Linear guide rail system: weighing pros and cons
My previous two articles covered the two major sub-assemblies of a CNC machine: stepper and servo motors, and linear drive systems. Our tour is almost complete with a description of…
My previous two articles covered the two major sub-assemblies of a CNC machine: stepper and servo motors, and linear drive systems. Our tour is almost complete with a description of the linear constraint systems. This term is used to describe the structure or frame of the machine and the linear guide system, which is attached to the frame and allows movement of the machine’s axes.
We probably all have a trusted woodworking bench. If it’s like mine, it has a thick, heavy top and stout legs and cross-bracing to support the weight and to deal with the static and dynamic forces generated from sawing, planing and pounding. It’s built for a purpose and serves its purpose quite well.
Commercially built CNC machines that cut wood, foam, plastics and aluminum stock have framing elements of steel, aluminum or both. And, like all things in life, there are positives and negatives to both relative to the intended use. Generally, the larger the machine is and the faster the axes move, the heavier and more substantial the machine’s framing will have to be. A CNC machine that has a cutting area of 10’ x 5’ with two 25-hp variable-frequency-drive spindles and an automatic tool changer used in a high-speed production environment is going to have and need more mass than one with a 4’ x 4’ cutting area and single 3-hp router.
Steel or aluminum
The steel base frames and the X- and Y-axes of the larger production-oriented machines tend to be made of welded steel. Relative to the final costs of these types of machine, the steel stock and the bending and welding of it makes for rapid and efficient production of the frame and axes. Steel is easy to finish by sand-blasting and then spray-painting and is easy to machine, specifically to flatten areas for the mounting of linear guide systems for the moving axes and to then drill and tap holes to bolt the fixed portion of the linear guide systems to the steel framing.
For a smaller, low-speed production machine, the base frame and the X- and Y-axes are generally made with extruded aluminum. T-slotted profiles are bolted together using gussets, T-nuts and bolts. Relative to the final cost of such a machine, this is also a rapid and efficient production method. Aluminum T-slot profiles are the more common material used in many of the fences on stationary woodworking power tools, such as table saws, band saws and router tables. Post-production machining prior to mounting the fixed portion of the linear guide systems is generally not required because the surface of the extruded aluminum is flat and true.
The choice of which material to use in the construction of the machine base and the moving axes, and how to join them, is ultimately based on the intended use of the machine rather than any attempt to distinguish one as being better than the other. What is best depends on the production uses of the CNC machine, which can vary from a high-speed production environment producing cabinets to a small one-man shop producing custom furniture.
Tracks, rails and trucks
The linear guide systems are the interface between the base frame of the CNC machine and the mounting point of the axes and their drive systems. The idea of a linear guide system is what a woodworker sees in the miter slot on a table saw’s top that constrains a miter gauge’s movement.
The linear guide system come in an astonishingly wide variety of forms, though they are primarily comprised of two parts. The first is a rail, either flat or round, and the second is a truck that rides on or within the rail, depending on the type of rail. To the truck is attached the moving axes of the CNC machine. The trucks are quite complex and use a wide variety of methods and materials to help this load-bearing device slide easily on or within the guide rail.
Some systems use a rail that looks like T-track and the truck has ball-bearing mounted rollers that ride within the T-track-like rail. Others are just the opposite, having the rollers or linear ball-bearing units ride on the outside of the rail. Another option is extruded aluminum T-slotted profiles with integrated steel guide rails for the trucks to ride on.
Again, there’s not an ultimate linear guide rail system. You want the best system to handle the demands of the particular CNC machine. A heavier system, with automatic lubrication and self-cleaning features, would be needed for a large production machine, while lighter rail and truck system is often the choice for a CNC machine used to make one-off pieces of furniture.
This article originally appeared in the October 2014 issue.
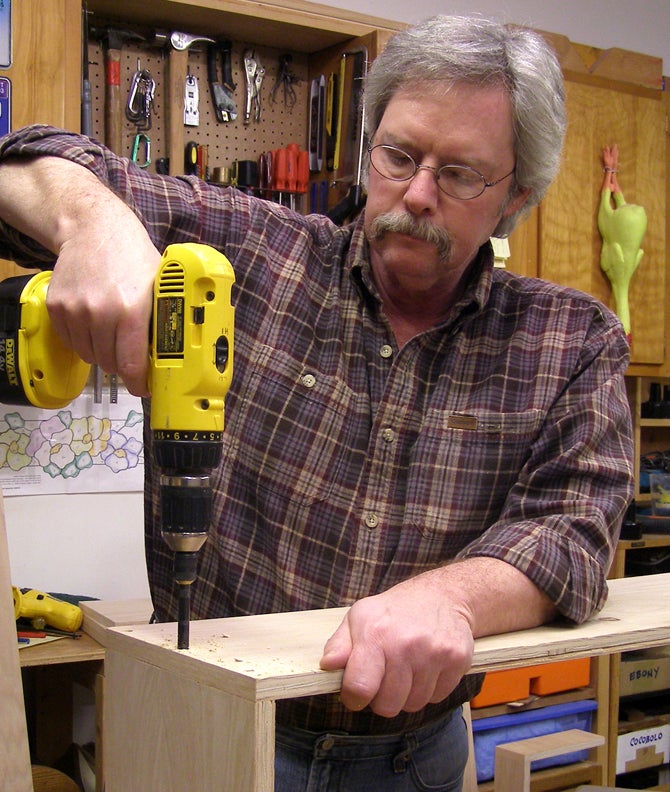
A.J. Hamler is the former editor of Woodshop News and Woodcraft Magazine. He's currently a freelance woodworking writer/editor, which is another way of stating self-employed. When he's not writing or in the shop, he enjoys science fiction, gourmet cooking and Civil War reenacting, but not at the same time.