Custom shops can harness lean processes
Most of us have heard of lean manufacturing. We have read the articles in praise of Toyota and Ford and many other manufacturers that improved the quality and efficiency of…
Most of us have heard of lean manufacturing. We have read the articles in praise of Toyota and Ford and many other manufacturers that improved the quality and efficiency of their operations. We have heard experts using terms such as “Kaizen,” “Kanban,” and “Heijunka” and wondered if they were just making stuff up.
Many shop owners have serious reservations about lean manufacturing — and with good reason. Lean was developed for manufacturers who make the same product over and over. And most woodworking shops are custom, where every job is at least a little different than others. Shop owners suspect (and I agree with them) that the experts and consultants have worked to complicate and mystify the process in order to charge fees for classes and consultations.
These are, in my opinion (and I am a consultant), valid concerns, but lean manufacturing can have great value in any sized shop, including those that are strictly custom. You may not make a thousand widgets a day, but every rough board brought into your shop goes through the same process to prepare it. A cabinet shop brings in lifts of plywood that will be processed into many different parts, but the holes, dados, rabbets and grooves are all similar from part to part. These common tasks are where lean techniques can be effectively applied in any shop.
This is the first in a series of four articles designed to demystify lean manufacturing, to see how simple it can be to make your shop more efficient and profitable. Working with my clients, I have learned that lean is actually quite simple, and the techniques can be adapted to any specific shop structure. Even better, it does not have to cost a lot of money. In reality, my clients have found that done right, money is saved from Day One and the cash can be used to fund further improvements as your plan moves forward.
As we move through this series, I will not be telling you what to do. Lean is not one-size-fits-all. Your shop is unique. You and your workers have a unique mix of skills, knowledge and biases, and the floor plan and the tools you use all make your situation one of a kind. So I hope to show you how to think lean and apply these ideas in ways that work for your shop.
What is lean?
Lean is nothing more than constantly making small improvements to your shop. I preach that every employee, every day, on every job, should be thinking: “How can we do this better?” This is the core value of lean. A little more efficiency every day is the goal.
Nothing will get you hooked on lean better than seeing real results (cash in your pocket) very quickly. So the starting point — and not coincidentally the first principle of lean manufacturing — is to clean up the shop. It starts with cleaning off benches and workstations, storage areas, sweeping the floors — all of it. Don’t forget work vans, trailers and such as well.
Ninety percent of the shops I have been in during the last 20-plus years need such a good cleaning. I can virtually guarantee that you will find tools you thought were lost, discover hardware that you did not know were in inventory and, yes, even that rub collar for the shaper for which you were about to order a replacement. Those items all represent money that you do not need to spend now to replace them. That is real cash that stays in pocket.
More than that, a clean shop is more safe, efficient and just more pleasant to work in. Less time moving stuff around, making room, tripping over scrap on the floor and looking for your square. Every wasted minute saved is a minute that can now be devoted to actual, billable production.
Be ruthless
While you are at the cleaning thing, don’t forget the cutoff and scrap piles. While some off-cuts should be saved, most often the time spent digging through the pile probably costs you more in labor than simply using new. A plywood scrap pile will rapidly fill any space you devote to it and just be in the way. Be ruthless as you clean up and make sure you only save things that make sense. Again, there is no hard and fast rule. For example, a stair company I have worked with uses a lot of hardwood for making up treads, but any crosscut leftovers less than 30” in length were not usable for most tasks. So they kept a few small bins for these shorts, but the rest were thrown out. Otherwise, the shop would be overrun in short order.
Once your shop is clean, the next task is to begin to think about how to keep it that way. Look around. Do you have enough trash barrels? Do cutoffs stack up behind the chop saw or is there a barrel nearby? Is the chop saw connected to the dust collection system or does the dust just pile up on the bench? Are there brooms and dust pans easily at hand so the routing mess can be quickly swept up and disposed of or is it too much hassle?
