Lean techniques start with traffic flow
This is a four-part series on lean manufacturing for custom shops. Part 1 covered the importance of a clean and organized shop. Part 3 will cover proper batch sizing, while…
This is a four-part series on lean manufacturing for custom shops. Part 1 covered the importance of a clean and organized shop. Part 3 will cover proper batch sizing, while Part 4 will focus on getting employees to “buy in” to the techniques.
So your shop is clean, and the organization of tools, materials and work space is ongoing. Now we can start to dig into lean manufacturing techniques. At this point, many of my clients say, “OK, I understand how lean manufacturing can work for Toyota or Ford, but I am a custom shop. Every job is different; no assembly line here.”
Your end product — cabinets, furniture, millwork or parts for other shops — might be different with every job, but the steps taken to make those parts are often the same, especially at the beginning of the process. Every board brought into your shop goes through the same steps to become usable parts, so let’s start from the beginning.
Lumber and sheet goods are brought in through your loading door. How are they brought in? Where are they stored? Do you find yourself moving material around to make room? Are the sheet goods stored close to the CNC or panel saw where they will be processed? Even before a single piece is cut, you might find wasted time and effort. I am convinced that material handling is where most businesses will find the quickest benefit from adopting lean techniques, and all of these articles will touch on this topic. So watch how your team brings materials in and how they flow from storage to the shop floor. Odds are you can find efficiency even before the actual work begins.
What goes in …
Following the material into your shop, look for the common tasks that are done over and over. Pretty much every sheet of plywood needs to be reduced to individual parts. In your shop, this may mean going to a CNC or panel saw, a sliding table or conventional saw. However you are reducing the sheet, watch how it is being handled. Is one worker struggling to carry and balance the sheet and load it onto the machine? Do any carts or racks you are using help or hinder the process? Your forklift can easily set a lift of plywood next to the CNC, but as the stack gets lower, is your operator struggling to load the machine? Adding a lift that raises the stack so that every sheet is level with the CNC table can help.
Even in very small shops that do not use entire lifts of ply, having carts at the right height can speed the process. And if you are using MDF, this becomes even more important, since full sheets are cumbersome for one person to move and lift. Having carts that are the same height as your saw makes the cutting process faster and less strenuous for operators.
Rough lumber also has to undergo a number of common procedures before taking a more “custom” path. Every board must be rough-cut to length, face-jointed, planed to thickness, edged and ripped to width. That’s pretty much every board, every time. These are the type of common tasks that beg for lean manufacturing techniques.
Watch the flow as boards are prepped. If the boards move past the jointer to be crosscut to rough length, there may be an opportunity. Can a chop saw be mounted near the lumber rack so boards can be initially reduced as it is stacked onto the cart?
A shop I worked with had a big 16”-wide jointer and a 20” planer positioned so that the stock could flow around a corner from one to another. But through the years, new equipment added to the shop narrowed the aisle next to the jointer so that carts of stock had to be moved around a large saw station rather than following the shortest path between machines.
This was made worse by the fact that, after planing, all the stock had to return to the jointer for edging. Without spending any money on new equipment, the cabinet saw was repositioned so that the stock cart could be parked in the center, and all three machines could be fed in turn without moving the cart. In reality, a “work cell” was created where stock could be prepped with a minimum of movement. In addition, this removed the cart from a main travel aisle so that stock being prepped was no longer interfering with other traffic moving around the shop.
Must come out
Keep following the stock through the shop. A client of mine makes a lot of drawers for retail sales counters. While the drawers are different sizes and do not get made every day, we decided that a dedicated router table set up with a drawer lock bit was the way to make the boxes. All joints are cut on the same setup and the table is on wheels. When needed, the router table can be rolled to the where the stock is and is instantly ready to use. The table was built in the shop with a dedicated router. Tackling this common task with lean techniques cost less than $300, saves setup time and allows somewhat unskilled laborers to successfully manufacture and assemble drawer boxes.
At some point along the flow, the parts do diverge to the point where there are no more common tasks. A stick that is destined to become a door stile or a turned appliqué will not share much after initial stock prep. But each part needs to be moved around the shop and prepared for shipment.
You’ve looked at how materials are brought into your shop and stored. It’s also important to examine how finished parts are stored and shipped. When the parts of job A are loaded onto the truck, do the parts from job B and C have to be shifted out of the way? This goes back to the organization we discussed in the last column, and if you are shifting parts around to access the ones you need, there is obviously room for improvement.
Where are the common tasks that most or many of your projects share? With these tasks identified, lean manufacturing techniques can be applied to answer the question, “How can we do this better?”
Ralph Bagnall is a woodworking consultant and author. He can be reached through his website at www.consultingwoodworker.com.
This article originally appeared in the November 2011 issue.
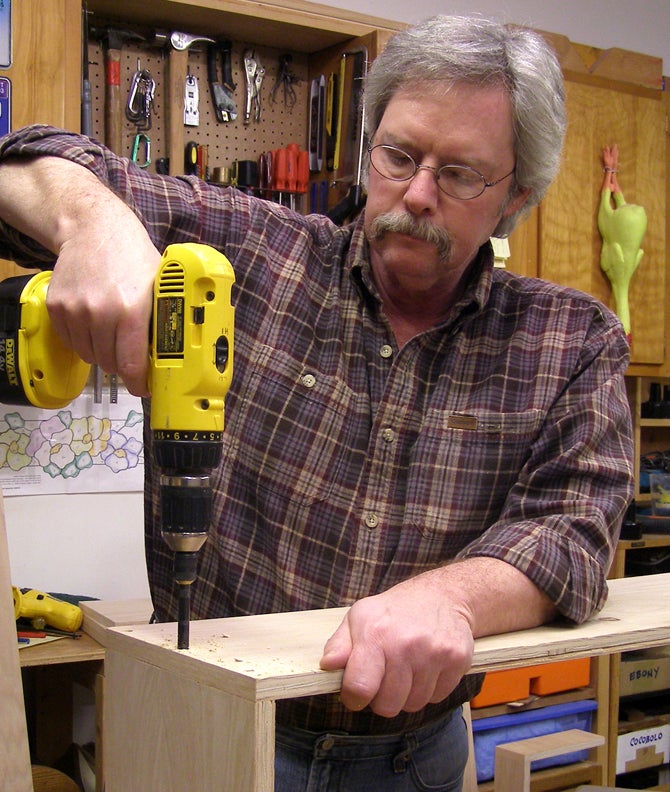
A.J. Hamler is the former editor of Woodshop News and Woodcraft Magazine. He's currently a freelance woodworking writer/editor, which is another way of stating self-employed. When he's not writing or in the shop, he enjoys science fiction, gourmet cooking and Civil War reenacting, but not at the same time.