It’s tough living on the cusp.
How does one decide whether a business is mature enough to justify moving into robotics? This is a big commitment that goes far beyond just adding a new machine. The decision depends on so many factors, several of which are external while others ride on internal values such as cashflow, personnel and local infrastructure.
The external ones are completely beyond our control, so we can only react or plan for them. For example, on June 19, the Federal Reserve surprised many analysts by declining to raise interest rates, while signaling that it may even consider a cut soon because of a slowing U.S. economy. Does that make a stronger or weaker case for investing right now in a robot? If housing starts sag, or interest rates fall or inflation kicks in, do any of those factors make this a better or worse time to borrow and buy?
Another cusp-related reality is that this isn’t just a numbers decision, because not everything fits neatly on a spreadsheet. For example, people. If a shop has the right personnel in place already who are tech savvy, knowledgeable and innovative, that can change the equation. Hiring and training are huge drains on a shop’s cashflow and productivity, especially if the entire crew has to learn how to best use and incorporate brand-new technology.
The shop’s existing infrastructure is an essential ingredient, too. Adding a robot in reality means adding a complete robotic cell, and the shop needs to consider physical space, power, dust collection, infeed and outfeed accommodations, and a host of other aspects beyond just the price tag on the machine.
Along with all those questions, a woodshop manager also needs to realistically evaluate the upside. And that can be, well, huge. SCM Group (scmgroup.com), based in Michigan, recognizes that dichotomy. The company has spent a great deal of time and effort over the last year or so creating the Smart & Human Factory. What it is, in essence, is an event that marries state-of-the-art digital and automation systems with collaborative robots. It lets woodshop owners and managers witness, in real-time, a new model of interaction between humans, robots and machines. This occurs in open, safe cells where four different types of cabinets are produced. One of the facets that SCM highlights is that operators are freed from repetitive and low added-value activities, which goes right back to that question of having the correct personnel in-house. When robotic arms initially became a realistic option, bean counters everywhere immediately thought that robots might simply replace hired labor and benefit the bottom line. And indeed, they can certainly do that. But rather than restricting their impact to the shop’s existing parameters, the challenge here is to see how this new technology can change some fundamentals.
Fluidity, for example, is one facet of robotics that sets them apart. Most woodworking machines are stationary, and we feed raw materials to them. A basic example is the act of sliding sheet goods through a table saw. Some of our more advanced machines incorporate materials handling, which means they can feed themselves. For example, we might drop a pile of MDF on the infeed side of a CNC router. But from there, the machine can only slide the material in place, lock it down and then machine along dedicated axes.
Robots are different. They are fluid, flexible and almost human in their span of movement. They can twist and turn at high speed, align and reset material, perform intelligent assessments and corrections, and interpret reports. They are not yet fully intelligent, but that’s now just a matter of degree. Within the confines of set tasks, they can be made aware of almost all eventualities and responses. That is, we can teach them enough to allow them to choose among options and make the most logical choices.
So, how can that agility be incorporated into existing processes, or generate new ones? Most shops begin with the realization that a robot could do a single task, but it doesn’t take long to begin to see myriad opportunities. For example, Fanuc America Corp. (fanucamerica.com) in Rochester Hills, Mich. supplies robotics to woodshops for a wide range of tasks. Its machines are used for assembly, dispensing and sealing, machine tending, material removal, painting, coating and parts transferring.
Robots in production
Cabinet shops have seen an evolution over the past few years, where more and more custom shops are using outsourced suppliers to make components, and often entire kitchens. As robots become more advanced and more affordable, medium-sized shops in particular are going to be presented with a new choice. Robots will begin to open the door to bringing much of that production back in-house. Working three shifts a day if needs be, they can currently maximize the output from other machines, in particular CNC milling.
But robots are also beginning to take over a large part of the assembly and finishing processes, too. And because they are so versatile, furniture makers are rapidly discovering that they work extremely well at producing small batch, complex assemblies that heretofore were the exclusive province of highly skilled people. Take away the concept of working within the confines of three, four or five CNC axes, and you can build almost anything. While large shops often have a hard time responding to change (that is, their processes often don’t lend themselves as easily to one-off or short production runs), and small shops simply can’t afford the equipment, robots can be the perfect solution for medium-sized shops.
There’s another take on skilled labor, too. One highly trained operator who is teamed with a handful of robots can do the work of a whole team of other highly trained employees who are using conventional milling and assembly solutions. In today’s job market, where skilled labor is becoming increasingly difficult to find, this concept may well be a light at the end of the tunnel. Is the new solution going to be one human, several robots and state-of-the-art materials handling and routing?
At the Ligna show in Hanover, Germany this May, Biesse explored that solution. The company had a 65,000-sq.-ft. exhibit space dedicated to illustrating that the future of Industry 4.0 is now. The theme was “a winning alliance between man and robot”. There were three automated processing solutions on display, the first of which could produce up to 1,500 panels per shift and deliver a complete kitchen conceived by Cubo Design. Next was a collaboration with Italian designer Lago, which concentrated on furniture – more specifically, living and sleeping projects that combined “ideas in flexibility with regards to sectioning and robot-assisted machines”. And the third demonstration, a collaboration with BMT Bagni, was for bath furniture and shop fittings. This latter focused on integrating machines with additional automatic systems, robots and software. That fitted well into one of Biesse’s goals at Ligna, which was to show smaller (as in mid-sized rather than large scale) woodshops how they can be transformed into smart factories. To that end, the company presented its ROS (Robotically Operated System) integrated robots for handling panels and providing support for sectioning, boring, smoothing and CNC machines.
