Metrics can predict peak performance
Last month we covered the nuts and bolts of how to gather information and enter the information into a database, either a computerized maintenance management system or an enterprise asset…
Last month we covered the nuts and bolts of how to gather information and enter the information into a database, either a computerized maintenance management system or an enterprise asset management system. Regardless of which software package you choose, you are now ready to embark on the journey of using the available data to support critical decisions that will help you to maintain your machinery in a more reliable manner.
{loadposition position10}
A word of caution before proceeding: Management of a maintenance department is a business process. The database is a tool to help that process. If the management process is in any way not viable, the database tool will be less effective and may well expose management shortcomings. The data itself must be accurate in order to substantiate business decisions and any conclusions drawn.
If you are like most woodworkers, you probably concentrate on the project at hand. Did I order the correct materials in time to meet the delivery date? Do I have enough finish? Is the truck big enough to handle the size of the shipment? All of these are important questions, but not as pointed as when your machinery screeches to an abrupt halt in the middle of a critical production run and you are forced to ask, "Was this supposed to be greased?"
Using the information that resides in the database can help to avoid situations like this. It's important to remember that the frequency interval (periodicity) recommended by most manufacturers is based upon a 40-hour workweek. If you work overtime or have multiple shifts, the maintenance interval must be recomputed. Whether you mark your shop calendar or use a database, implement a maintenance interval schedule and stick to it. Good intentions will not protect your machinery. It might not show itself in a week or a month, but aggressive preventive and predictive maintenance will save you time and money in the long run.
At Techline USA, we have some equipment that is more than 15 years old. The OEM cannot believe the machinery is in such good condition after running 10 hours per day for so many years. The secret to our success is a good preventive maintenance program.
Tracking the data
Once your schedule is established and the data is accurately captured, what's next? Well, like most of us, we are held to some kind of standard or level of responsibility. The captured data can help in several types of justifications. The first that comes to mind is equipment reliability/uptime. By keeping accurate data on your maintenance routines, you have the ability to calculate mean time between failures, overall equipment effectiveness or other key performance indicators you wish to track. You can also track maintenance costs.
I prefer to track these by machine (on some of our large integrated lines, I track as many as 13 subsections for more detailed reporting). Tracking of spare part usage should also be captured by machine. This will help to determine stocking levels and turn counts. One feature I would look for in a database or software is the ability to generate a request for quotation. This will help the person ordering spare parts to know what to purchase. All this information can be rolled into cost justifications for machine replacement and future budget considerations.
All of the above is a mute point if the database won't perform in a way that enhances your ability to keep your machinery running. To analyze the data, you will need some type of reporting capability. Try to get a demo of the software you are considering. Try out the reports. Canned reports look great on demo CDs, but do they provide what you need? Try to modify or edit the reports. Some programs are easy to use, while others require advanced computer skills to manipulate the data.
The ultimate question is whether this will be something that you use or will it collect dust? If you choose wisely, gather the data entirely, accurately input the data and schedule with common sense, the answer will be the resounding noise of busy production and minimal machinery downtime.
Establishing an amp baseline
Having covered databases, it's time to move on to the practical side of the maintenance world. After the machinery has been cleaned, lubricated and calibrated, how do we know it's working and how well it's working? The best place to start, if possible, is when a machine is new and has just been installed. This is the perfect time to acquire an ammeter, also known as an amp clamp. This is a device that clamps (circles) the main power cable of a 3-phase machine and reads the amperage the machine is consuming. When establishing an amp baseline, it is advisable to make sure you write down and quantify what is running for future comparison.
Machines with multiple motors should have a reading on each individual motor for future comparison and troubleshooting. Amp clamps are an inexpensive and simple way to establish a machine baseline. For machines already in use, start a baseline. At least you can track the decline of the motor efficiency. Knowing in advance that a motor is declining will help with the maintenance scheduling and allow you to schedule downtime for repairs, lessening the impact on your production schedule.
An amp baseline is the first step leading to a statistical predictive maintenance triad. Knowing weeks or months in advance that one of your machines is going to fail might sound unbelievable, but there are tools out there that make this dream a reality. We are not talking about crystal balls here; we are talking about real technology like thermal imaging cameras and vibration analyzers.