With the shop nice and clean, you have the opportunity to watch where and when the messes begin to build up again. This is the time to ask: “How can we do this better?” Adding a couple of trash cans, brooms and such costs you little and can be implemented quickly. Adding a drop from the dust collector to the chop saw may be a bigger task. If so, make a note and plan a time to get it done as soon as it won’t interrupt your work flow.
Evaluate
Organizing your shop is the next step, and it works in much the same way as improving shop cleanliness. Once all the tools are found and put away where they currently belong (done during the cleanup) you have the chance to evaluate if tools and materials are stored in the best locations or manner. You should notice that certain tools tend to pile up on a particular bench. That is logical since they get used there all the time. So maybe they need to be organized under or around that bench. If the worker can simply reach out to get a tool or put it away, a lot of time can be saved not wandering around retrieving tools or putting them away.
One of my clients had plenty of tools for the staff, but because of thefts all the tools were kept in a tool room and had to be signed in and out. While this kept theft incidents down, it also meant that a lot of time was spent every day with employees walking back and forth to get tools or waiting in line. Their solution was to create smaller tool cages in each area of the shop where the tools used in those jobs were kept. The area supervisors had the keys to the cages and would check tools in and out locally, saving all that time. An unexpected benefit was that the workers tended to maintain the tools better since they knew that they would be using the same tools all the time.
Don’t be afraid to be creative in your solutions. I personally cannot keep track of safety glasses. I find myself wandering around the shop trying to find them or, worse, being tempted to make “just this one cut” without them. My solution is to keep several pairs and leave them on each tool in my shop. I have to move them out of the way to use the table saw, band saw, lathe, etc. Problem solved at a very low cost.
This process does not happen all at once and you should not try to do it all at once. The important lesson is to be conscious of how things are placed, how the work flows, and make changes when you see the opportunity to save a step. Remember, small changes made constantly will add up quickly over time.
This article originally appeared in the October 2011 issue.
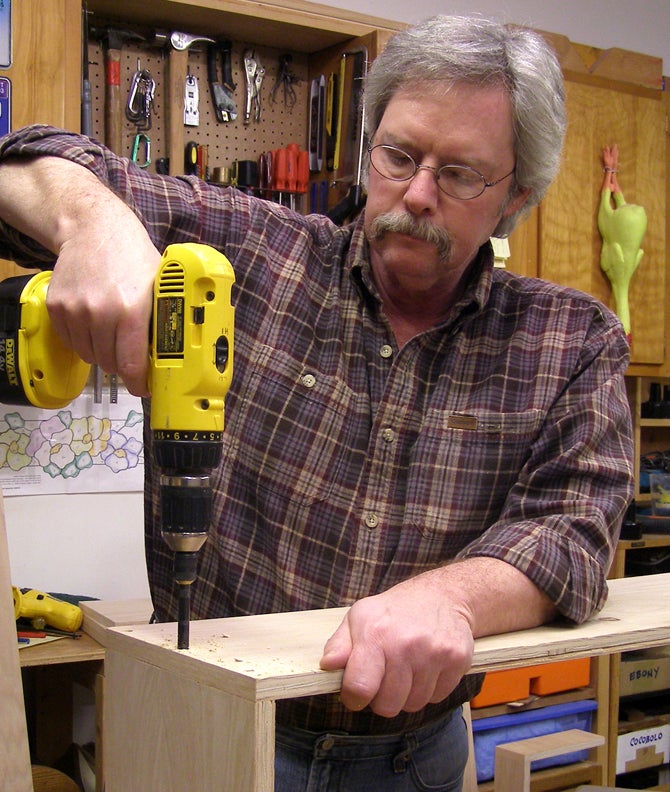
A.J. Hamler is the former editor of Woodshop News and Woodcraft Magazine. He's currently a freelance woodworking writer/editor, which is another way of stating self-employed. When he's not writing or in the shop, he enjoys science fiction, gourmet cooking and Civil War reenacting, but not at the same time.