Machine maintenance requires a database
In the second of a three-part series, our experts show you how to have your assets catalogued and scheduled for repairs {loadposition position10} Last month we covered the three main…
In the second of a three-part series, our experts show you how to have your assets catalogued and scheduled for repairs
{loadposition position10}
Last month we covered the three main principles of preventive maintenance: Keep your machinery clean, lubricated, and calibrated. With these principles in mind, we will endeavor to explain the basic concepts and commonly used practices for setting up a preventive maintenance program.
At some point, there will be a machine breakdown resulting in downtime and loss of productivity. This will have a ripple effect on the flow of product through your plant or shop. This can also have an impact on your ability to deliver finished goods to the customer or job site, which will have an effect on your business and could ultimately lead to the demise of a small shop. Not to be pessimists, but we live in a real world where machines break, parts wear out, operators can hit the wrong button, power fluctuates and compressors tripping offline can knock machines out or result in catastrophic crashes. We cannot see into the future, but we can actively shape the future. This is where an aggressive preventive maintenance program can significantly minimize machinery downtime.
The next logical question is: Where to start? To quote Stephen R. Covey in "The 7 Habits of Highly Effective People," begin with the end in mind. You must first determine what you want out of the program.
Take an inventory
A good place to start is to make a list of assets (machinery, critical hand tools and air compressors) to be included in your program. Copy all of the information from the machinery identification tags or plates, including the manufacturer, model and serial numbers, and electrical data. This information will be helpful for future data entry and machinery life cycle management. It's also recommended that you include the date of purchase, dealer and service contact information. This is especially useful when you need parts for repairs.
At this point, you may be surprised at just how many machines you have in your inventory. This list is also useful for determining the amount of insurance coverage you should have and will help expedite replacements should you ever have a claim.
Depending on the number of machines you have and how much time and money you want to invest, you need to make your first major decision: Do I invest in software and training? If you are a one-man shop and you are the only one running the machines, you may want to save the expense and do a basic spreadsheet with simple intervals. Alternatively, you could just mark critical maintenance intervals on your shop calendar. However, if you are a shop with operators or multiple shifts, you may want to consider a software package. There are many programs on the market, so the important factor here is to define up front what you want the program to do for you. Do you just want to track simple maintenance tasks? Do you require charting, reports, calculations for multiple shift intervals, mean time between failure, repair-part utilization, cost analysis and overall equipment effectiveness?
Another important question to consider is whether or not you have the necessary skills for this endeavor or will you have to have an employee input and maintain this information?
Creating a database
Once a tracking device/method is chosen, it will need to be populated with information. After you've created your machine inventory list, obtain the original equipment manufacturer (OEM) manuals. If you don't have the original manuals, which is not uncommon with older machinery, the Internet is a great resource for replacements. Most OEM manuals have a series of pages or even an entire chapter devoted to maintenance.
OEM maintenance schedules usually assume a standard 40-hour workweek. If you run more than 40 hours per week, you will need to recalculate the maintenance intervals. Similarly, if you are not utilizing your machinery full time, you will have to base your maintenance intervals on your best estimate of usage. Large machines like CNC routers and wide belt sanders often have hour/ETI meters either mounted on panels or viewable in the program/operator console. It may not seem like a major consideration, but during a busy period when you work overtime every Saturday for a month, you can easily place your assets in jeopardy. You are now a week behind on greasing and could set yourself up for catastrophic bearing failures. Scheduling plays a major role in the success or failure of the entire program.
During information entry, you should transcribe the maintenance tasks into the database. Maintenance tasks include cleaning, greasing/oiling, calibrating and inspections. Attach to your maintenance tasks any other pertinent information, such as lubricant type, frequency of task, estimated man-hours, required tools and special instructions such as lockout/ tagout procedures.
