Getting past the spin when it comes to spindles
The last piece of non-consumable hardware of a three-axis CNC router is the spindle. Many woodworkers already own a spindle, though they know it as a router. A hand-held router,…
The last piece of non-consumable hardware of a three-axis CNC router is the spindle. Many woodworkers already own a spindle, though they know it as a router.
A hand-held router, or one mounted in a router table, has traditionally been an induction alternating current motor with brushes and a collet on one end of the motor shaft, all contained in a frame. Attached to or part of the frame are mechanisms to adjust the depth of the cut relative to the base of the router or surface of the material being cut.
This type of spindle is well-known: inexpensive, dependable, easily repaired and there are an enormous variety of router bits to use with it. Sure, a router makes a lot of noise, but most shops have several and they’re used daily. But this type of spindle is most commonly used with a bench-top or low production CNC machine.
The other choice is a brushless spindle, which uses magnets rather than brushes in the motor’s operation. This type of motor can be run with either AC or DC current and requires a variable frequency drive to control the frequency of the electrical power. The goal is clean and smooth power.
Brushless spindles are more expensive but better suited for high-production CNC machines. They can run all day — cooling can be accomplished with a fan, compressed air or liquid — and are much quieter than a traditional router.
Manual or automatic?
After deciding on a spindle, the next decision concerns manual or automatic tool changing.
In the U.S., most traditional routers are sold with collets to accept bits with a 1/4” or 1/2” shank. The collet is actually two pieces: a set of tapered cylindrical jaws and a nut that is sized to the collet jaw. The quality of a collet and bit is determined by total indicated runout or how far the bit’s rotation is from a theoretical straight line drawn through the motor shaft. Since a major benefit of CNC machining is accuracy, it only makes sense that you’d want to use the most accurately made collet and bit.
While it is easy to change a bit in a traditional router — manually, with one or two wrenches — the process with a brushless spindle is nearly identical to the one for metal working machines.
The inside of a brushless spindle’s motor shaft is slightly tapered; wider at the end and narrower up the shaft. There are many different taper dimensions, based on a variety of technical issues, and the spindle manufacturer can recommend the appropriate taper based on a specific use.
This interior taper in the motor shaft allows for quick tool changing, whether it is done manually or with an automatic tool changer.
In an earlier column, I discussed how G-Code tells a CNC router to move in a given direction for a given distance and at a given depth to complete a job. G-Code also tells the spindle to move to a location away from the work surface to change tools, either manually or with an automatic tool changer. With the latter, the G-Code provides instructions to unload and load a tool or tools and then resume cutting.
Though this all sounds horridly sleep inducing, once the tool changing G-Code sub-routine is programed a few times, it is relatively easy. Promise.
What should I get?
Whether you are buying or building a 3-axis CNC router, decisions will have to made on the type of spindle and whether to use a manual or automatic tool changer.
A small shop with lower or set production requirements can easily be satisfied with a traditional router and manual tool changer, especially if only one type of bit will be used most often.
For shops planning to invest in a high-production machine, a brushless spindle and automatic tool changer is probably the way to go. The size of the spindle, type of collets and size of the automatic tool changer should be selected after consultation with the CNC router’s manufacturer.
This article originally appeared in the December 2014 issue.
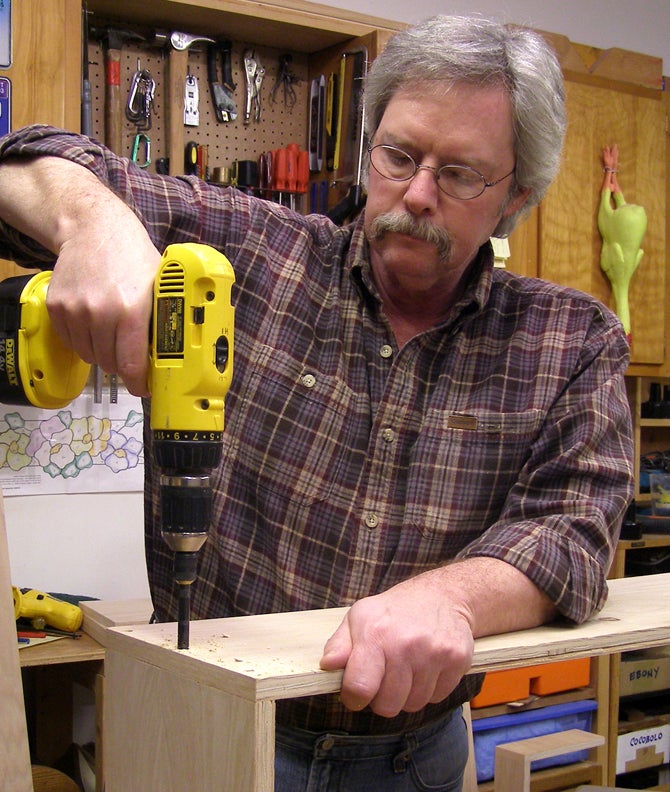
A.J. Hamler is the former editor of Woodshop News and Woodcraft Magazine. He's currently a freelance woodworking writer/editor, which is another way of stating self-employed. When he's not writing or in the shop, he enjoys science fiction, gourmet cooking and Civil War reenacting, but not at the same time.