A labor-saving option
Thermofoil is a solid value for customers and makes life simpler in the shop
Bringing thermofoil in-house is a viable option for many small- to medium-sized woodshops because of advances in the technology, both in terms of machines and patterns. Foil makers are constantly introducing new solid colors and woodgrains, and the machines are getting small, more powerful and more efficient.
The theory is relatively simple. The shop mills one-piece flat or panel MDF doors on a CNC, and then wraps the backs first and then the fronts with vinyl in a heated, vacuum packing machine. The doors and drawer fronts are laid out on the bed of the machine, often with sophisticated platens that raise them off the surface or make it easier for woodworkers to apply or handle the hot-melt adhesive used to create a bond between the foil and wood products. After baking, the parts are trimmed from the sheet and turned over and the process is repeated for the front faces. The vacuum and heat suck the foil tight to the door profile, revealing flat or raised panels or details such as arched tops.
The advantages of thermofoil are that the material can be significantly less expensive, and the process is less labor-intensive than more traditional assembly and coatings options. One or two workers can turn out a full set of doors and fronts in a day, and there’s no overnight cure or multiple coating required.
The biggest disadvantage is that thermofoil is shaped by heat, and usually lies on an MDF core. The foil is susceptible to heat after installation such as hair dryers, coffee machines and toasters, and if the seal deteriorates the MDF core may absorb moisture and become distorted or swollen. It can also meet some client opposition as there is a conception that these doors are a low-end solution for a high-priced custom job.
Other concerns are handling vinyl with pre-applied glue, dust or dirt that telegraphs through the vinyl, and delamination. Sometimes, the doors can be repaired with contact adhesive, but the normal solution is replacement. And that can be a problem if the vinyl pattern or color has been changed or discontinued, or if the tone or shade of adjacent doors and fronts has reacted to an environmental influence such as direct sunlight or cleaning chemicals.
But overall, thermofoil doors can really simplify life in the cabinet shop while offering the customer a solid value.
Options
Vac-U-Clamp (vacuclamp.com) in Oceanside, Calif. offers the FT 900 thermofoil vacuum press that can handle work up to 52” x 105” and it has a low-profile top that decreases the interior volume. That delivers optimum heat distribution, while shortening the cycling time. The machine has 24,000 watts of heating power; which is delivered through infrared quartz tubes. The top tubes are curved to more evenly distribute heat. And there’s a tube at each end for complete, even heating of the film. The temperature of the film is accurately measured by an infrared sensor, and there’s a centrally located 300-watt interior light so the operator can visually check progress through the front viewing window.
In a Vac-U-Clamp exclusive, optional platens are bonded with a very high-tech non-stick coating that prevents pre-glued film from sticking to the platens during processing. That makes removal of excess film a snap. Previously, shops that wanted to use pre-glued film had to spray the platens with a food-type non-stick spray- which worked but was a mess and required frequent repeat applications. The new platens can save a lot of set-up time between cycles and contribute to both a cleaner work environment and better results. Experienced users will also appreciate the Constant Row low level of vacuum, which helps eliminate wrinkles.
The FT 900 also comes with a 48-cfm vacuum pump and a new IDEC 8.5” color touchscreen that can handle up to five separate programs for different kinds of film.
Vac-U-Clamp also makes the larger FT 1200 that’s designed to turn out 8,000 to 12,000 panels a week, compared to the FT 900’s 1,000 to 1,500 capacity.
CNC Factory in Santa Ana, Calif. offers the Cyclone 4896 thermofoil press. Highly automated, the controls on this short-cycle 3D press allow a single person to produce over 300 pieces in an eight-hour shift, the company says. It has a one-button digital monitor and a mobile footprint. It’s powerful enough to produce virtually any 3D shape using PVC sheets, rigid sheets, PS sheets, acrylic, ABS and wood veneers.
Shops that need to veneer shaped parts might want to take a look at the MVP 300 membrane press from the Felder Group (felder-group.com). The membrane can stretch up to 700 percent as vacuum pressure is applied from below. Then heat from above cures the glue and delivers parts in just minutes, according to the company.
Black Bros. has locations in Mendota, Ill. and High Point, N.C. The company supplies two ranges of machines. Its Thermaformer is suited for heavy or thick parts such as desktops and counters. The larger Thermolaminator has Teflon coating to handle pre-applied adhesives, an automatic door and panel trimmer, and a modular design that allows for increased capacity as a shop grows. It operates with or without a membrane and has a touchscreen panel with a modem for diagnostics.
JKL Machinery (jklmachinery.com) in Brighton, Mich. offers a full range of production equipment for panels including presses for veneer, laminate and composites, as well as glue spreaders, thermal heating units and veneer saws.
Global Vacuum Presses (gvpna.com) is in Valencia, Spain and has offices in Lincoln, Neb. The company’s G-TVP model does 3D foil thermoplastic lamination of both films and sheets. It features a PLC automation system, operated by a touchscreen interface, that offers the possibility of temperature curves and vacuum pressure steps.
