Turning a cheap tool into a decent one
Well, I bought my scroll saw. It’s a cheapie, but with an hour’s worth of work I made it into a better tool than it was out of the box….
Well, I bought my scroll saw. It's a cheapie, but with an hour's worth of work I made it into a better tool than it was out of the box.
I just don't need a scroll saw that often so my needs are simple. I might use it twice in one week for essential tasks, but then not touch it again for months. So, two factors were key: low cost and storability.
Without mentioning brands, I got one for about $120. Five well-known manufacturers have saws in that range. I did hands-on with three of them and they're identical - same housings, same specs, same quality of fit-and-finish, everything in exactly the same locations. I'm guessing they all came out of the same factory, just with different paint jobs and decals.
The fit-and-finish was, uh, how to be charitable: disappointing. The table was so rough that you could have used the surface as a substitute for 60-grit sandpaper. All cast edges were very sharp in places, especially the table edge. Nothing was square. Anything even remotely adjustable had come out of adjustment during packing/shipping.
I removed the table and smoothed the surface with increasing grits on a random orbit sander; workpieces now slide easily without being marred. A sanding block took care of the sharp edges. A combination square, Allen wrench, screwdriver and 10 minutes work made everything square.
When running, the machine made a banging sound - the lower arm was hitting the metal housing on one side. I removed the housing and reshaped it to correct the problem only to find it was banging in another spot in the corner. An abrasive wheel on my Dremel solved that by just cutting the offending corner off. That same sanding block smoothed the edges of the cut.
In use, the machine vibrates a lot, which, in truth, I expected since this thing only weighs a bit over 20 lbs. A heavier machine like a DeWalt or Excalibur wouldn't do that, but I didn't have $500+ in my wallet (and didn't want to try to get out and put away a 50+ pound tool every time I needed it). So I just cut a piece of 3/4" Baltic birch ply and bolted the saw to it as an auxiliary base. That reduced the vibration considerably, and added an easier means of handling the saw as a bonus.
In short, my tweakification of this cheap saw has turned it into exactly what I wanted: a low-cost, easy-to-store machine for my occasional scroll-sawing tasks.
The only way I'd be happier is if it had been free.
Till next time,
A.J.
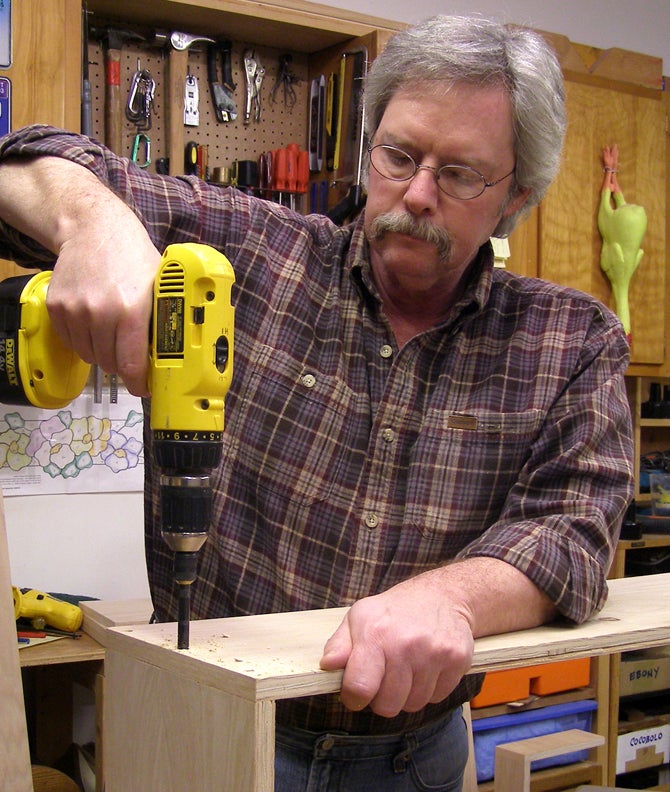
A.J. Hamler is the former editor of Woodshop News and Woodcraft Magazine. He's currently a freelance woodworking writer/editor, which is another way of stating self-employed. When he's not writing or in the shop, he enjoys science fiction, gourmet cooking and Civil War reenacting, but not at the same time.