Industry will see more CNC innovation in 2012
Small woodworking shops were introduced to CNC machinery about 10 or 15 years ago. For most, the cost was prohibitive. For others, the thought of a robot doing their work…
Small woodworking shops were introduced to CNC machinery about 10 or 15 years ago. For most, the cost was prohibitive. For others, the thought of a robot doing their work was unsettling. But then the virtues of CNC machining began to catch on: incredible accuracy, repeatability — no lunch breaks!
Today, cost should no longer be an issue. There’s an affordable CNC solution for shops of any size. Several manufacturers have introduced low-cost bench-top models in recent years, while the technology and ease-of-use features currently found on sheet good-sized machines have never been more plentiful.
So what are the manufacturers thinking about in 2012? Woodshop News asked and here’s what they had to say:
“There have always been low-cost CNC machines, but tremendous sacrifices have been necessary in the past to meet the price point for those machines. The consequence has been very poor performance in terms of accuracy, edge finish and machine reliability and that has been primarily attributed to insufficient frame designs,” says Robert Alsup of Laguna Tools.
“Continual innovation in CNC machine frame technology at companies like Laguna Tools, along with the standardization of motion control components, has made it possible now to make an affordable CNC machine without sacrificing performance. This places CNC technology within the reach of smaller wood-product companies that in the past could never justify the capital investment.”
Laguna has recently developed the Touch CNC control with B&R Automation in Austria, which eliminates the requirement for Microsoft Windows as part of the machine control system and greatly increases machine performance and reliability while providing a very intuitive operator interface that is both easy to learn and use, according to Alsup.
“The new design software business model for the industry has to be based on a CNC machine investment from $25,000 to $45,000 for cabinet shops. We saw the beginning of that trend last year and it will continue into 2012 and beyond and it is forcing the software companies to change their distribution models in order to meet those pricing goals,” says Alsup.
“The nested-based manufacturing concept (NBM) that was developed 15 years ago changed the cabinet industry. Prior to that period, cabinets were made on table saws and in cabinet factories. NBM allowed small- to medium-sized companies in the industry to compete with the largest manufacturers. Only a decade ago, a typical cabinet shop would invest nearly $200,000 in a CNC machine and cabinet design software package. In those days that amount was more than the business owner paid for his house. That investment is more along the line of the cost of a new pickup truck [today].”
An educated guess
“Small shops need to automate their businesses. If they don’t, they’re going to have a rough go because labor costs will just consume them,” says Steve Stevenson of General International, which is targeting its desktop models to the education market.
“Seventy-five percent of our market continues to be education,” he says. “We never anticipated the kind of interest that we were going to generate. It completely revolutionized our CNC program.
“There have been lots of schools that have tried to integrate CNC in the past, but never very successfully. The schools really didn’t have the full support of manufacturers; they didn’t have local distributors, they tried to use software that was far too complex. We tried to look at all of those problems and solved the mechanisms.
“That translates out to the small shop market as well because they really have the same problems that high schools have. The owners don’t have a lot of aptitude when it comes to CNC. They need somebody to hold them by the hand and take them through the process. For lack of a better term, we wanted to create ‘CNC for Dummies.’
“As we’re developing products now, our focus has moved away from the larger industrial applications — which in this economy are still struggling — and quite frankly there are tons of manufacturers in that realm. We thought we’d run on the road less traveled; albeit a more challenging road because you’re dealing with [shops] that don’t have programmers and designers on staff.”
“The education angle is interesting,” says Ted Hall, founder and CEO of ShopBot Tools. “The STEM emphasis — science, technology, engineering and math — has caused a lot of people to get more interested in CNC and digital fabrication. Little tools are easy for teachers to start integrating into their lessons so we, too, see a lot of interest from education.
“We see a lot of creative people coming through our training. They’re doing woodworking, but they’re doing unusual pieces that don’t fit into the standard cabinet software model. The nice thing about our CNC tools — or anybody’s really — is you just click a button and the tool’s ready to do something else.”
Something for everyone
CNC machines have become the equipment of choice for shops of all sizes, says Jeff Conger, Weeke product manager at Stiles Machinery.
“Very few companies these days produce huge production quantities anymore, resulting in the need for flexible, easy-to-set-up and change-over CNC machines,” he says.
“A CNC machining center can perform duties ranging from horizontal and vertical drilling to routing, grooving and sawing in less space and time than other machinery. Smaller machining shops and millwork companies are among those that have benefited from the expanded use of CNC machines on a wide range of materials that include honeycomb composites, solid wood, plastics and aluminum. As rapidly changing designs of products force the need for machines to be up to the challenge of cutting these, we are also seeing a large push for machine builders to design equipment that is versatile enough to handle many various substrates.”
Shops are asking for machines with smaller footprints, automatic feeding, faster unloading, automatic part identification and multiple processing zones, according to Conger.
“Industry leaders say they also expect to see a greater range of production, safety improvements and better diagnostics provided by CNC machines. Simpler controls that make the machinery easier to add to a manufacturer’s network will also speed operator training. In addition, makers of wood and related products may experiment more with robotics, which have seen some success in metal works.”
Cesare Magnani, sales manager for Biesse, says customers continue to seek more value and better performance from their CNC machines.
“Reduced setup time is an area where it is always worth investing as it minimizes the machine downtime and increases output. The main area of focus is the machine table where operators can spend lots of time setting up. For this reason, the new worktables are becoming smarter to allow instantaneous vacuum configuration change between sheet sizes and quick switch between applications.
