CNC and your ROI
The following is a starting point for shop owners thinking of making the leap into CNC machinery. It might also be useful for shops that are already up and running…
The following is a starting point for shop owners thinking of making the leap into CNC machinery. It might also be useful for shops that are already up and running as they can use it to introduce new employees to the process.
The first thing to note is that computer numerical control is a somewhat archaic term used to describe how a computer takes a design, reduces it to numbers and uses those numbers to control the movement of a cutting or milling head in two or three axes. It is often referred to nowadays as digital fabrication tooling.
CNC machinery can be a big investment for a woodshop. While it automates certain processes in the shop and replaces some man-hours, the addition of CNC capability usually involves a lot more than just the cost of purchasing or leasing machines. People need to be hired or trained to run it. There will be cutters and inserts to buy and sharpen. The new parts being made might require bins or carts. There will be wiring and dust collection to install. Floor space will be sacrificed — not just for the footprint of the machine, but for new aisles and walkways for people and materials.
Computer-aided design (CAD)
To run a CNC machine, the parts that will be fabricated are first designed on a computer using a CAD program. Most of these programs work in three dimensions (width, length and height) and they create a visual model of the item or part that needs to be fabricated. The design program a woodshop purchases or rents usually depends on how complex the parts will be. For example, it takes a lot less design capacity to create a single flat-panel cabinet door than it does to design an entire back bar for a restaurant. However, both of these projects are designed in much the same manner as the bar is broken into smaller components, which are then individually designed in 3-D models and combined to create the whole.
Many design programs are sold or rented as modules. A shop only needs to buy or lease the modules that cover the kinds of work being done. This alleviates the need for woodworkers to become computer programmers or learn how all aspects of massive programs work.
A 3-D model is merely a mathematical expression, a visualization that takes a flat two-dimensional image and adds perspective to it using simple geometry. The model is a series of lines connecting designated points and nothing more complicated than that, although sometimes the lines are curved. As such, it can be rendered on a 2-D computer screen and printed on paper. It can be rotated and manipulated, scaled and distorted.
Through the years, 3-D design programs have become easier to use and less complicated as more and more of the geometry is buried and the experience becomes less about programming and more about simply drawing parts on a screen. Some programs now even include a concept called digital sculpting, which allows a designer to blow up an image and create new, small, custom details.
The bottom line here is that CAD delivers scaled images that make sense to people and then those are converted to a numerical code that make sense to the actual CNC milling machine.
Code language
Most design programs generate G-code to run the CNC machine. This programming language tells the tool head where to move (left, right, back, forward, up or down), creating the tool path. It also tells the head how fast to move, which is important because of the relationship between the cutter’s size and the properties of the material being cut.
Many design programs allow a woodworker to program the CNC machine without knowing anything about G-code. They use conversational programming, which either hides the code or sometimes eliminates it entirely. New versions of the code include constructs. Initially, G-code couldn’t do any figuring on its own: it could just tell the cutter to travel from one point (dot) to the next. Constructs allow the code to “think” in a rudimentary way, calculating a solution when enough variables have been identified. For example, instead of the operator having to manually locate a long series of very close dots to describe a curve, the code can automatically figure out the arc and length of the curve.
How many axes?
CNC machines come with a different numbers of axes. When more than three axes are offered (those being side-to-side, back-and-forth, up-and-down), the machine is said to be multi-axis. Essentially, this means that the head can swivel, so it’s not always in a strictly vertical position. By tilting a certain amount and then moving diagonally, the cutter can make a whole lot more cuts than its simple 3-axis cousins. For example, it can countersink a hole that is located in a 45-degree plane, so it can drill screw holes for door hinges in complex corner cabinets. And the number of axes doesn’t just describe the cutter’s ability to move: it can also include the table’s movement. Some tables can now tilt in either direction or in compound slopes (that is, they tilt to the right and the front end also dips down), so that more advanced CNC machines can actually manufacture in true 3-D.
Tooling can contribute enormously to the overall versatility of a CNC machine and complement the ways in which the axes add to the machine’s potential. There are lots of tools available for cutting, but also for drilling, milling, shaping, grinding, boring, shearing and forming. These tools are secured in a spindle (the simplest ones are portable routers without the base) and, as the years go by and collet technology improves, it takes less and less time to change out heads. Spindles are usually described in terms of their horsepower, but a woodshop investing in a CNC machine should also ask the salesperson about a spindle’s speed, load ratings, power requirements and the collet type and size.
Stepper and servo motors
A CNC machine can use stepper or servo motors or a combination of the two. First-time buyers often find this issue a little complicated. Essentially, a stepper motor runs on DC and moves in a number of controlled minute ‘steps,’ while a servo motor is usually AC and has continuous motion, so it is usually smoother.
Shops that upgrade from steppers to servos sometimes have a difficult time tuning the new motors and often they need to upgrade the controls, too. Some experienced CNC operators actually prefer steppers because of their ability to lock into a position and stay there (holding torque), while a comparable servo might take a split second to “find” the best position and then it is constantly using current to maintain that new position.
New or used?
A CNC machine is usually a big investment (depending in large part on size, but also on brand and age), so some shops opt to buy a used or refurbished model rather than purchasing brand new.
A couple of the issues involved in buying on the used market are the probable lack of a warranty and the potential inability to upgrade software. But perhaps the biggest drawback is the lack of support. Most brands have some kind of users group online, but that’s never a satisfactory substitute for a qualified, trained service technician.
For a list of CNC suppliers, visit our online resource guide at www.woodshopnews.com.
This article originally appeared in the February 2014 issue.
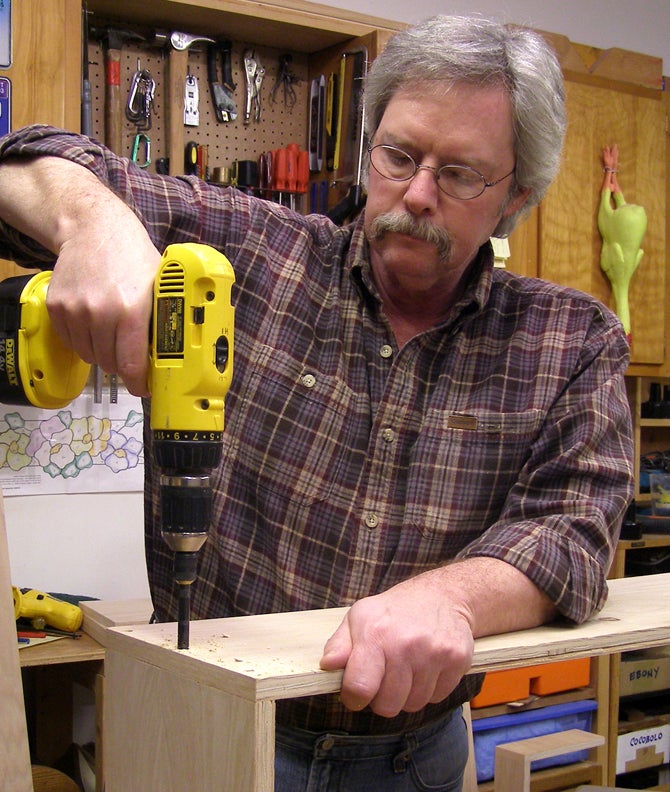
A.J. Hamler is the former editor of Woodshop News and Woodcraft Magazine. He's currently a freelance woodworking writer/editor, which is another way of stating self-employed. When he's not writing or in the shop, he enjoys science fiction, gourmet cooking and Civil War reenacting, but not at the same time.