can analyze the engineering of an old vehicle from a photograph, size the axles and, from that base, he can begin to re-create missing specs.
"It's a combination of mechanical engineering and knowing the craftsmanship and style of a specific era," he says. "Our teachers are the original builders. And doing it their way lends authenticity. For example, when fitting two parts together, nicer blends will usually come from a spokeshave than a router. Those men learned on the job and that's how we do it still. When somebody comes here to work, we build old skills on top of the newer ones."
He leaves for a minute to welcome a group of Amish farmers who are here to discuss the purchase of some parts. When he returns, he is still in full stride.
"There is a delicate balance between aesthetics and engineering, more obvious in carriages than freight wagons. The load that a horse can pull is what determines many of the dimensions of our wooden parts. We need to keep the structure sized as small as we can to still do the job and be reliable. Even after all these years, some of the components still surprise us: they always seem lighter than we assume they will be."
The thread of his discussion is based on the fact that steel was expensive 130 years ago and wood was relatively cheap. Hence, older wagons have much less iron or steel in them, but that changed through the years.
"There was an evolution where wood became secondary," he says. "By the 1920s vehicles were almost entirely metal, with only a few wooden accents. The original automobiles, mostly made of wood, were just a step up from a wagon. That evolving trend allows me to look at a vehicle today and determine approximately when it was built. Rules imposed by the weight of materials had a lot to do with the aesthetics and style of vehicles, too."
Hansen's shop occupies a niche within a niche in the carriage world. They specialize in both new and used heavy Western vehicles - stagecoaches, chuck wagons and prairie schooners. Along with their repair work, the company usually has about 50 vehicles for sale, from freight and chuck wagons to carriages and coaches.
Hansen Wheel and Wagon Shop is a member of the Carriage Association of America (caaonline.com), and the National Stagecoach & Freight Wagon Association (www.stagecoach freightwagon.org).
Contact: Hansen Wheel and Wagon Shop. Tel: 605-996-8754. www.hansenwheel.com
This article originally appeared in the April 2011 issue.
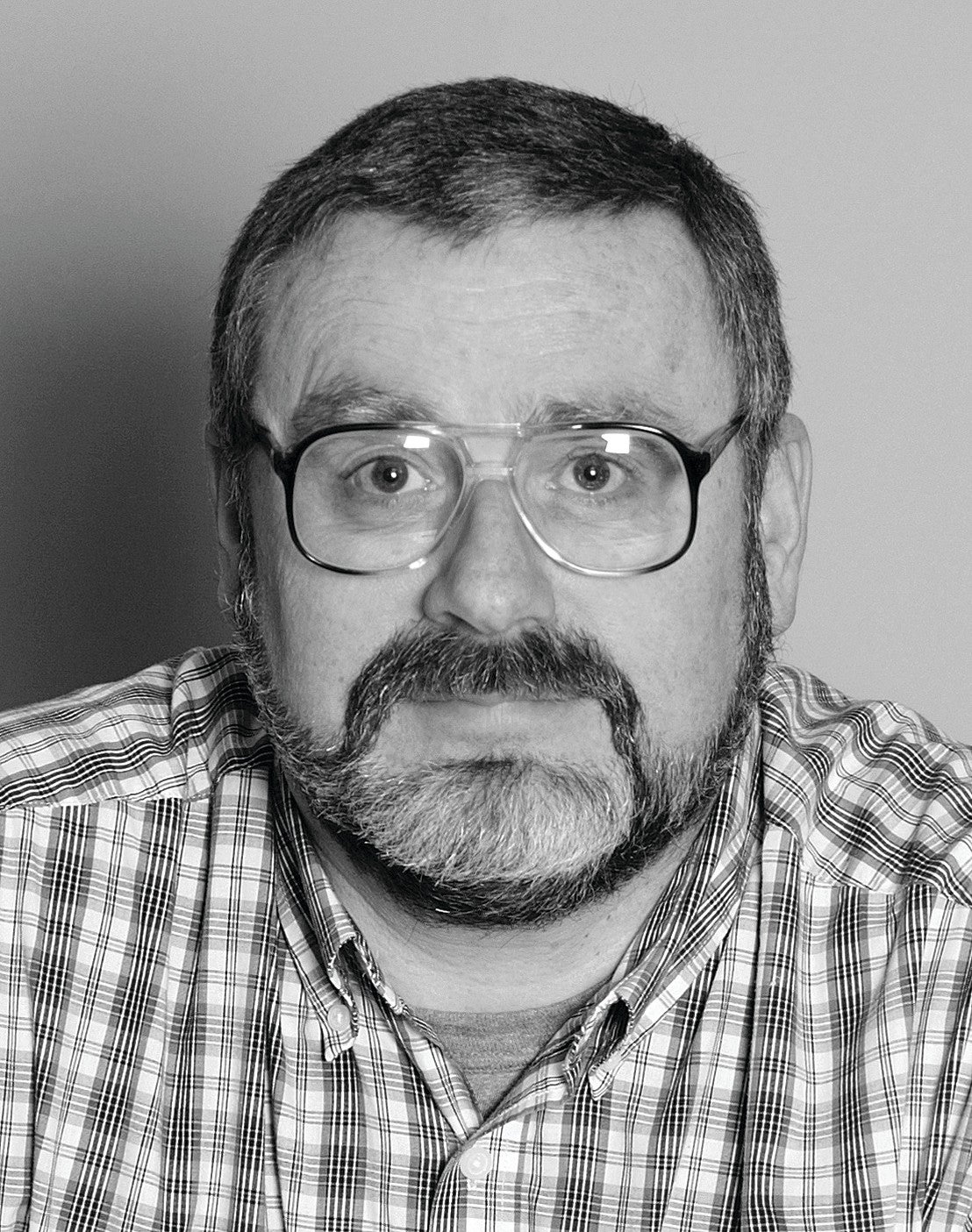