CMA Spray Robotics (cmarobot.it) has been in business for 26 years and is a world leader in the field of automatic spray equipment, imported by Robotic Solutions (machinesolutionsllc.com). The Italian manufacturer designs and installs a wide range of robotic equipment, and supplies software for self-learning, point-to-point, offline and auto-generation. CMA also manufacturers full turn-key spray systems for the wood industry. Robotic Solutions was formed in 2017 as a system partner for Kuka Robotics in Germany, and offers stationary, autonomous mobile, and collaborative robots. Applications include machine tending, palletizing, part-flipping, sanding, transporting parts, and assembly.
Collaborators
There’s an interesting two-minute video from Rethink Robotics (youtu.be/o3cb3iCmQz8) about how a Massachusetts furniture manufacturer, Moduform, has incorporated a single robotic arm called Sawyer into its parts processing. The company builds casework for institutions (colleges, hospitals and the like), and it has seasonal labor requirements that couldn’t be easily filled. So, it deployed a collaborative robot to pick up the slack. A mid-sized woodshop contemplating such a solution will appreciate some of the insights offered by CEO Josh Weissman.
That term ‘collaborative’ is interesting. Also known as cobots, or co-robots, it refers to robots that physically work with and alongside human workers in a cell, and do so safely. Up until a few years ago, most industrial robots were autonomous. That is, they were isolated from people and given set repetitive tasks. This new generation of cobots is distinguished by characteristics such as small size, smaller investment levels, extreme dexterity, and safe housings. They can be taught by demos instead of having endless lines of code written. That makes them easier and less expensive to integrate into the production line.
This article originally appeared in the August 2019 issue.
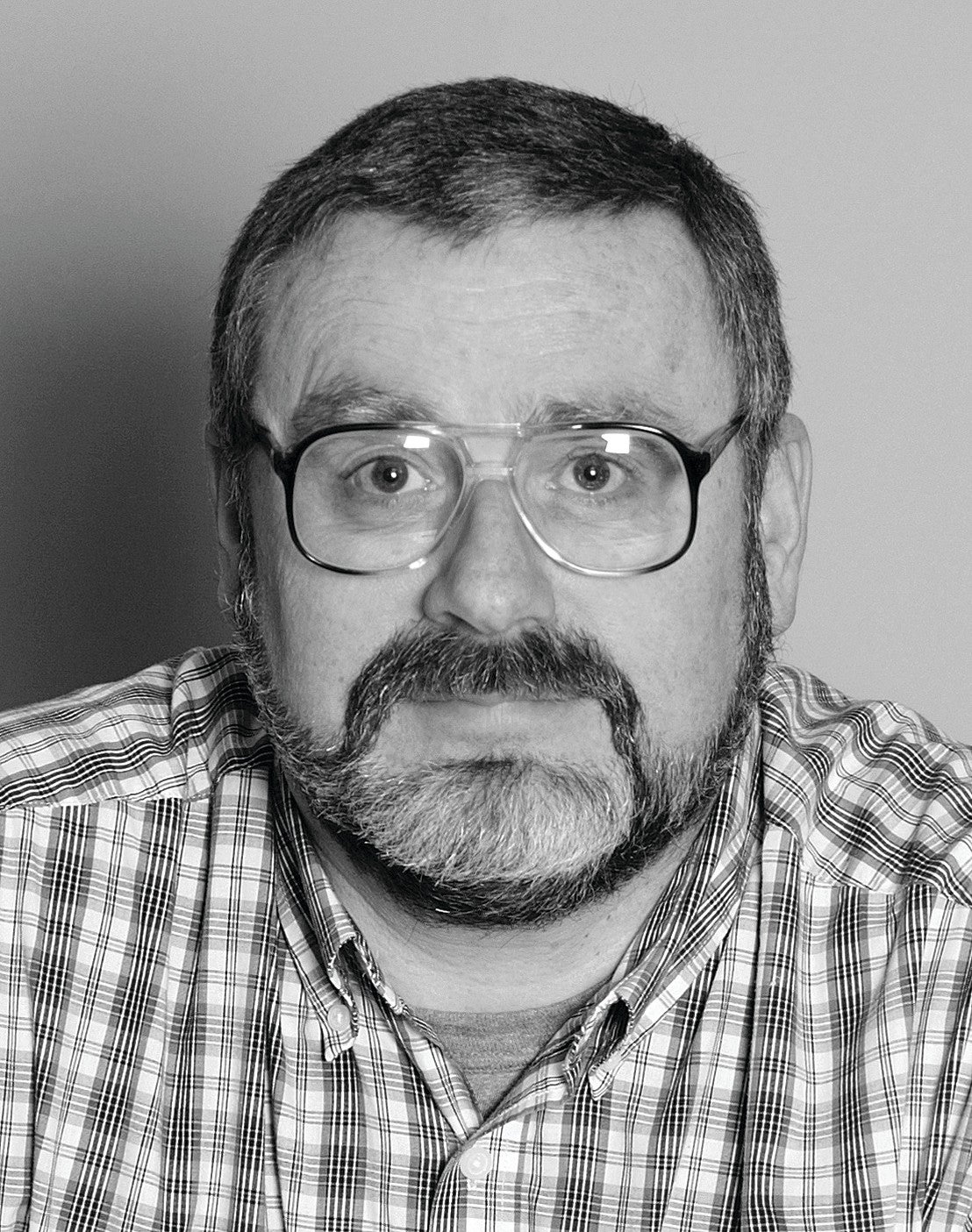