A handy power source
Pneumatic tools are a great addition to woodshops, especially for creative clamping solutions
Despite the revolution in power tools that has been delivered by better batteries and brushless motors, there’s still a solid place in the woodshop for air-powered tools. Indeed, some of the more interesting evolutions of late have been hybrid adaptions where pneumatics and batteries have been combined to produce more portable yet powerful solutions, such as nail guns that use batteries to compress air in onboard cylinders.
Take, for example, Senco’s Fusion technology that combines pneumatic power and performance with the ease of a cordless tool. It consists of six main components – a battery, a gearbox, an electric motor, a lifter, a driver, and a cylinder of pressurized air that contains a piston. The motor and gearbox turn the lifter, raising the driver above the piston. This stores energy, so that when a woodworker pulls the trigger, the nail is driven within nanoseconds. The lifter then picks up the driver and stores energy for the next shot. The technology repeatedly uses that pressurized air to create the same rapid response time after time.
Air under pressure has always been a handy power source in woodshops, and one area where this is especially adaptable for smaller shops is in clamping.
Fixturing and clamping
Whether a woodshop is operating traditional machinery or CNCs, there’s always a need for creative clamping. In casework shops, pneumatic clamps are often placed in a single location and set for a standard material thickness where they can be used for sawing, routing, shaping or hardware mortising. A pneumatically operated clamp can help cut production times, and it may also reduce carpel tunnel syndrome. Unlike vacuum tables, toggle clamps and cylinders don’t use much air, plus they’re quite affordable and easy to both install and operate.
Finding pneumatic clamps is easy. For example, Destaco (destaco.com) offers toggle clamps with air-actuated cylinders to operate the clamping action. These are ideal for quick clamping in repetitive production operations, and they can also be used on short run jobs with temporary fixturing. They have the same basic design and operation as manual hold-down or straight-line toggle clamps, and they have the familiar toggle-lock safety feature that keeps them mechanically locked even with a total loss of air pressure. They come in a variety of holding capacities, are completely self-contained and require only a compressed air hook-up and an optional on/off valve (called a flow controller or switch) to operate. The company also offers a power cylinder that has two steps. The first moves the rod into position and the second applies clamping force. The rod force in the forward stroke is that of a traditional pneumatic cylinder, and the power stroke (clamping) offers a mechanical advantage of up to 10:1.
Among the newest pneumatic woodworking clamps on the market is the PC-1 from Woodpeckers (woodpeck.com). Designed for the company’s Multi-Router, this pair of toggle-operated hold-downs could be adapted to many assembly and milling processes because the cylinders are mounted on vertical columns that just attach to threaded holes in the work table.
Woodworkers Supply (woodworker.com) offers several air cylinders for shops that want to build pneumatic clamps, including double-acting horizontal and vertical clamps, plus a 1-1/16” diameter cylinder. The clamps require switches and they have standard 1/8 NPT ports, but the cylinder already includes two flow controllers, a mounting bracket, a mounting nut, an aluminum foot, a non-marring foot pad and a jam nut, and it’s available with 1”, 3” and 4” strokes. There are lots of videos online where woodworkers use such air-powered small clamps to upgrade their miter saws, table saw sleds and other equipment.
Several manufacturers also offer panel clamps that use air cylinders to apply both edge pressure and panel flattening. For example, James L. Taylor (jamesltaylor.com) has developed the 180A-M2 accessory that flattens bowed panel stock when using one of the company’s regular edge-glued panel clamps. You basically load the machine with glued-up parts, snug up the sides and then deliver up to 1,500 lbs. of downward pneumatic pressure to keep everything flat while the assembly cures.
There’s another airpower option for clamping work on a CNC beyond using a whole table grid or pneumatically operated mechanical clamps. Better Vacuum Cups (bettervacuumcups.com) offers a new flat table vacuum cup, the DS75180, that works on top of a solid spoil-board and elevates the work by 35mm off the table. This lets the woodshop work on edge details. The cup is 75 x 180 x 35 mm and can be used to work on parts as small as 3”.
