Smooth operator
Hush! That’s the sound of a Rolair JC10 compressor running. Installers and trim carpenters love this machine because it only generates 60 dB of noise — about the sound level…
Hush!
That’s the sound of a Rolair JC10 compressor running. Installers and trim carpenters love this machine because it only generates 60 dB of noise — about the sound level of a normal conversation. Quiet operation pays two big dividends: the customers don’t have to put up with a racket and the installer doesn’t have to worry about hearing damage.
This kind of engineering is part of a trend toward better ergonomics in the pneumatic tool industry. Merriam-Webster defines ergonomics as “a science that deals with designing and arranging things so that people can use them easily and safely.” The woodworking industry has always been a theater of noise, dust, heavy lifting and sprayed finishes. It’s the nature of the beast. During the last few years, that has started to change in large part because of endless litigation in the workplace, but also because of the information highway. Workers and shop managers are simply more knowledgeable and that usually leads to better decisions. With the world literally at our fingertips, there are very few aspects of life, law and labor that can stay hidden or ignored. We’re probably not getting any smarter, but hopefully we’re becoming a little more informed.
Tool manufacturers are also benefitting from a global economy that has reduced production costs. Even equipment manufactured in the U.S. often incorporates parts made elsewhere. That has enabled engineers to incorporate aspects of design that were once too pricey. One of the earliest examples of this in the woodworking world was a fundamental change in the look and feel of Hitachi power tools from cordless drills to pneumatic nailers. The green, almost comic-book superhero look they adopted was designed to look modern, easy to use and to stand out from the crowd.
Other manufacturers followed and soon tools that had maintained a distinct form for decades became streamlined and sophisticated. After that, function followed form and design began to really look at making small changes that increased the tools’ utility and ease of use. Mainstream industry hadn’t paid this much attention to aesthetics and ergonomics since the heyday of Art Deco between World War I and World War II. And one of the areas that affects woodworkers most was advances in the way that air tools were being tweaked to make our lives just a little easier. The revolution is still happening.
Cold starts and hot switches
Oil-less compressors are part of making things easier to use. They’ve been around for a long time, but now they seem to be the standard rather than a low-price option.
Rolair’s JC10, for example, has that quiet 1-hp induction motor and because it’s oil-less it’s ready to go to work straight out of the box. The compressor is both lightweight and compact but, according to national sales manager Dan Fox, it’s still powerful enough to run up to three trim guns. Even simple things like placing the drain on the side, rather than underneath the tank, make it a little easier with which to work. Being oil-less means it’s maintenance-free, but it also can sit at an angle on a roof without running out of oil and it starts faster in cold temperatures because there’s no viscosity issue. Rolair (www.rolair.com) even added a cold-start valve to this machine that releases a little head pressure so the motor doesn’t have to work quite as hard to get going. That means the installer doesn’t, either.
Another small part of ergonomical design here is that the JC10 comes with an electric solenoid, so that if power is shut off without the switch being thrown (for example, if it’s unplugged while running), the solenoid actually trips the switch and allows the machine to unload the head pressure. (A lot of hobbyists through the years have discovered that unplugging without switching off can kill a compressor.)
One last design feature on the JC10 is a roll cage. These are becoming more and more popular on small, portable compressors, not only to protect the innards but also as a way to handle the machine on the job site. It’s a lot easier for a single installer to lift it up and place it on a pickup tailgate than the old-fashioned models with wheels and a big handle. Available through tool dealers (rather than big-box stores) for around $250, this compressor highlights a transition in the pneumatic tool industry — there is much more merging of serious hobbyist and light professional equipment. One tool increasingly serves two markets. That’s happening because small pro tools are getting cheaper and hobbyist tools are getting better.
