Smooth over your sanding shortcomings
During the last decade, I have analyzed the sanding systems of more than 400 different companies that involved more than 1,000 wide belt sanders. I soon became aware of a…
During the last decade, I have analyzed the sanding systems of more than 400 different companies that involved more than 1,000 wide belt sanders. I soon became aware of a distinct pattern of operating problems irrespective of the product being manufactured or the size of the company. The following are universal problems that you should endeavor to avoid.
Improper adjustments
The depth of cut of each sanding head is almost never properly set. On multiple head machines, the negative effect of this problem is substantial. Oftentimes, on machines with three or more sanding heads, the center sanding heads are not even touching.
The side-to-side adjustment of each sanding head is also almost never properly set. On multiple head sanders, these sanding heads are usually tilted in opposite directions, resulting in completely different sanding results depending on which side of the machine a panel is sanded on.
Pinch rolls and hold-down shoes on machines older than six months are usually badly out of adjustment relatively to each other, relative to the sanding heads and side to side. The negative effect of these problems usually results in dubbing or sniping.
Feeding too fast
The feed rate often exceeds the cutting capability of the belts. This creates premature belt loading, burning and streaking, and is a major contributor to inconsistent finish problems.
Always down the middle
Operators often feed down the center of the machine, rather than using its entire width. This creates uneven wear on components such as abrasive belts, sanding heads, conveyor belts, pinch rolls, and hold-down shoes. It also produces uneven sanding and finishing problems.
Worn components
After any machine has been in use for a period of six months or more, it is likely that many of its components become worn because of the conditions mentioned above.
Conveyor belts are almost always worn down the center, affecting thickness control and resulting in uneven sanding depending on where a panel is placed across the width of the machine. Contact drums wear so that they are out of balance or out of round, resulting in chatter marks. Conveyor bed plates wear concave because of an uneven feeding of panels resulting in uneven sanding across the width of the machine.
Other common problems
In almost every plant visited, sanding heads on wide belt sanders were found to be improperly set relative to each other and also often not parallel to the conveyor belt. Furthermore, belt sequences were often changed without making any individual drum or platen adjustments and no individual adjustments were made to correct for belt wear. These problems result in abrasive belts loading, burning, streaking, shortened belt life and poor finish quality.
In order to eliminate all of the above problems, a user must have the following information:
• What is the depth of cut resulting from each grit abrasive belt being used?
• What is the maximum amount of material that can be removed at the feed speed required?
• Based on that information and the machine that I have, what grit sequence should be used?
• What am I currently removing with each abrasive head?
• How can I adjust my machine to get to where I should be?
• How can I monitor belt thickness variations due to different type backings, mineral types, mineral grades, different brands or wear and make necessary sanding head adjustments to compensate?
During the next several issues, I will address specific remedies for each of these major universal problems. But it all starts with the average stock removal (depth of cut or scratch) for each grit size, referenced in the chart below.
Keep this information for future reference. Deep scratches put in by coarse grit belts must be uniformly and consistently removed by finer grits in order to obtain uniform and consistent colored finishes.
For help with sanding problems, contact: Howard Grivna, Sanding Systems Consulting Inc. Tel: 218-678-2929. www.sandingsystemsinc.com
This article originally appeared in the May 2012 issue.
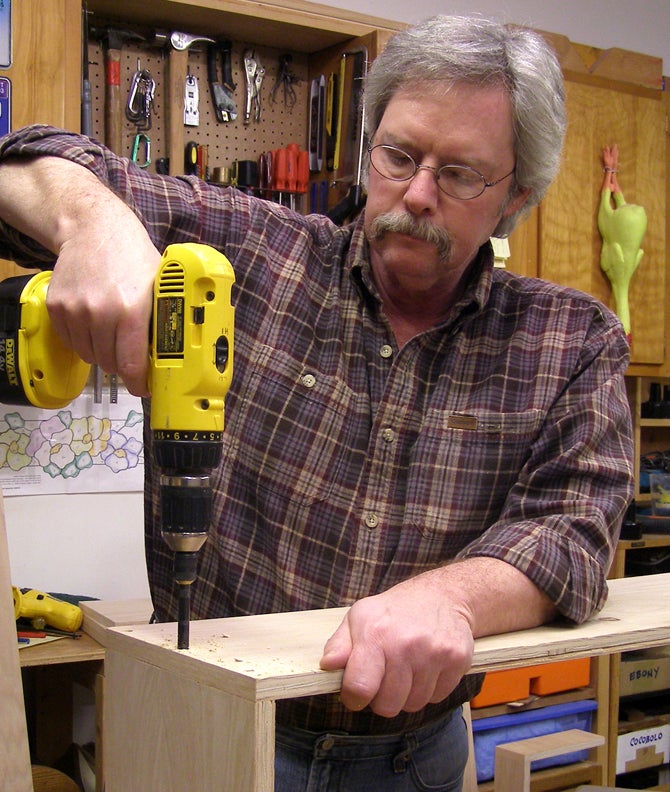
A.J. Hamler is the former editor of Woodshop News and Woodcraft Magazine. He's currently a freelance woodworking writer/editor, which is another way of stating self-employed. When he's not writing or in the shop, he enjoys science fiction, gourmet cooking and Civil War reenacting, but not at the same time.