Tolerance threshold vital for wide belt sanders
There are several factors that affect a wide belt sander’s ability to hold a close thickness tolerance. When a sander is new, with proper operating procedures, any rigid orifice-type machine…
There are several factors that affect a wide belt sander’s ability to hold a close thickness tolerance. When a sander is new, with proper operating procedures, any rigid orifice-type machine should reasonably hold plus or minus .005” tolerance. If a machine has been specifically designed and has the right characteristics to hold a close tolerance, thickness tolerances of plus or minus .0025” are achievable. However, within a short period of time (less than one year), certain wear factors require machine maintenance procedures along with proper operating procedures in order to continue to obtain tight thickness tolerances.
Individual sanding heads must be adjusted parallel to the conveyor belt and, for best sanding result, to each other. The degree of this parallelism should be within a total of .001”. This can be achieved and maintained with a setup device.
Care must also be taken to make sure that the outboard spacer and its contact surfaces are free of dust. The hold-down bolt must also be tightened with a uniform tightening force. A torque wrench might be required to accomplish this.
Conveyor belt factors
Many conveyor belt factors can have a dramatic effect on a sander’s ability to hold tolerance. First of all, all conveyor belts must be callipered (dressed to a uniform thickness). New belts must be callipered and then redressed approximately every six months to eliminate wear variances.
The conveyor belt hardness can have a major impact on a sander’s capability to hold tolerance. For maximum tolerance holding capability, belt hardness should be 85 to 90 durometer or more. The top surface pattern of the conveyor belt also impacts tolerance capability. A smooth face belt results in an optimum tolerance holding capability. Be advised that belt hardness and top surface type can impact part-feeding capabilities. Smooth face hard belts have less feeding grip than softer, rough-textured belts.
Contact drums are one of the most critical components in a wide belt sander. For optimum dimensional control, contact drums should be steel or hard rubber. Because they wear unevenly, they must be periodically ground true. Also, for optimum dimensioning capability, they should be running at belt speeds of 5,000 to 7,000 surface feet per minute. Runout should be less than .0005” (measured when drum is running in its bearings). Balance should be as fine as possible (within 2 grams). Displacement should not exceed .0002” to .0004” at operating rpm. Wall thickness should be sufficiently heavy so the drum will not deflect when heavy cut is made.
Thickness adjusting
All wide belt sanders have inherent backlash (slop) in their thickness setting devices. Thickness setting changes are accomplished through the use of jack screws rotated either by means of a worm and worm gear device or a chain and sprocket arrangement. Therefore it is essential that thickness changes are always made with the final adjusting movement in the same direction. If this is not done, side-to-side thicknesses can change by as much as .015” to .020”.
On most top sanding machines, the conveyor bed is moved up and down relative to the sanding heads to adjust thickness settings. In those cases, the final setting should always be made by moving the bed upwards to the exact setting. If the bed is moved upward beyond the final set point, it should be lowered by at least one full handwheel turn and then slowly raised, taking care not to go past the required setting.
Almost all bottom sanding machines are built so that the conveyor feed system hangs from the adjusting jack screw arrangements. This means that the final movement of the adjustment should be in a downward direction. If the set point is missed, the conveyor feed system should be raised up by at least one full handwheel turn and then slowly lowered, taking care not to go past the required setting.
On some sanding machines, the entire upper frame assembly is moved up or down instead of just the feed bed. In those cases, the final movement of the adjustment should be in a downward direction. If the set point is missed, the entire top frame should be raised up by at least one full handwheel turn and then slowly lowered, taking care not to go past the required setting.
Not all wide belt sanders are designed for optimum dimensional thickness control. In fact, some machines are purposely designed and built with yielding orifices for optimum results when sanding sealer or thin face veneers. If close thickness control is one of your requirements, make sure that you purchase a machine with the proper characteristics to optimize those requirements. If you find that your machine has thickness-control design deficiencies, it might be possible to modify in the field and gain some improvement.
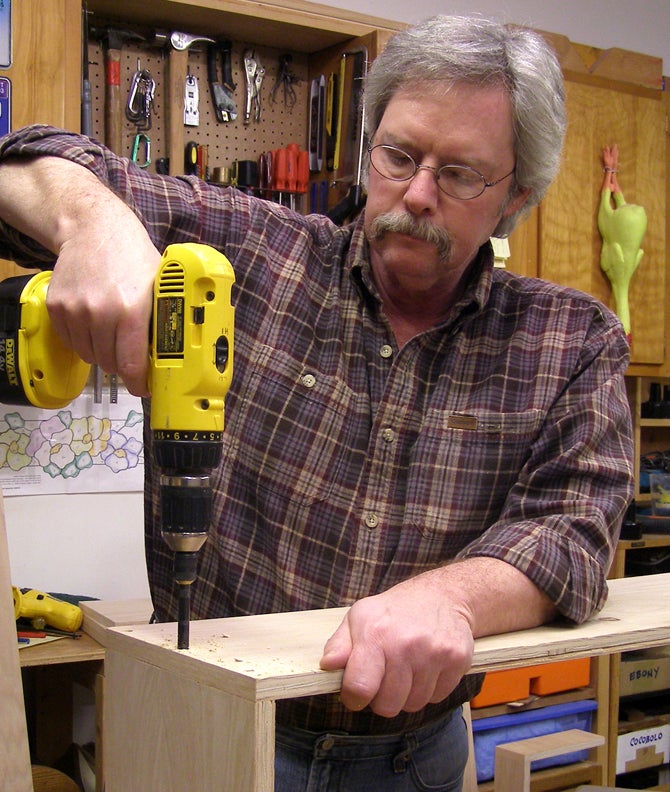
A.J. Hamler is the former editor of Woodshop News and Woodcraft Magazine. He's currently a freelance woodworking writer/editor, which is another way of stating self-employed. When he's not writing or in the shop, he enjoys science fiction, gourmet cooking and Civil War reenacting, but not at the same time.