Smaller choices
Martin Woodworking Machines Corp. (martin-usa.com) in Charlotte, N.C. offers a number of Barth brand vacuum press options including the Corvus-5 and W models that have a small footprint. The S is a wheeled unit that flips from horizontal to vertical, so it can be moved around the shop if needed. An optional cover plate is not only a protection for the membrane, it also offers a flat work surface. Shops making extra-long or a large number of parts may be interested in the Taurus, which is the flagship of the line. It combines flexibility in part processing and mass production by offering the largest possible workspace. With lengths up to four meters and custom lengths beyond that, these presses are designed for big projects. The elasticity limits of the membrane can also be customized so that higher and longer parts can be glued in a convenient way.
Quality Vakuum Products (www.qualityvak.com) in Hudson, Mass. offers smaller solutions that are popular with fine furniture builders and luthiers. The company supplies both pneumatic and electric presses, and numerous stock bags in both polyurethane and vinyl. The bags are made in-house, so custom sizes are not a problem.
Lenderink Technologies, Inc. (lenderink.com) offers wood veneers, dry film, web and powder adhesives. The company also supplies laminating equipment for flat panels.
Smaller woodshops that only have an occasional need for thermofoil doors have a lot of choice when looking for an outsource. Many of the standard door suppliers can handle custom shapes and profiles, so a shop can try outsourcing for a while until the volume grows enough to consider bringing this function in house.
This article originally appeared in the May 2020 issue.
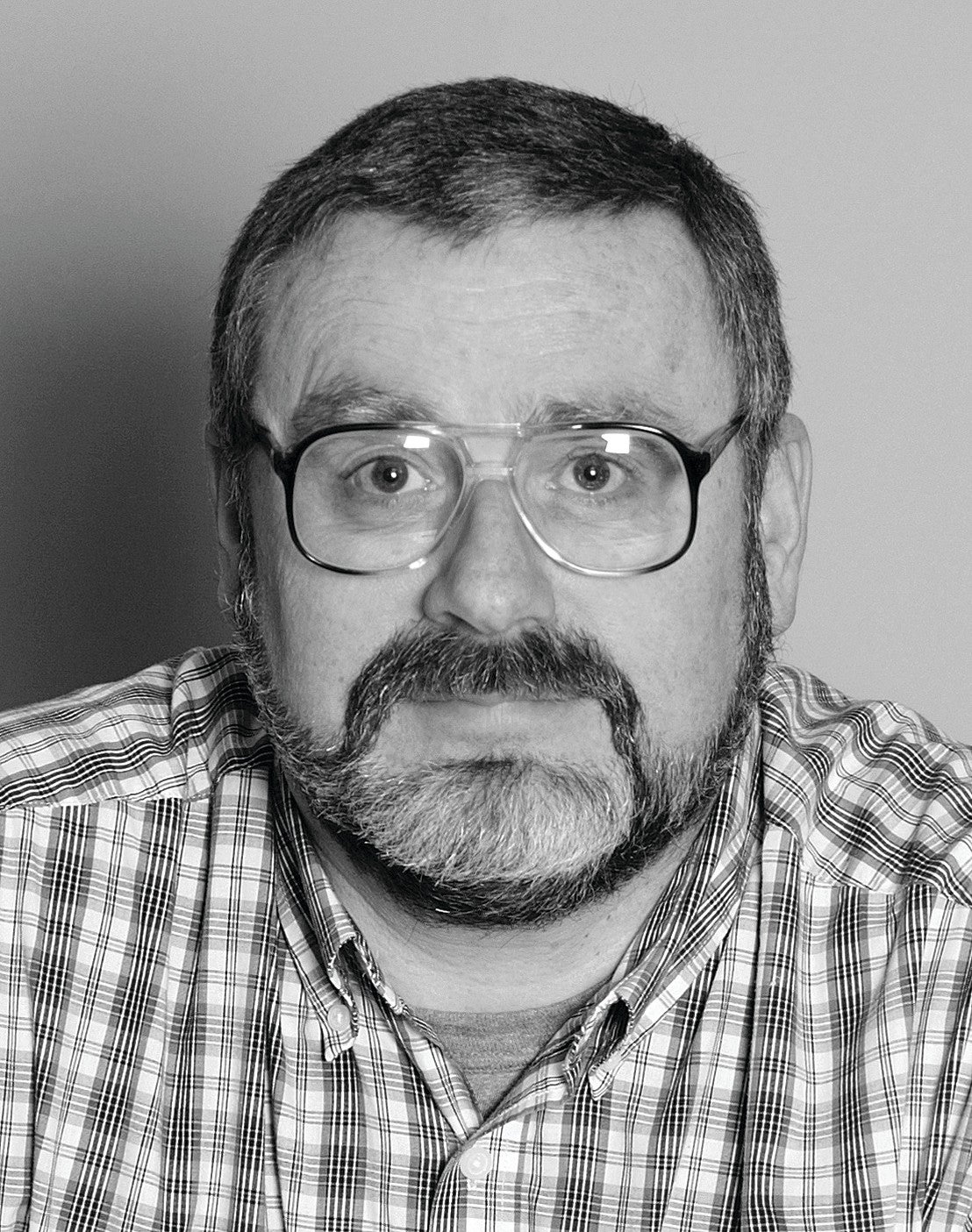