Air power
Ever been on a construction site where nobody talked because all the nail guns were running off noisy compressors? Well, many of the bigger guns for framing and roofing are still using pneumatics but batteries are eating into that market. Fortunately, most of the respected and familiar manufacturers still make air guns too, and most have just added quieter but often less powerful cordless versions to their catalogs. Most framing crews still like their pneumatic guns, because air power lasts all day without having to recharge or replace the power source, and it still delivers the biggest punch to sink those larger nails.
In the woodshop, the focus is more often on brad and pin nailers, and here pneumatic guns use such a small amount of air that the compressor cycles much less frequently. But there’s no need to listen to the pump anymore with the advent of quiet compression. For example, California Air Tools (californiaairtools.com) makes the CAT-20040DCADC, which is a 4-hp, 20-gallon oil-free air compressor with its own drying system, all housed in a soundproof cabinet.
Other reasons for choosing pneumatic brad nailers over cordless might include low initial prices, no chargers and sheer ruggedness. Pneumatic guns are usually simple and tough, and of course they never run out of juice. Recently the better models have added improvements such as directional exhaust, swiveling air connectors, built-in LED lights, and easy tool-free jam removal. That means choosing a pneumatic gun is no longer just about the magazine capacity, and most of these new features really do make jobs easier and more productive.
One woodworking activity that does use a lot of compressed air is running a random orbit sander, but the other side of that coin is that a pneumatic sander has an awful lot of power. Tools such as the Grex AOS368 (grexusa.com) can deliver a beautiful surface in a very short time. This is a compact, smooth operating and powerful random orbital sander that takes hook and loop paper on 1”, 2” or 3” diameter pads (the 1” pad and 3” are optional) and addresses the work at a very comfortable 105-degree angle. And there are a couple of extensions available for reaching into tight spots.
Pneumatic notes
Moisture in compressed air has always been an issue, and if not taken seriously and removed it can cause expensive damage to equipment, parts and even finished products. LaMan Corp. (www.laman.com), a provider of filtration and lubrication products to the pneumatic industry, advises that the most effective way to remove moisture from air lines is to use filters that are integrated at the compressor, or preferably at the point of use. “Because condensation, rust, dust, scale, and other contaminants can accumulate along the compressed air line between the compressor and the tool,” the company says, “filtration at the point of use is generally preferred.”
For furniture shops that harvest their own lumber, Gardner Denver (gardnerdenver.com), a provider of compressors, blowers and vacuum pumps, notes that a vacuum pump allows preservative to penetrate much deeper than soaking alone. The use of vacuum dryers in conventional wood drying chambers can reduce the typical drying time from several weeks to a few days. During the drying process, pressure in the chamber is gradually reduced to the minimum. The chamber is pressurized with steam and the air is extracted to prevent cracks and color changes in the wood that can be caused by too high an oxygen content.
Delivering compressed air to tools got a little easier with the introduction of Aircom’s new multilayer pipe (aircomsystem.com). It can overcome or bypass obstacles such as pillars or corners without needing to use flow-reducing elbows and it offers quick and easy connections to system elements such as drop legs, branch plugs, aluminum wall-mount manifolds or workbenches it has both inner and outer bending springs and a hydraulic bending gun. Diameter sizes available are 16, 20 and 25 mm.
Resources
Woodworkers looking for air-powered solutions for delivering coatings can check out the woodworking page on the Carlisle website (carlisleft.com) where they will find a huge array of pneumatic tools and complete systems.
The Jenny lines of portable and industrial stationary air compressors are shown at jennyproductsinc.com. Mi-T-M’s lines are located at mitm.com.
The entire Ingersoll Rand compressor line-up can be found at ingersollrand.com, where woodshop managers can also see the company’s dryers, filters, and controllers.
Mirka offers a large selection of pneumatic sanders – from spot sanders to two-handed 8” diameter tools – at mirka.com.
And for Rolair jobsite compressors that include everything from lightweight carry models to wheeled and stationary gas and electric compressors, visit rolair.com.