Thermal imaging (or infrared) cameras are on the market everywhere. But the buyer should beware. These imagers can find sources of potential fires, hot spots in electrical panels, fuses that need to be replaced and faulty grounds. While this may sound easy, there is a learning curve to this process. Working from practical experience, if you hand a thermal imager to four different people, you will most assuredly get four different results. How one holds the unit, how far away the unit is held, which thermal scale was selected, and whether or not the laser pointer was used to aim or frame the capture (picture) will affect the results.
At Techline USA, we went through our share of growing pains in the learning curve. It took some time for everything to become standardized. We came up with the idea of attaching a string to the unit so the same distance of the unit from the source was constant. By building a record of captures, you can do a trend analysis and see a decay curve. By the way, the thermal imager schedule for the machines should appear on preventive maintenance work orders, which are scheduled and included in the database.
Vibration analysis
The last leg of the statistical predictive maintenance triad is vibration analysis. Just as we established a baseline for amperage and thermal images, vibration readings captured on a given schedule will give you the ability to track the decay (increased vibration) from a machine and help predict a failure and fix it before it breaks. Vibration is an oscillation caused by some type of movement. The result of vibration may be sound or heat.
The cause of vibration is usually a repetitive force, resonance or something being loose or worn. Vibrations can be caused by imbalance, misalignment, worn-out parts or improper driving. Looseness might be the result of excessive clearances, mismatched parts, improper mounting, corrosion or cracked structures. Resonance is when the machine, vibrating at its natural frequency, is in some way aided externally to assist the vibration, causing the vibration to escalate unchecked and resulting in serious damage to the equipment.
Getting a baseline on equipment as soon as possible will not only help track the machine, but this part of the triad usually saves the most money. Machine misalignments have hidden costs that you might not realize. Increased vibration in motors requires more power to turn the motor. This works hand-in-hand with the amp reading baselines and helps with troubleshooting.
Statistical predictive maintenance can also prevent unnecessary maintenance. Changing out good parts that are in proper working order is just a waste of your hard-earned money and time. Properly running machines also lend themselves to higher quality, greater yields and less rework and warranty returns. And that has an impact on your company's image and bottom line.
Patrick Molzahn is the director of the cabinetmaking and millwork program at Madison Area Technical College in Madison, Wis. John Nichols is a senior maintenance manager at Techline USA in Waunakee, Wis.
This article originally appeared in the July 2010 issue.
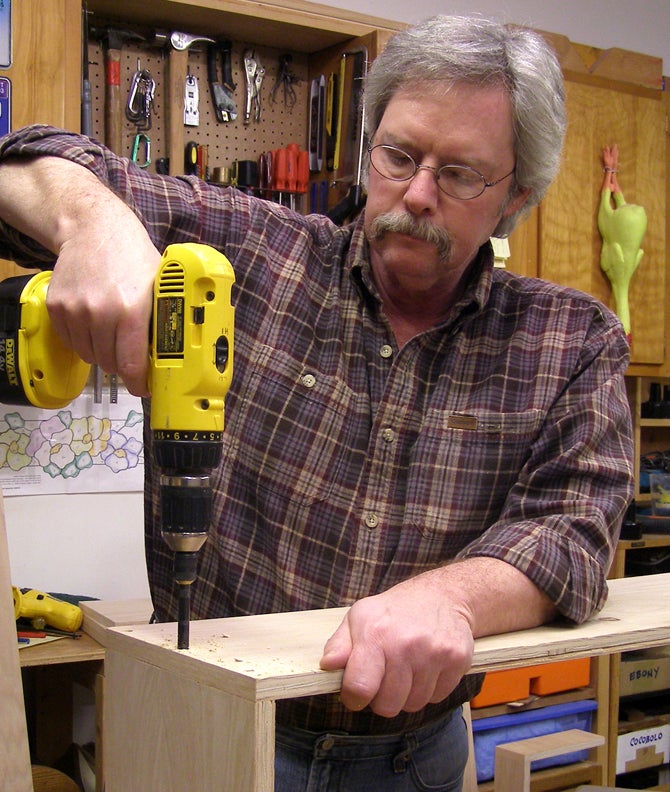
A.J. Hamler is the former editor of Woodshop News and Woodcraft Magazine. He's currently a freelance woodworking writer/editor, which is another way of stating self-employed. When he's not writing or in the shop, he enjoys science fiction, gourmet cooking and Civil War reenacting, but not at the same time.