Power point: How to harness 3-phase motors
Sooner or later, most small-shop owners will find a great bargain on a machine only to discover that it has a 3-phase motor. Since 3-phase power is typically found in…
Sooner or later, most small-shop owners will find a great bargain on a machine only to discover that it has a 3-phase motor. Since 3-phase power is typically found in industrial settings, many of these shops will only have a single-phase electrical service coming into their buildings. While sometimes the simplest solution is to just replace the motor, that is not always a reasonable option. In this article, I will discuss other ways to bring 3-phase machines online.
The place we need to begin this discussion is at the entry point of electricity into your building. Your primary electrical panel is directly tied to a transformer on a utility pole or underground wiring pad nearby. While it is the type of power running down the street that determines your ability to have a 3-phase service, it is the transformer that determines the voltage coming into your building. This will vary depending upon your location, but I will refer to single-phase power as being 220 volts and 3-phase power as being 208 volts here. While this article will deal with machine motors of these voltages, understand that higher industrial voltage machines do exist and can sometimes be run per this information.
The difference between the motors
A single-phase motor is designed to run on 110 or 220 volts. It is powered by two wires: two hot lines, if 220-volt; or a hot and a neutral, if 110-volt. The motor may or may not have a capacitor to help it start under load and another to beef it up a bit when running. If it does have a capacitor(s), it will also have a centrifugal switch incorporated to pass the capacitor power to the motor windings.
A 3-phase motor is a simpler device. It does not use capacitors and switches, but instead relies upon the windings to give it starting and running torque. Partly because of this, 3-phase motors typically cost less to purchase than single-phase motors. Also 3-phase motors split the 208-volt power source between three leads instead of two, which means the wires going to the machine can be a smaller gauge. However, contrary to popular thinking, 3-phase motors do not cost less to run because total current drawn through the electric meter will be the same whether it is split between two or three wires.
3-phase converters
Now that the differences between the motors have been reviewed, we can go over the options available to run a 3-phase machine in a single-phase environment. There are four possibilities: static, rotary and digital converters, and frequency drives (inverters).
Static converters
A static converter is an electronic device that will pass single-phase, 220-volt power through to two of the three legs of a 3-phase motor. It will then electronically generate power to the third leg just long enough to get the motor up and running. Once the motor has started, the generated third leg will cut out, leaving the motor to run on single-phase power.
The upside to static converters is that they are relatively inexpensive to purchase while being small and easy to mount by the machine. The downsides are significant, though. First, static converters are sized to either a specific or low range of motor horsepower ratings. While you could theoretically set up to run two motors off one static converter, it could only run one at a time.
The second downside is that after the electronically created third leg cuts out, the motor is running on the two single-phase wires. Because of this it will only be running at about two-thirds of its rated horsepower. This might be alright if you are running a light load, but it could burn out the motor and/or static converter if a heavy load is applied.
Rotary converters
At the core of a rotary converter is a spinning 3-phase electric motor accompanied by capacitors and other electronic components. Since the converter’s 3-phase motor is freewheeling, it does not require significant running torque and the capacitors in the circuitry will help get it going. As such, it can spin using 220-volt, single-phase power to two of its three legs.
These same two single-phase leads that are powering the rotary converter’s motor are then fed directly to your machine motor, connecting to two of the three motor leads. Since the converter’s motor is spinning with no load, it acts like a generator and electrical current is pushed out of its third lead. This third lead is then connected directly to your machine motor’s third leg and you end up with “true” 3-phase power.
There is a somewhat unexpected benefit to this system. Since two of the three leads to your machine are coming from your single-phase power service, the rotary converter is only providing one-third of the required power. As long as they are started one at a time, you can simultaneously run multiple motors up to approximately triple the rotary converter’s horsepower rating. On the other hand, since motors typically have high startup power requirements, you’ll need to purchase a rotary converter that is 1.25 to 1.5 times larger than the biggest motor you will want to run. The heavier the load on the motor at startup, the more oversized the converter needs to be.
