Make it happen with a multiuse machine
With a variety of price points, electrical requirements and weights, there is one to fit the needs of every woodworker {loadposition position10} Are you downsizing, running out of room in…
With a variety of price points, electrical requirements and weights, there is one to fit the needs of every woodworker
{loadposition position10}
Are you downsizing, running out of room in the shop, starting up a new business, setting up a home shop or do you just need more bang for the buck? Consider the array of multifunction machinery currently available. The majority of these machines have been made in Europe for many years and have been honed and refined so they are no longer just for hobbyists. Most models are currently made in Austria, Belgium, Czech Republic and Italy. While some of the manufacturers offer varying levels of machinery for different markets, they are all well-built machines engineered for specific tasks.
The main benefit of these machines is their space-saving ability. Up to five machines have been incorporated into just one tool. The work flow is designed to go in the same direction, so a rectangular shop will work just fine. The footprint is much smaller than dedicated machinery and, most important to fastidious woodworkers, is they are every bit as accurate as the single-use machines. Only one source of power is needed, saving on electrician costs. The main drawback of the combination machine is there can only be one operator using the machine at a time. There is also some conversion and changing of fences as needed.
There is a wide range of prices for these machines to fit every budget. With 50 percent of the market for this type of tool being for hobbyists and 50 percent for serious professionals in a production capacity, it is easy to see how the range of prices goes from $5,000 to $38,000 for the five-function machines. Just like all other tools and products people buy daily for work or pleasure, options and features make the difference. Some of these are "bells and whistles," but most of them are serious considerations. While many of the companies make standard models with certain features, like automobiles, some can be ordered to the customer's specifications and needs. Like most everything else, you get what you pay for.
Most of the machines sold are in the $8,000 to $15,000 price range, far less than if the machines were purchased separately. These machines are bought for a lifetime, not just a single job, so look for an array of features when purchasing combination machines.
Safety first
These machines have certain inherent basic design concepts. One of the most impressive is the concept of safety. There are integral blade guards, dust collection hoods, riving, magnetic on/off switches and anti-kickback fingers. The next set of features are the capacities available; saw blade sizes go from 10" to 14" with scoring units, no dado to 3/4" dado, shaper spindles go from 3/4" to 50mm, planer widths go from 12" to 20", thickness planers go from 6" to 9". Weights of the machines run from 550 to 3,100 lbs. Most of the combination machines come with three electric motors ranging from 2.5 to 10 hp each. Most of the five-function machines have a sliding table saw, shaper, jointer, planer and horizontal mortiser.
There are many other useful features available depending upon the model and manufacturer. For the saw portion, there are scoring blades, the ability to create compound miters, sliding tables and crosscut fences with flip stops. Planer knives, which double as jointer knives, can also come with quick-change Tersa cutterheads or spiral cutterheads with insert tooling. Shapers can have continuous variable speed and reversible rotation options along with tilting spindles. Power feeders are always a good plus with both production and safety benefits.
Through the years, much thought has gone into these machines to make them as versatile as possible. As each person's needs are different, one should consider both the job the tool will do and the physical constraints of the space and the user. One of the big factors in machinery purchases is weight and, while the quality of the casting and matching parts need to be true, it is the mass of the tool that will help to provide the best cut. When two or more tools are combined in the same machine, the result is larger mass and a better cut from all the tools.
The location of the tool is as important as to how it gets there. A shop with a forklift truck can easily handle any of these tools. A dolly is quite a different matter. It will take a few people to get the machine off the pallet and into place. Some of the machines come with a trolley or mobile base so they can be moved out of the way as needed. In addition, some of these machines can be separated into two halves to get them into smaller spaces, such as down steps, and then reassembled. Three-phase power is also needed for some of the machines.
In the case of combination tools, remember that a changeover will be needed between operations. The good news is the manufactures are aware of this and have made it substantially easier and quicker. It should take only a minute or two to change from one tool to the other. Repeatability is the real goal with these machines. Occasionally, one might find that a particular part was omitted or became damaged somewhere from the tree to the client and needs to be remade. Frequently, especially with any shaper, the setup time is longer than the actual run time. The solution is digital readouts and quick change spindles.
One-stop processing
These machines have combined sliding table saws with other tools best suited for the processing of solid wood. If all of your work is solely sheet goods, these may not be the best choice. However, for those that make furniture or who use solid wood in combination with sheet stock on a regular basis, it can make a large difference in the ease of the job. Everything is in one place, there is no need to run around the shop and transport your partially produced parts on carts.
In addition, most of the manufacturers make add-on attachments and aids, such as clamps and hold-downs, safety bar guides on the shaper fence, memory pins on the shaper fence. The sliding table fence with hold-down clamps can be used to hold pieces at 90 degrees as they go through the shaper for cutting copes on door rails or for supporting smaller raised panel pieces.
A combination machine would also make a perfect cell manufacturing station in a larger shop, such as one that produces solid wood gates and railings. First, joint and plane the stock, then rip it with a power feeder, profile it on the shaper, crosscut it on the slider and then use the mortiser for the joinery.
All in all, these are machines that have a slightly larger footprint than a table saw and are capable of five full machining functions. With a variety of price points, electrical requirements and weights, there is one to fit the needs of every woodworker.
Jim Falk is the owner of Progressive Wood Works in Port Chester, N.Y.
This article originally appeared in the January 2010 issue.
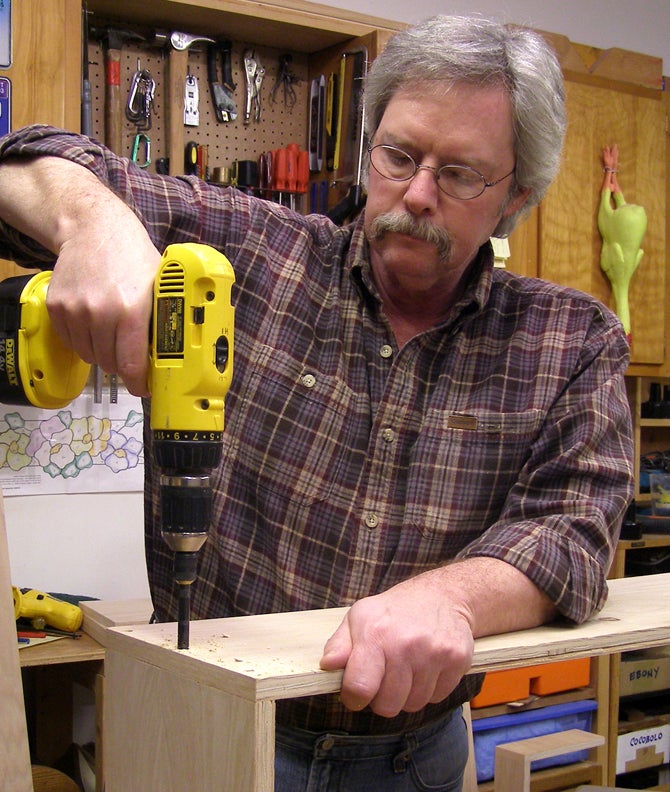
A.J. Hamler is the former editor of Woodshop News and Woodcraft Magazine. He's currently a freelance woodworking writer/editor, which is another way of stating self-employed. When he's not writing or in the shop, he enjoys science fiction, gourmet cooking and Civil War reenacting, but not at the same time.