What if
When it comes to woodshop accidents, you don’t want close calls. However, a close call is always better than the real thing.
When it comes to woodshop accidents, you don’t want close calls. However, a close call is always better than the real thing.
When making cabinets with inset backs, I’ll either mill rabbets in the parts before assembly, or rout out the rabbets afterward. It all depends on which method is most efficient for the project at hand. In this case, it was a pair of small cabinets for drill bits and cutters, and I preferred to rout the rabbets.
I installed a rabbeting bit in my table and set it up for a 1/4" cut all around the inside edge of the first cabinet. The routing went fine, but when I came back around to the starting point the rabbet depth at the end didn’t match the beginning.
I shut everything down and checked my setup, and sure enough the bit had slipped during the cut by nearly 3/16". Yikes. What if I hadn’t noticed, or if it had slipped more quickly, or if any one of a dozen other what ifs had happened? That bit could have launched into low earth orbit, possibly with some important part of me in its trajectory.
That didn’t happen. A thorough examination showed everything nice and tight, and I couldn’t figure out why the bit slipped. However, I immediately did full maintenance and cleaning on everything – the router, the collet, the shanks of every bit I own, everything.
The problem hasn’t occurred again, so I can only guess that something got in the collet that prevented the bit seating or tightening properly. But the takeaway here is that the worst didn’t happen but remained a close call and not the real thing.
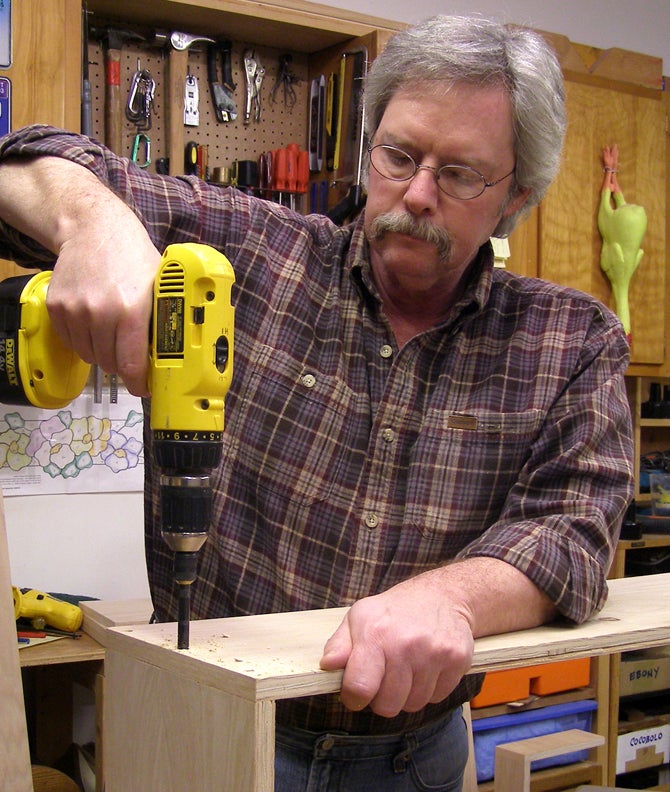
A.J. Hamler is the former editor of Woodshop News and Woodcraft Magazine. He's currently a freelance woodworking writer/editor, which is another way of stating self-employed. When he's not writing or in the shop, he enjoys science fiction, gourmet cooking and Civil War reenacting, but not at the same time.