This article was originally published in the December 2021 issue.
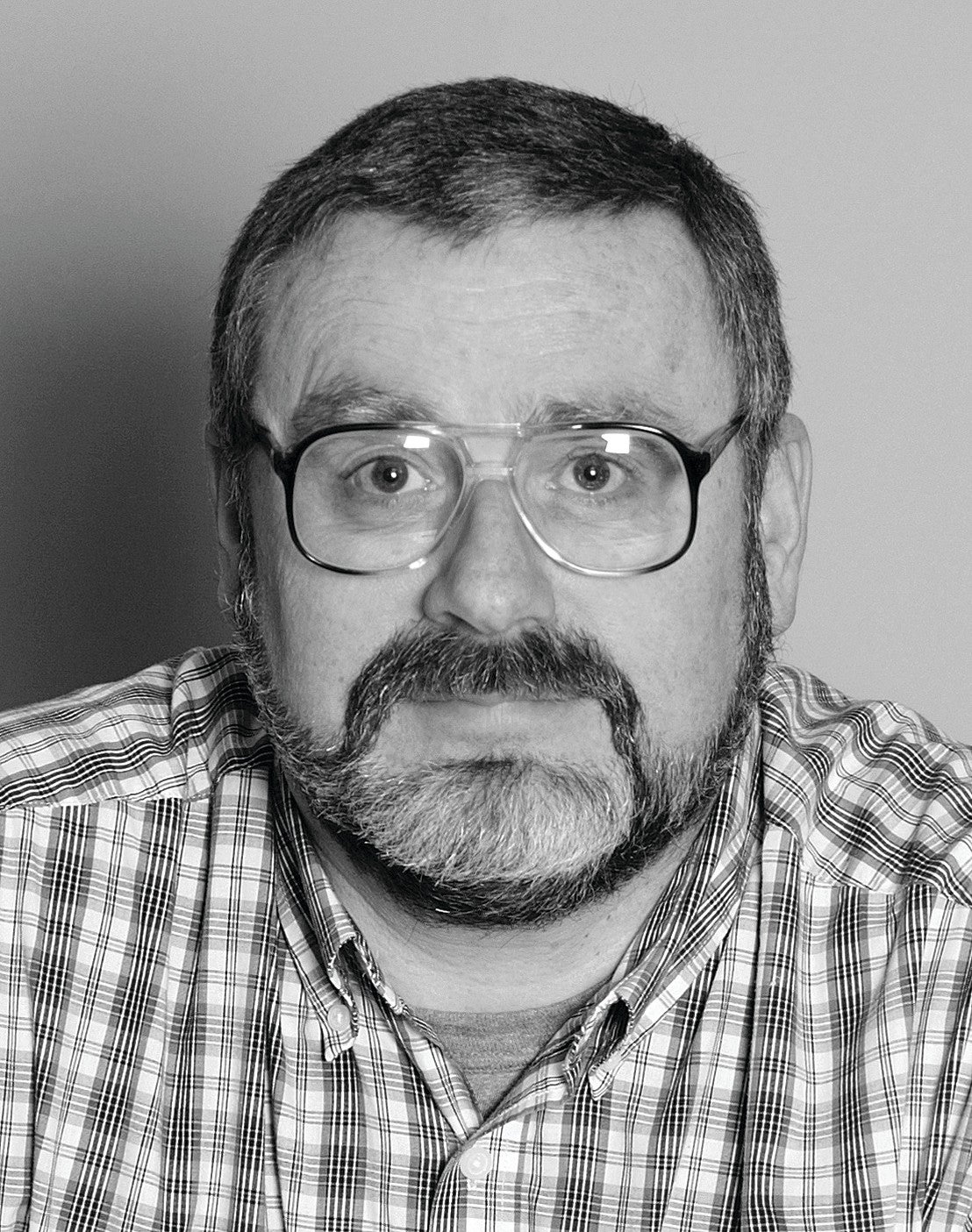