CNC weds efficiency and craftsmanship
Blind dado construction, using mortise-and-tenon joinery, is one of the classic methods of making cabinets and drawers. In the time before the modernization of cabinetry, when high volume and efficiency…
Blind dado construction, using mortise-and-tenon joinery, is one of the classic methods of making cabinets and drawers. In the time before the modernization of cabinetry, when high volume and efficiency were not as important to the cabinetmaker as beauty, strength and making furniture that became heirlooms, mortise-and-tenon joints were common. These joints not only gave strength to the cabinet being built, but also gave the cabinet the look and feel of being one continuous piece of work with the joints actually hidden from view, thus the more modern name of blind dado construction.
With the advent of sheet material, edgebanding and panel processing, blind dado construction took a back seat to other methods of joinery. Butt joints, coupled with staples, rabbet joints, full dado joints, pocket hole joinery, dowel joinery, biscuits joints and others were much more conducive to the utilization of panels than was mortise-and-tenon joinery. There were simply too many factors to consider with the modern processing of panels, such as edgebanding thickness, consistency of panel thickness, number of sides to be edgebanded, different thicknesses of edgebanding for different jobs and other fluctuations in material that made a clean joint very difficult to attain at an affordable cost.
For example, it is very important for the outside edge of one part to perfectly match the edge of the part to which it is being joined in order to have a continuous surface. One of the worst mistakes a cabinetmaker could make is to have a 1/16" or even a 1/32" difference between the two surfaces being joined. Instead, the cabinetmaker wants the owner of his or her cabinetry to be able to run his hand across the surface of the cabinet so that smoothness and continuity is felt, rather than stark fluctuations on the surface at the points where joints exist. The difference is craftsmanship versus sloppiness.
But recently, with the advent of CNC routers and computerized design software for the cabinet manufacturer, blind dado construction has become more common among those shops concentrating on production and efficiency, as well as among those shops whose focus is individualized craftsmanship. A shop no longer has to choose between one and the other.
There are a number of outstanding software packages on the market that have solved many of the problems associated with blind dado construction such as, in alphabetical order, Cabinet Pro CNC, Cabinet Vision, KCD and Microvellum. All of these software packages have developed to produce solutions for cabinetmakers who own shops of all sizes.
Cabinet Pro, for example, automatically adjusts the width of the mortise, as well as the thickness of the tenon, to accommodate panels of varying thicknesses, although many shops would opt to have these dimensions constant at, for example, 3/8". In addition, if edgebanding is used, the software automatically moves the mortise closer to the edge of the panel by a distance equal to the edgebanding that will eventually be used.
By the press of a button on the software, CNC code is quickly generated for all parts within the job to accommodate whatever CNC router the user owns so that all machining, including blind dado machining, is done automatically and efficiently on the CNC router.
A month or so ago, I was visiting JDG Inc., a small cabinet shop in Eugene, Ore. Steve Ferguson, the owner, had a sheet of prefinished maple lying on his Techno CNC router waiting to cut out all of his drawer box sides, ends and bottoms for Blum Tandem undermount drawer guides. While he and I drank a cup of coffee, his router, taking instructions from his Cabinet Pro design software, not only cut out all of his drawer parts, but machined them such that those parts with mortises were properly machined, those with tenons were machined and even the 6mm holes required for his drawer guides were drilled. By the time we finished our coffee, all he had to do was apply his edgebanding to the drawer sides and ends, insert his various drawer parts into each other with a bead of glue and clamp each drawer box to produce a well-made drawer whose top edges were even with each other.
Ferguson was able to produce not only his drawer boxes, but also his entire cabinets with the craftsmanship that he and his customers expected from a custom cabinet shop with the efficiency and quickness that allowed him to do so at a reasonable cost.
Finally, in 2011, the CNC router, when used with appropriate software, has allowed the modern world of cabinetry to catch up with the classic world, allowing blind dado construction to be utilized in both the shop concentrating on efficiency and production and the shop concentrating on craftsmanship. No longer does a cabinet shop need to choose between efficiency and craftsmanship. It can have both. n
Jimenez is the president and programmer of Siskiyou Products, the producer of Cabinet Pro software.
This article originally appeared in the February 2011 issue.
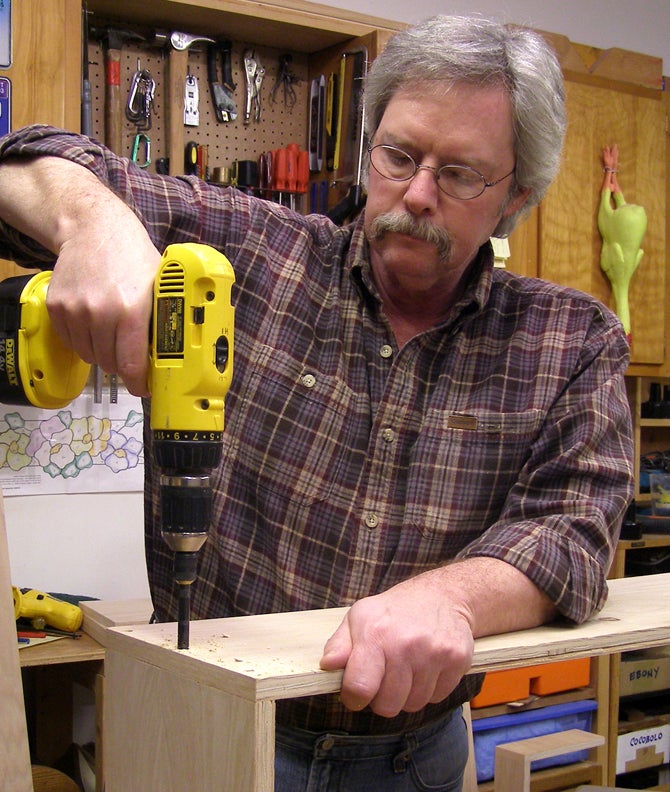
A.J. Hamler is the former editor of Woodshop News and Woodcraft Magazine. He's currently a freelance woodworking writer/editor, which is another way of stating self-employed. When he's not writing or in the shop, he enjoys science fiction, gourmet cooking and Civil War reenacting, but not at the same time.