You need a sharp eye to treat your blade
Quality saw blades don’t come cheap, so owners need to take the time to determine who they trust to sharpen and clean them {loadposition position10} Good carbide saw blades are…
Quality saw blades don't come cheap, so owners need to take the time to determine who they trust to sharpen and clean them
{loadposition position10}
Good carbide saw blades are expensive and shop owners need to be careful who they hire to sharpen them. An inexperienced or ill-equipped sharpening shop can destroy a blade in seconds, while a good sharpener can reduce downtime for blade changes and also extend the useful life of blades.
The first question to ask is whether blades even need sharpening. C-4 carbide teeth are a delicate balance between hard and brittle. The addition of elements such as tungsten to the steel creates a material that is extremely hard, but also has the ability to shatter, especially along its refined edges. This means that carbide teeth are designed to cut by attrition: they approach the work at an almost vertical angle (compared to, for example, the forward-leaning teeth on a high-speed steel rip blade). The flat face of the tooth slams into the wood and removes waste by force of impact, rather than by mere abrasion. Because of this, carbide teeth tend to run hot and this leads to an accumulation of resins and other detritus that clings to the sides and back of each tooth. Quite often, a cleaning is all that is needed to restore a good blade to full function. Once the accumulated resins built up around the trailing edge of a tooth are removed, the fine edge is revealed and allowed to do its job again.
Cleaning the blade should also be the first step to look for in a sharpening shop. If your sharpener immediately mounts your blade on a machine and begins to sharpen it, he is addressing only the front face of each tooth and ignoring the sides and back. Some shops like to sharpen first and then clean. But this means they have declined to give the blade a proper visual examination before milling and they might miss small chips, fragmented edges and perhaps even loose or split carbide.
Is it balanced?
With resins and grime removed, the next step a technician needs to take is to check the balance of the blade. It's OK to ask whether the shop has a blade balancer. This is a precise device that tells whether the blade is balanced or bent. If a blade has 80 sharp teeth but they're not in line (for example, the plate may be warped), the blade will wobble and create tear-out and wide kerfs and might even be dangerous. The standard manual version of a balancer is a simple cone. As the blade is slowly spun, a micrometer reads the alignment of the teeth. Many shops now have electronic balancers that are more accurate than the manual versions.
If a blade is just a hair out of balance, this can sometimes be repaired by enlarging one of the stress relief holes or by adjusting the alignment and even the size of some of the teeth. If the blade has suffered severe heat and the plate is sprung or warped, it may be time to invest in a new one. A good sharpener can give sound advice here. If the sharpener doesn't seem to understand the issue, it may be time to shop elsewhere.
In larger saw blade sharpening shops, most of the equipment is CNC-controlled. This means the blade is mounted in the machine, certain parameters are programmed (the number and type of teeth, the set and the diameter of the blade), and then the operator has little to do with the actual sharpening process beyond monitoring it. Small shops rarely enjoy this luxury because of the size of the initial investment. For example, a TF5 (Top or Face Sharpener) from Talon is a $40,000 machine. At $15 to $25 to sharpen an average blade, it takes a couple thousand blades just to pay for the machine.
The big advantage to CNC is that each tooth is machined to exactly the same tolerance. Many computerized shops also log your blade, so when it returns for another sharpening, the CNC program remembers the exact angle it used the last time this specific blade went through the process or it has a program for factory specs on that specific model.
Small shops with manual setups often rely on visually setting the sharpening jig to an angle that looks close to the existing one. The problem here is accumulated error. Being human, the sharpener may have a tendency to change the angle each time, and pretty soon the blade has a new, non-factory set. Some manufacturers such as Forrest ask that you return their blades to them for sharpening. This allows the sharpener to dress each tooth at an original factory setting, re-creating the original setup each time the blade is processed.
Tooth configurations
There are numerous tooth configurations and a sharpening shop needs to be able to address each of them separately. Simple flat top teeth (used to rip) require nothing more a single setup. These blades have low side clearance and tend to accumulate buildup fairly quickly. They also lack subtlety: their impact-based design tends to cause tear-out, so keeping them clean is as much a priority as keeping them sharp.