“Customers have also been voicing an interest for added versatility; such as having CNC machines capable of handling more applications. This goes hand-in-hand with the request of minimizing setup time. The added versatility in the new generation of CNC machines is provided by more capacious tool changers, more powerful electrospindles capable of handling different materials and multifunctional tables that are easy to set up and include features designed to minimize the need for custom fixtures.”
“Many woodworking shops that survived the recession have learned about controlling overhead costs,” says Roy Valentine, sales manager at Techno Inc. “I believe 2012 will yield considerable growth in the purchase of affordable CNC router equipment. These purchases will allow shop owners to add capability, increase production volume and improve quality, while controlling their spending thus making them more profitable.
“We have spent the last two years redesigning new equipment and gearing up our new production facility preparing for this market change. We’ve invested millions of dollars in this project and know our new HD and HDS Series equipment will be the industry leader. We’ve designed these new routers only using the highest quality components, and concentrated our efforts on ease of use, so that shop owners get a return on their investment quickly.”
The last words
“We see the trend for 2012 directed at eliminating/reducing the non-productive time in CNC machining,” says Michael Cassell, North American CNC product manager for Holz-Her U.S. “In nested-based manufacturing this is time spent on labeling and unloading of cut parts. Systems are now being introduced that provide automatic loading of new panels along with the pushing off of finished parts, all in one motion. This system now provides us control of the time this action takes instead of relying on manual load/unload with no predictable amount of down time. Further there are systems now offered which will automatically print and place labels on the raw panel prior to loading, as this is accomplished while the previous sheet is being machined there is no addition time spent on this function.
“In point-to-point style machining, setup time is addressed with the implementation of automatic position pod and rail systems. As the control knows where and what machining functions are to take place on a specific part it can accurately calculate the best position of consoles and vacuum pods. These systems will automatically move pods and rails into position while a part is being cut in the opposite zone. This allows for efficient pendulum processing and elimination of set up time.”
“The primary trend we have seen for the past few years is the movement to space saving, fixed table, moving gantry machines with automatic tool changers,” says John Harris, director of sales and marketing at MultiCam. “These machines are economical, flexible and can be outfitted with automatic load and unload devices to boost productivity. In large companies, we see a trend to cell-based manufacturing with multiple small single purpose machines.”
There will be “more emphasis on software and ways in which costs can be reduced by running machines more efficiently,” adds Robert Marshall, marketing manager for AXYZ International. “Also by implementing Internet-based ‘cloud support’ technologies, we can provide faster global support to customers but at the same time reduce travel time, costs and carbon emissions. The new AXYZ A2MC controller is the most versatile of its kind, runs machines faster and smoother and also has full Internet connectivity for remote diagnostics, auto-updating and cloud support.”
This article originally appeared in the February 2012 issue.
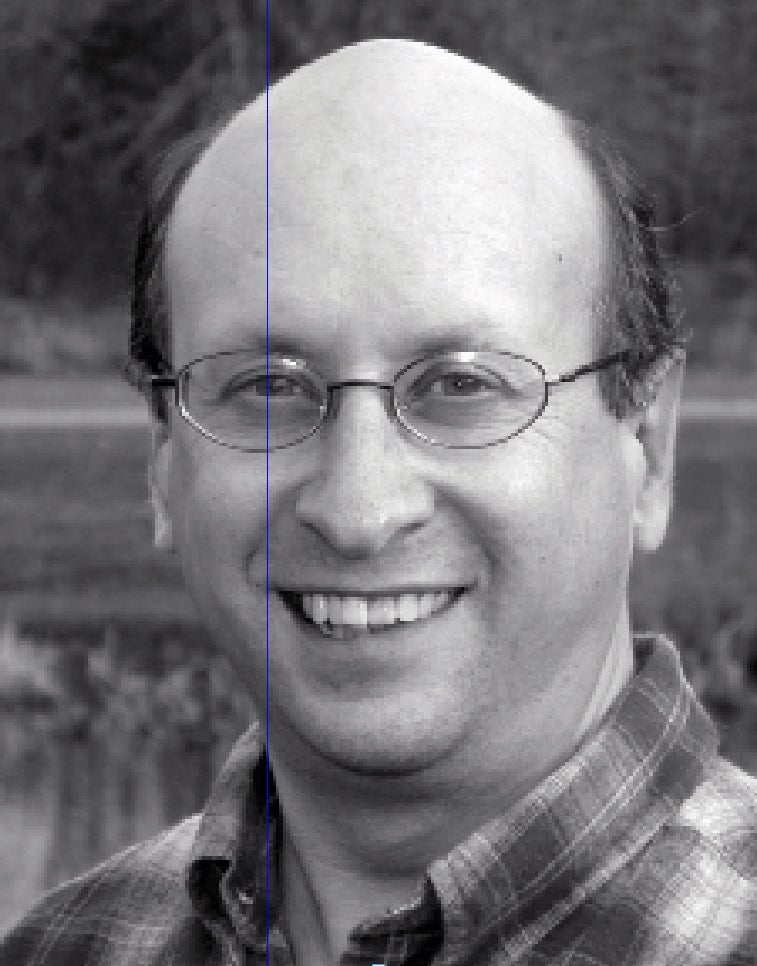