Join the desktop revolution
A desktop CNC router is an entry-level machine that is relatively inexpensive, physically quite small, and offers a user-friendly introduction to computer aided design (CAD) and machining (CAM).
A desktop CNC router is an entry-level machine that is relatively inexpensive, physically quite small, and offers a user-friendly introduction to computer aided design (CAD) and machining (CAM). It’s an ideal choice for woodworkers who design and build a lot of one-off custom parts or do short production runs, and who now feel ready to automate some tasks.
It’s also a solid complement to other tools and machines in a creative environment known as a makerspace. That’s a word that came out of the need for schools and colleges to allow students to create with their hands. Today, the term has been adapted to include artists, engineers, hobbyists and a host of other creative people, including woodworkers. The core machine in many makerspaces is a versatile desktop CNC because it encourages people to conceive, design, and then actually build in three dimensions.
Just because they’re small, don’t think of these machines as limited. They’re by no means confined to creating one-off prototypes. Many of these powerful yet affordable little machines can also be used for runs where they might make all of the raised panels for a kitchen, or perhaps mill identical components for RVs, or carve bodies for electric guitars. The ability to repeat accurately – to make the exact same part more than once and keep the electronic instructions on file for a later date if the task needs to be repeated down the road – is another key value that a desktop CNC brings to a small shop.
So many choices
There’s a lot to consider when investing in one of these machines. The first question that most people ask (and this seems counterintuitive when you consider that these are ‘desktop’ models) is how large a project can it handle?
First off, there are three dimensions to consider, not two. Many manufacturers list the workable space (also called the envelope) in terms of just width and length (X and Y). That’s fine as long as the woodshop is only going to work on relatively flat surfaces in the vicinity of, say, 3/4” thickness. But if parts are thicker than that, or may possibly be in the future, then one needs to also ask about the Z axis – that is, the maximum height available for a workpiece after the router bit has been installed. One of the constraints here is the height of the gantry (the moving bridge that holds the motor).
Many manufacturers also offer more than one table size in each model, and some offer choices in gantry height, or even extensions that can be added later. Another constraint is the range of motion – how far can the machine’s motors move the bit up and down.
Some machines confine the work in both flat dimensions (width and length). That is, the entire workpiece must fit on the table. But other machines are open-ended, so while the width might be constrained the work can be as long as needed. A 24” x 36” working space is about the limit for most desktop units (although a few will reach as far as 48”), and that’s large enough for most cabinet and panel work.
While not strictly ‘desktop’ models, some of the new portable CNCs don’t even have a table: they just sit on the workpiece and rout a specific area. Then, the operator moves the unit a bit to cover a neighboring area, or the machine moves itself as it works on a large project by breaking it down into small frames that it completes one after the other.
Many desktop CNC units use the guts of a standard handheld router to spin a bit. The manufacturer just removes the router motor from its base and pops it into the machine. Others come with electro-spindles, which are dedicated CNC motors that can add quite a bit more performance to the machine than a basic router can. They are either air or liquid cooled (the latter is preferable for longer production runs), and some machines offer choices based on the power configuration that’s available in the woodshop.
Some of the smallest desktop CNCs run on household 120-volt single phase current. Midsize models often draw 220 volts, and a few of the larger desktop machines offer the option of going with 3-phase. Choosing the level of power will depend on what you’re going to ask the machine to do. For example, a thin engraving bit needs a lot less muscle than a large carving bit.
The brains of the outfit
For many woodworkers (especially us old galoots), the scariest thing about CNC routers is not the physical aspects, it’s the darn computers. For somebody who has always drawn on graph paper or is barely familiar with rudimentary design programs such as SketchUp (sketchup.com), the idea of learning a whole new skill can be very intimidating. And the people who sell these machines often don’t help alleviate those fears. They start out fine, but within a few sentences they just leave the uninitiated behind as they gradually sink into a fog of technical lingo. They don’t understand that for some of us, a toolpath is still those flat pavers leading from the parking lot to the workshop.
The good news is that the programs are getting much more intuitive and user friendly. Yes, there’s still a learning curve, but it’s a whole lot shorter than it used to be. Most programs have dropped templates on top of the programming language, so that the woodworker now interacts with the software in relatively plain English. There are libraries of pre-drawn cabinets where the operator (that’s you) can pick out a sink base or a wall cabinet and may only have to change the width in a simple dialog box to make it a completely custom fit.
Some software packages require two separate programs – one for designing (CAD), and another that exports the design files and uses them to tell the machine what to do (CAM). But there are several programs available now that simplify that process. You make a change in the design, and it is automatically adjusted in the instructions to the machine.
There’s also a fear when buying a machine that it will be difficult to get help with both technical challenges (just running the machine) and also abilities (opening up its full potential). The manufacturer will usually offer tech support, but it’s a really good idea to explore the nature of that before buying. Some companies are always at the other end of the phone and never charge a fee, while others make a customer scroll through hours of useless and unrelated files on their own to try to find the solution by themselves, or else they charge for support by the hour or by the incident. And many small desktop CNC builders offer no support whatsoever. They just leave it up to a buyer to search for solutions through online user groups, chatrooms, billboards, social media and the like. So, ask about support. And especially ask about live human beings who answer phone calls or emails, and whether or not they charge.