One thing that isn’t changing fast enough is that manufacturers are still allowing engineers to name things. For example, the AKHL1250E is a futuristic-looking small compressor from Max USA Corp (www.maxusacorp.com) that is the newest member of its PowerLite line. While the moniker is harder to recall than an online banking password, the machine itself is remarkably memorable. Perhaps the first thing most professional woodworkers will like is the easy drain lever. Just flip a switch and the ball valve opens and drains the air and water (this helps prevent air leaks caused by foreign substances). It’s also remarkably easy to tote around the job site. Weighing just 41.4 lbs., the body is compact (14-5/8” wide and 21-1/2” long) and comes with two-way grips so one worker can comfortably carry it.
All that technology isn’t cheap: Woodshop News found street prices ranging from $1,600 to $1,725 for this model. But its high-pressure air tanks can hold up to 500 psi of compressed air, which means the AKHL1250E delivers the equivalent of 10 gallons in a 100-psi model. There are two regular air outlets and another two that can handle PowerLite high-pressure tools. In another nod to ergonomics, it has a DC brushless motor that is more powerful, quieter and lighter than conventional AC motors and it’s more efficient because an inverter circuit on the motor adjusts the RPM to extract maximum performance depending on the voltage level. And making it easier to handle the technology is a very intuitive control panel display that uses LED lights and beepers to tell you when something is out of sync. At 68dB, the AKHL1250E is almost as quiet as Rollair’s JC10, even though it has a lot more work to do pumping compressed air up to 500 psi.
So new it’s not even here yet
Looking even more futuristic and streamlined than the PowerLite compressors, the newest offering from PneupowerUS is so advanced that it hasn’t even been released yet. Made in the USA, it measures 27.2” x 16.5” x 16.2” and looks like one of those little kneeling pads with handles on the sides that gardeners use when weeding. The chassis is a tough and lightweight Lexan composite and the whole machine weighs in at 48 lbs. It delivers 6.9 CFM at 90 psi with a 1-1/2 gallon tank. The motor is 2 hp. With its rectangular box-like profile, a flat top and a built-in parts drawer, the PneupowerUS compressor is ergonomical to the highest degree.
The company that developed it, Pneupower, is already well-known for another air power product, the ReCoiler, essentially a housing that stores and manages an air hose. The hose is made of a flexible polyurethane that doesn’t stiffen in cold weather (good from -60 F to 175 F) and the high-strength Lexan composite housing is flat, so the case can be stacked and stored easily on top of the compressor.
A third and also very ergonomical unit, a lightweight control module, will be available shortly. This, too, stacks on top of the compressor and allows an installer to regulate air pressure for tools at the point of work. This means that he or she can actually leave the little compressor outside and work almost silently on the install. At the end of the day, the tangle-free hose simply winds into the box like a fishing reel. Available in both 3/8” x 50’ and 1/4” x 100’, it’s extremely lightweight (about 9 lbs., hose and case), and tough enough for the job site (850-psi burst pressure). The hose is extruded twice as an inner and outer core. A high-strength thread, braided around the shell, reinforces the inner core. The outer core is designed with small ribs to shield the inner core from micro-punctures due to chafing on abrasive surfaces such as concrete or roofing material.
Either model of the ReCoiler is available online (www.pneupowerus.com) for $144.95.
Soundproof cabinets
One of the industry leaders in the march toward better ergonomics is California Air Tools (www.californiaairtools.com), which is based in San Diego and distributes through The Home Depot, Woodcraft, Northern Tool and other outlets. In April, the company introduced the 10020SPC model, which is a 2-hp, 10-gallon compressor in its own soundproof cabinet. At 58 dB, it’s one of the quietest 2-hp units on the market.
One method that engineers are using to ramp down sound is to slow down motor speeds (in this case to just 1680 rpm). Slower revs also have the advantage of reducing wear. Models from California Air Tools with ‘SP’ in the name have been designed to increase duty cycle and allow for longer continuous run times. Its oil-free, dual piston pump is built to last — the 10020SPC is designed to have a life cycle before wear of 3,000-plus hours.