On alternate top bevel (ATB) blades, the top of every other tooth is sloped either to the right or left. The ATB configuration is generally found on rip/crosscut combination blades for the table saw and on miter saw blades with a high tooth count. The biggest problem with these blades is that the tops of the teeth are pointed and this Achilles' heel tends to dull a lot quicker than the sides of the teeth. They are tricky to sharpen manually, because it's hard to keep the two bevels even all the way around the blade.
Woodshops that work in melamine and plastic laminates prefer a triple chip configuration. This is a sophisticated combination of flat top and ATB grinds, and some smaller shops have a difficult time maintaining all the angles, especially in the absence of CNC controls.
How much?
Going rates for saw sharpening depend on the number of teeth and the configuration. Top-rated shops may vary a little in their prices according to location, too. For example, in Buffalo, N.Y., the Dynamic Saw company charges $13.50 for a blade with 61 to 80 teeth (about 20 cents a tooth), while Burns Power Tools in Fall River, Mass., charges $19.25 for the same blade in ATB (27 cents), and $22.25 (32 cents) in a triple chip. Ridge Carbide Tool Corp. in Lyndhurst, N.J., charges $17 (24 cents) for the same blade.
If carbide tips on a standard blade are damaged (and something as benign as a small knot or a sharp tap on a table saw top can cause this), most shops have the capacity to replace them. The cost is generally in the neighborhood of $2 to $4 a tip. Some shops offer complete tooth replacement on standard sizes and profiles and this generally runs between $1 and $1.25 per tip plus the cost of sharpening the blade. On a 40-tooth rip blade, this generally works out at about half the cost of a new, top-market blade. If your sharpener doesn't offer tooth replacement, ask whether they know somebody who does. Not offering this service doesn't mean the sharpener doesn't know how to sharpen: it just means they're not set up to braze.
Dado heads are usually priced at standard rates for the two outside blades, and chipper inserts run about $2.50 apiece for two-tip versions and $3.50 for four tips. Some shops can't sharpen dado sets because their equipment is set up for 10" blades and many chipper inserts have a smaller diameter than that.
John English is a freelance writer and runs the Black Hills School of Woodworking in Belle Fourche, S.D.
This article originally appeared in the February 2010 issue.
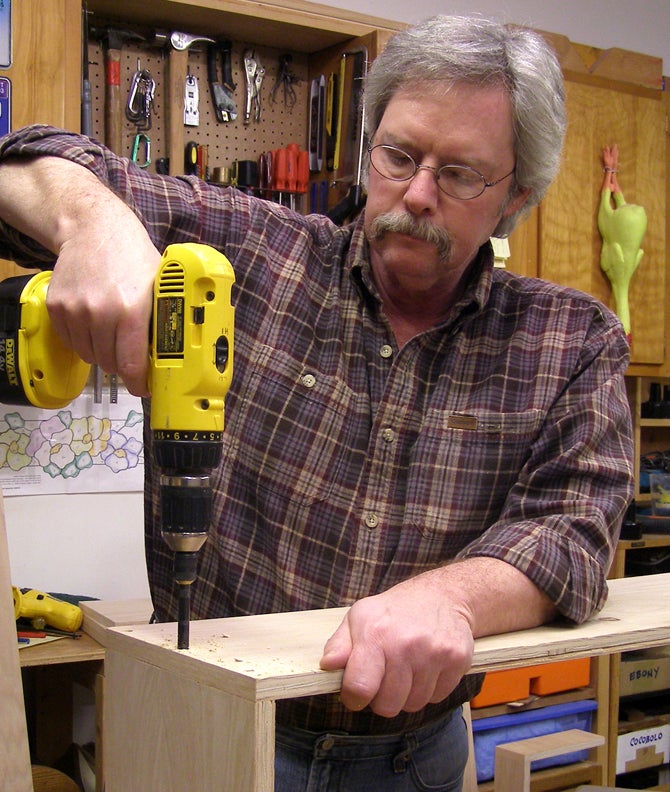
A.J. Hamler is the former editor of Woodshop News and Woodcraft Magazine. He's currently a freelance woodworking writer/editor, which is another way of stating self-employed. When he's not writing or in the shop, he enjoys science fiction, gourmet cooking and Civil War reenacting, but not at the same time.