If your system generates work orders, this information can be a great time-saver for the person doing the repairs. The initial data input should include as much information as possible, since it is easier to create reports and do analysis/cost rollups if the data is present in the database. You may also want to use the database as a repository to capture information such as compressed air, dust collection, power and drain line requirements. You can go so far as to list machine dimensions, weight, center of gravity, location and type of lifting devices and how the machine base was set (complete with attached pictures) for future machine moves.
During the data collection/entry phase of the project, it is helpful to keep a separate spreadsheet listing the type and quantity of greases and lubricants used for each machine. This can help in minimizing your lubrication inventory.
Do not substitute grease or lubricants on machines under warranty without the written permission of the manufacturer. Failure to get authorization for substitution could void your warranty. Also, when making substitutions, be sure you understand the base stock and additives of the lubricants chosen for substitution. If you are uncertain about lubrication substitutions, contact your local distributor and ask to speak to a lubrication engineer or certified lubrication specialist.
The same concept applies to minimizing your inventory of cleaning agents. Some cleaning agents are caustic to O-rings in pneumatic cylinders, some react with the metal or paint on machines and some can cause rust. A small patch test is a good place to start. As always, when in doubt, check with the manufacturer or machine supplier/dealer; cover yourself by getting the substitution in writing and clearly have a name or point of contact with their phone number, address and the date you spoke with them.
Selling the program
So far you have seen the need for a preventive maintenance program, you have made a list of machines and determined just what you want your program to do for you. You've gathered manuals, pulled out the maintenance task list information and entered it into a database. This has enabled you to consolidate your cleaning agents and lubricants.
Your preventive maintenance program is almost ready for use. At this point, it would be advisable to gather your employees and explain the program. By creating some enthusiasm and getting the buy-in of your employees, you will jump-start the program and help ensure its success.
Next month we will cover scheduling, tracking, reporting, request for quotation and machine-analysis baselines.
Patrick Molzahn is the director of the cabinetmaking and millwork program at Madison Area Technical College in Madison, Wis. John Nichols is a senior maintenance manager at Techline USA in Waunakee, Wis.
This article originally appeared in the June 2010 issue.
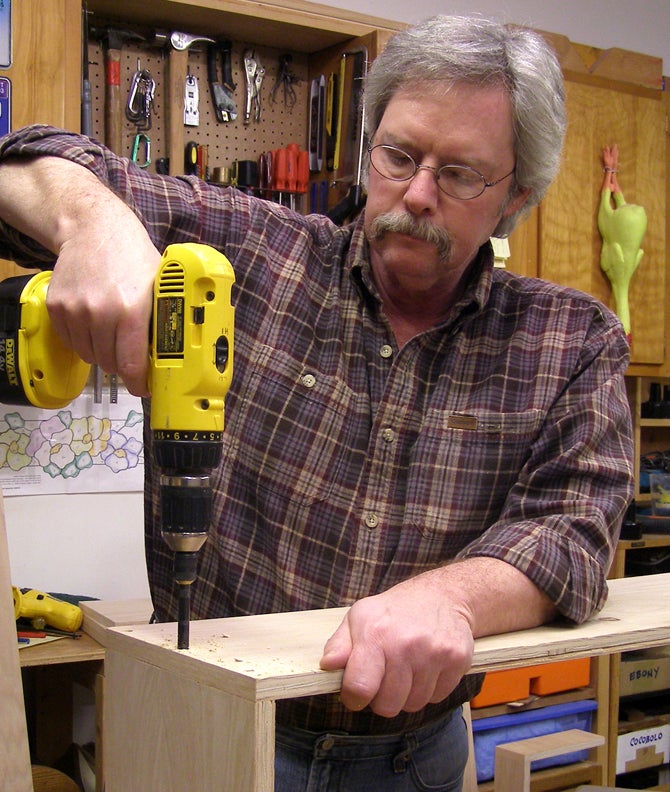
A.J. Hamler is the former editor of Woodshop News and Woodcraft Magazine. He's currently a freelance woodworking writer/editor, which is another way of stating self-employed. When he's not writing or in the shop, he enjoys science fiction, gourmet cooking and Civil War reenacting, but not at the same time.