Unlike a large industrial CNC router, the manufacturer won’t be helping with the physical installation or have people on site to provide initial training for a desktop model. So, many professional woodworkers have turned to their local technical colleges to learn some of the basics before buying. You won’t need a four-year degree, but an evening or weekend class might be available where a woodworker can actually design something useful and then work through the entire process once or twice before buying. Plus, classes provide an opportunity to meet other people sharing the same questions, and also meet some people with the answers (faculty, guest lecturers).
Grow up!
Many desktop CNCs offer options other than just routing. Some can be fitted with other heads that will 3D print (make plastic parts one very thin layer at a time), or engrave other materials such as soft metals, plastics and glass. Some can grow as you do, offering larger tables and more powerful motors and spindles. Before buying, sit down with a salesperson and discuss where this new machine might lead you, and where you might want to go with it.
Even basic desktop machines can usually be outfitted with excellent dust collection, and some can be fully enclosed to manage both safety concerns and extraction. Many units can also be equipped with vacuum systems that hold the work in place. A vacuum table or clamping pods will eliminate the need for mechanical clamping. There have been more than a few neophytes who have programmed their router to try to mill right through a cast iron clamp or two, so vacuum clamps are definitely worth a look.
Some of the larger desktop units might be able to accommodate automatic tool changing. Other units have versions of aggregate heads or other innovative solutions such as ShopBot’s Rotary Indexing Head, which is similar to a lathe in that it allows you to horizontally rotate a part being cut or machined with fully indexed control of the rotation. This way, you can carve anything you want in the round.
This article originally appeared in the July 2018 issue.
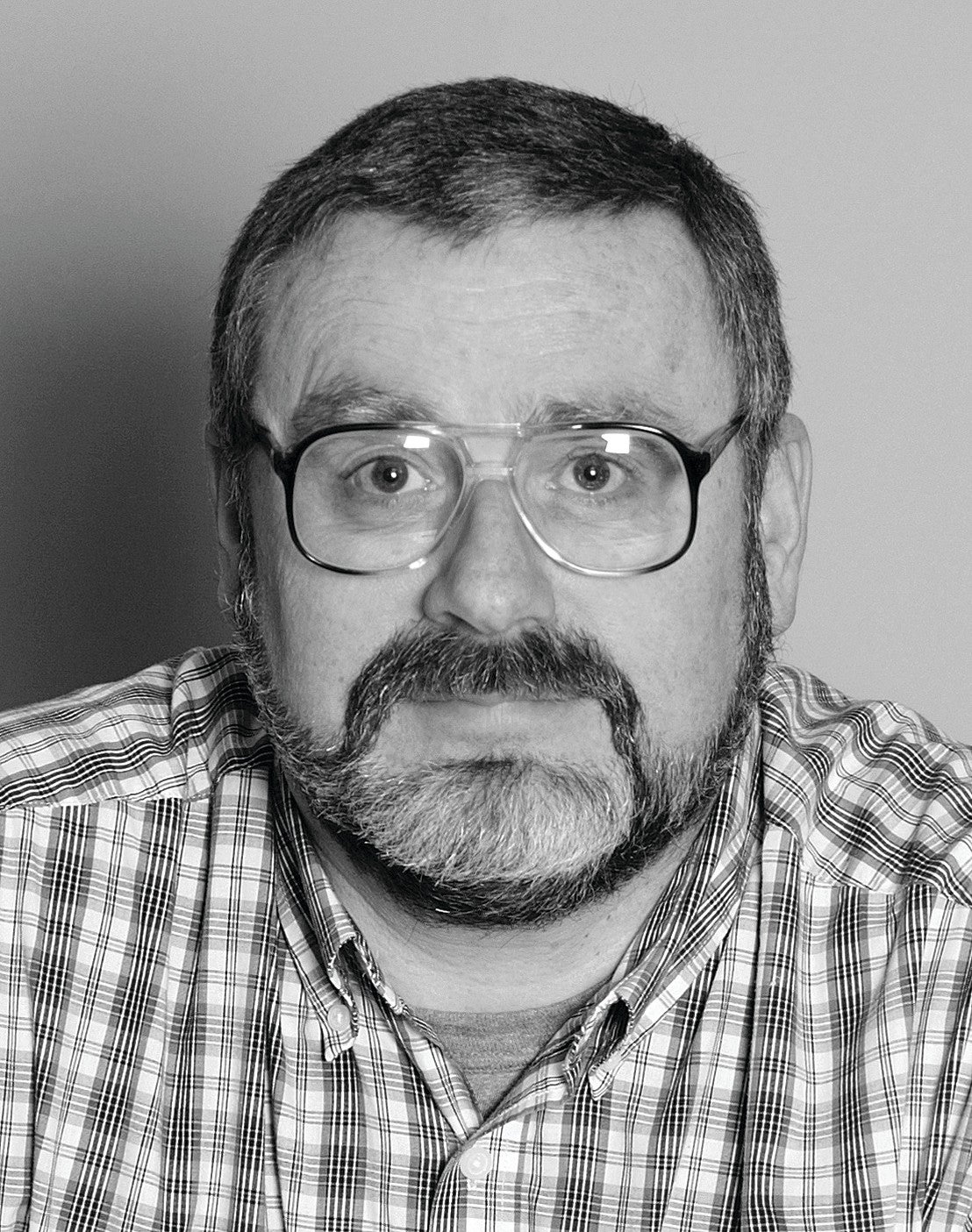