Time for the nitty-gritty of grit sequence
My first two articles provided depth of scratch and material removal information. Based on the depth of scratch, material removal data and the machine that you have, you can now…
My first two articles provided depth of scratch and material removal information. Based on the depth of scratch, material removal data and the machine that you have, you can now determine what grit sequence should be used.
Selecting the grit
The purpose of the roughing grit is to remove stock and bring the part to a uniform dimension, leaving enough material to develop the final finish.
The purpose of each subsequent grit is to remove scratches from the previous grit.
There should be no more than a two-grit jump between the roughing and the next grit size (36-50 or 40-60). Depending on feed speeds, there should be no more than a one-grit jump between fine grit belts (80-100-120-150-180-220 etc.).
With that being said, can you remove a sufficient amount of the coarser scratches with your final finishing belt at the feed speed you are running? Develop a matrix and experiment on paper with different grit sequences considering:
• The machine configuration
• The total material removal required
• The final finish required
• Do you have to remove all coarse grit scratches?
• What is maximum removal capability for each belt based on material and feed speed desired
For example
The following analysis is for a typical three-head finishing sander at a feed rate of 20 fpm:
This simple analysis shows that on all wood species, the total target removal fell within the belt removal parameters.
However, on hickory, hard rock maple, white oak, ash, birch, soft maple and red oak, the target removal on the 220-grit belt exceeded its removal capability. On all species, the combination of the 180- and 220-grit belts did not have the capability to remove the 120-grit scratches.
Therefore, the options are:
1) Slow the feed speed down to 10 fpm. This would double the cutting capability of all sanding heads and result in head Nos. 2 and 3 to have the capability of removing of the 120-grit scratches.
2) If possible, change the first head to 150 grit, which would result in a scratch depth of .006”.
3) Reduce the feed speed to 10 fpm and change the grit sequence to 150/180/220. In some cases, the 220-grit belt will still not have the cutting capability to remove all of the 180-grit scratches, but this might not be necessary.
4) Keep the existing parameters and live with poor belt life and quality on the 220- and 180-grit belts and live with the inability to remove all of the 120-grit scratches.
For help with sanding problems, contact: Howard Grivna, Sanding Systems Consulting Inc. Tel: 218-678-2929. www.sandingsystemsinc.com
This article originally appeared in the July 2012 issue.
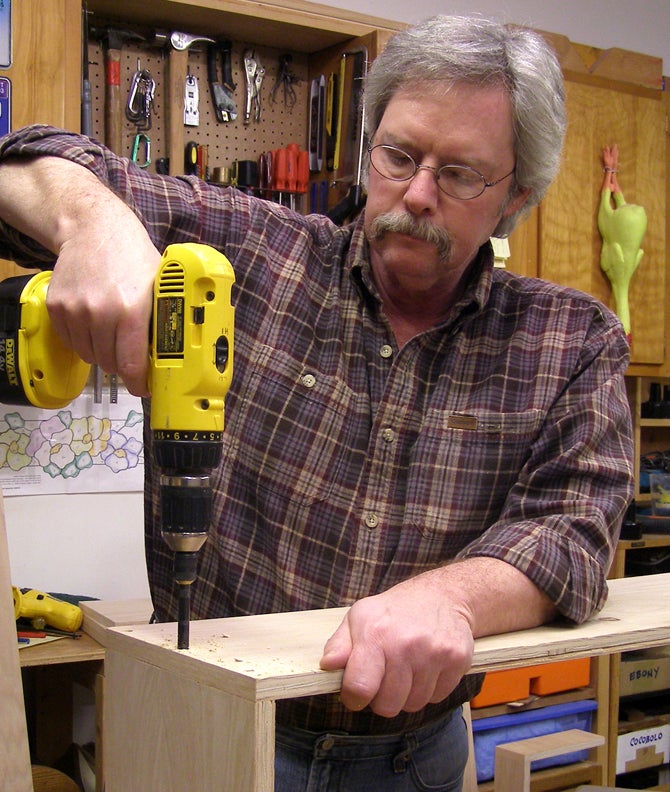
A.J. Hamler is the former editor of Woodshop News and Woodcraft Magazine. He's currently a freelance woodworking writer/editor, which is another way of stating self-employed. When he's not writing or in the shop, he enjoys science fiction, gourmet cooking and Civil War reenacting, but not at the same time.