The sound in a cut never lies
A good ear can help with a CNC router’s performance, but only after careful consideration is given to tooling selection, and feed and speed rates Here’s the tricky bit about…
A good ear can help with a CNC router’s performance, but only after careful consideration is given to tooling selection, and feed and speed rates
Here’s the tricky bit about choosing bits for use in a three-axis CNC router: there’s a lot to consider. You’re probably going to start with the material that needs to be cut, but you’ve also got to factor in the router’s spindle type and horsepower, the construction quality of the machine’s base and gantry, type of work-holding system and much more.
Then again, it might be more helpful to start with the basics, such as the differences and applications of straight-plunge, spiral and compressions bits.
These bits cost more than general woodworking bits because they are subject to longer periods of use and required to cut at a faster rate. The amount of heat a bit has to tolerate and the amount of force the bit is subjected to are both are much greater and for longer periods of time.
Though there is much debate about how router bits are used on a CNC router, there is one aspect that is always true: The more expensive, industrial-quality bits are a bargain. These bits will have better engineering, materials and design, and incorporate features such as high-quality carbide; increased clearance geometry, polished flutes and razor-sharp cutting edges.
Straight-plunge, spiral and compressions bits are manufactured in different configurations so they can effectively and efficiently cut materials like MDF, plywood, melamine and solid wood.
Straight-plunge bits often have one, two or three carbide-tipped flutes that are parallel to the rotation of the bit’s shaft. They tend to be used to cut at high-speeds in materials such as chipboard and MDF.
Spiral bits come in down-spiral and up-spiral configurations with any number of flutes. Down-spiral bits, as the name suggests, cut down into the material. This leaves a splinter-free top edge and helps keep the material tight against the work surface. However, the cutting action drives the removed material into the cut, causing additional wear and quicker dulling of the bit.
Conversely, up-spiral bits cut up from the material. This action ejects the removed material, helping to reduce wear on the bit and allowing for faster cutting speeds. But the edge of the cut will be prone to splintering and the material will be pulled off the work surface, which can cause inaccurate cuts.
Compression bits are a combination of down- and up-spiral bits. The cutting flutes spiral up from the bottom and down from the top. This drives the removed material to the middle of the cutter. These bits are used to cut completely through sheets of plywood, laminates and composites in one pass, leaving clean cuts on the top and bottom edges.
Feeds, speeds and chip loads
Like all other aspects of digital fabrication, there is more to know about a tool than just its physical characteristics. This involves knowledge of the machine’s characteristics and capabilities and a working knowledge of two machining concepts.
The first is the relationship between feed rate and speed. Feed rate refers to how fast the tooling will move through the material being cut or machined, which is measured in inches per minutes. Speed refers to the rotational speed of the spindle and is measured in revolutions per minute.
The second is chip load, a measurement of the thickness in inches of material removed by each cutting edge of the tooling during a cut.
To calculate the chip load, multiple the feed rate by the RPM.
But if you were to put four CNC operators in a room, they’d have at least a dozen opinions on the appropriate feed, speed and chip-load best-case scenarios and they will all be more or less correct. Feeds, speeds and chip loads are determined to maximize the rate of material removal rate, produce the best possible edge cuts and maximize tool life. Sometimes, you can only achieve two out of the three.
For example, if the goal is to maximize material removal and surface finish, then a moderate-to-high feed rate and a high spindle speed will probably get the job done. However, this combination will tend to cause the tooling to run at a high temperature and shorten its life.
But if you’re cutting mostly sheet goods, where most of the cuts will be hidden in dados or rabbits, by edgebanding and sanding, a moderate feed rate and slow spindle speed might suffice, resulting in longer tool life.
So who’s right?
The question that often arises is what feeds and speeds are moderate and what are high? The answer is ambiguous. Generally, many tooling manufacturers suggest spindle speeds of between 10,000 to 20,000 RPM, but that depends on the feed rate, the characteristics and capabilities of the CNC router and the material being cut, among others.
This leads, more often than not, to making educated guesses on the proper feed and speed rates while using the trial-and error approach. Some of this can be avoided by contacting your tooling supplier for suggestions. Ask if you can be referred to another shop for answers and offer to pay for their knowledge and time. Online forums are another excellent option.
When all else fails, lend an ear to the situation. The sound of a tool in the cut can be quite informative. A quiet cut suggests you’ve probably got everything dialed in correctly, while squealing or growling suggests something is running either too fast or too slow.
This article originally appeared in the February 2015 issue.
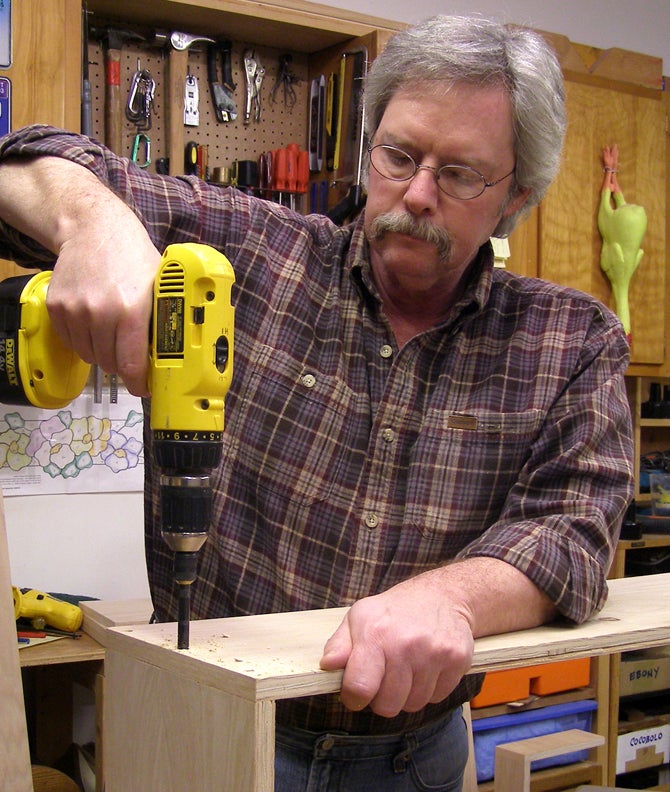
A.J. Hamler is the former editor of Woodshop News and Woodcraft Magazine. He's currently a freelance woodworking writer/editor, which is another way of stating self-employed. When he's not writing or in the shop, he enjoys science fiction, gourmet cooking and Civil War reenacting, but not at the same time.