While rotary converters are a very good option for 3-phase power conversion, there are still a few downsides to consider. One is that you will be paying the electrical costs to spin the converter motor as well as the machine motor. You may also have to be careful in connecting the converter to machines with electronic components so that the generated lead goes to an input that does not feed the electronics. Finally, along these same lines, you need to make sure there is electrically balanced 3-phase power going to your machines. This requires circuitry that should be designed into a good quality rotary converter, but it is an issue that needs to be examined with your purchase.
Frequency drives
This is the correct solution for situations where your new machine has a speed-controllable motor. With the exception of some small motors (such as those used on hand-held power tools), AC motors are not easily set up for variable speed. It can be done, though, on 3-phase induction motors with a frequency drive. These are user-controllable electronic devices that mix AC and DC circuitry to provide a variable-speed 3-phase output.
They are available in two varieties: those that can input only 3-phase power and others that can input either single-phase or 3-phase. Both output 3-phase simulated power with full voltage on all three legs. Once in place, they have the economy of operation of the static converters and the true 3-phase power output of rotary converters.
Digital converters
Digital converts are similar to static converters and frequency drives since they are completely electronic in nature. They produce true 3-phase power, but are not designed for use with variable-speed motors and do not need to be sized to a specific motor. One unit can power an entire shop. But digital converters are the most expensive option — about 1.5 to 2 times that of a similarly sized rotary converter — and are currently available in a limited range of sizes. Plus, if a digital converter that is used for full shop conversion has an electronic failure, the entire shop can be down until it is repaired or replaced.
Conclusions
So what’s the best choice for your shop?
• If two-thirds of the machine’s rated horsepower will be adequate and you don’t anticipate additional 3-phase needs in the future, an inexpensive static converter is a good choice.
• If you are bringing in a piece of equipment such as a CNC router that requires variable speed or programmability, then frequency drives that input single-phase power are a better solution.
• If you are thinking along the lines of a fully 3-phase capable shop, then a digital or rotary converter is the best choice.
B.H. Davis is the owner of B.H. Davis Co. a maker of curved moldings in Thompson, Conn.
This article originally appeared in the March 2012 issue.
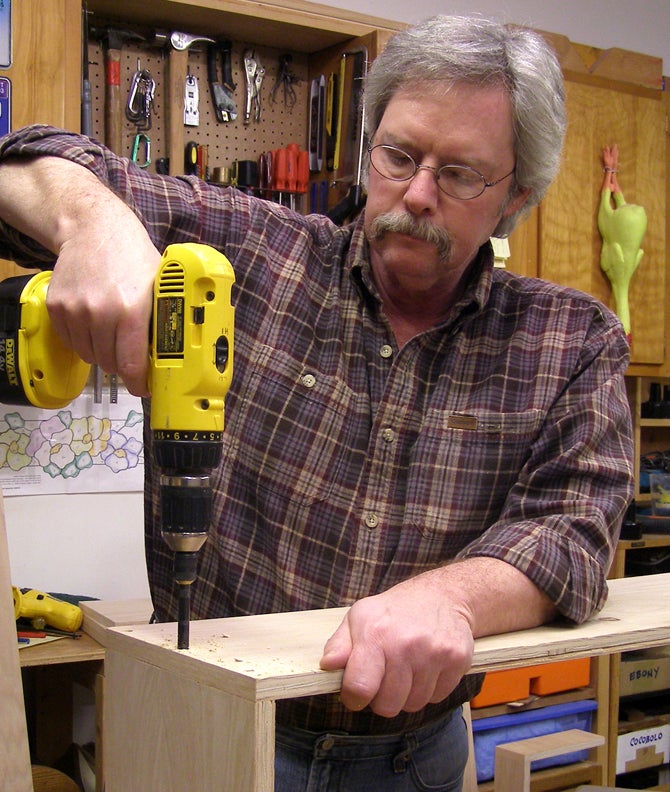
A.J. Hamler is the former editor of Woodshop News and Woodcraft Magazine. He's currently a freelance woodworking writer/editor, which is another way of stating self-employed. When he's not writing or in the shop, he enjoys science fiction, gourmet cooking and Civil War reenacting, but not at the same time.