The concept of a soundproof cabinet isn’t new, but for small compressors like this it means they can be used on job sites such as schools, office buildings, hospitals and restaurants. On the 10020SPC model, the complete cabinet is 190 lbs., so it’s on casters. The metal frame has 1/4” thick acoustic insulation that reduces noise by 30 percent, according to the company. The compressor delivers 6.4 CFM at 40 psi and 5.3 CFM at 90 psi. It has one 1/4” connector and draws 14 amps. The Home Depot lists it online at $1,500.
California Air Tools offers three different sizes in the soundproof cabinet line — 1 hp, 1.2 hp and 2 hp. Each comes as a basic package or with an optional air dryer and aftercooler.
Trigger happy
Based in Monterey Park, Calif., Grex Power Tools has been building pneumatic tools since 1995. This spring the company is shipping its first orders for the new P650LX, a 23-gauge, 2” headless pinner. Designed in part to accommodate smaller compressors, the new gun pays homage to the definition of ergonomics: designing and arranging things so that people can use them easily and safely. On the company website (www.grexusa.com), Grex says that the X in the name refers to “extra power even with smaller compressors, extra convenience and most importantly an extra safety.” The extra power means that a woodworker can drive longer fasteners into harder woods with smaller compressors and a more robust motor. The extra safety refers to an automatic lockout that was added to prevent dry firing. As installers know, that can cause damage to the tool, but it can also put dents in a brand-new cabinet or molding.
To prevent dry firing, the new feature locks the P650LX with approximately 10 pins remaining in the magazine. Then if you’re up on a ladder and popping crown, you can just press the One-Touch override button and the gun will use the remaining pins one at a time with lots of control.
Senco (www.senco.com) introduced a couple of new tools recently that also illustrate the industry’s shift toward better ergonomics. The team that designed the FinishPro 21 LXP pinner must have the Merriam-Webster definition on a chalkboard in the office: “Ergonomics arranges things so that people can use them easily.” The tool is a 21-gauge pinner that delivers the holding power of a brad nail, while leaving a much smaller indent that requires little to no filling. It bridges the gap between 18-gauge and 23-gauge fasteners, which was a little frustrating for installers on thicker moldings where small pins wouldn’t hold and larger ones left dimples. The tool weighs just 2.7 lbs., and at under 9” tall it can fit into tight spaces.
To combat dry firing, the company added a last nail lockout. Plus, the design is such that an installer or cabinetmaker can easily see when the supply of fasteners is running low. Small things can make a big difference during a long workday: the exhaust on the 21 LXP is located at the rear to direct air away from the user, an embedded muffler pretty much eliminates noise and a swiveling 1/4” plug helps keep the hose at bay.
Eighteen months ago, Senco introduced another ergonomics-conscious product, the SLS150Mg 18-gauge 1/4” crown stapler. The main body on this little gun is constructed from magnesium to cut down on weight (it’s only 2.6 lbs.) without giving up any toughness. It feels well-balanced and has an over-molded grip that lets a woodworker hold on — even with sweaty palms on a hot summer day. It takes 1/2” to 1-9/16” staples, so it works well for trim, furniture and building boxes. There’s an oil-free motor (which is nice around veneers and hardwoods) and an easy-to-use, 360-degree adjustable exhaust port that can be used to blow away any dust and debris. A switch lets the user select bump fire actuation for quick stapling when precise placement is not required. Flip the switch the other way and you’re in sequential fire.
The gun also has a nose-mounted light and a reload indicator that eliminates dry firing. There’s a rotatable belt hook and when you need to adjust the drive depth for different species or thicknesses, there’s a simple thumbwheel.
A little background
Some of the earliest recorded references to ergonomics in the workplace date to the Greek physician Hippocrates (460 BC to 370 BC, famed for the Hippocratic oath). He left extensive notes on the way a surgery should be organized so that a doctor did the least amount of moving around and had everything close at hand.
The first glimmer of ergonomics becoming a science happened during the Industrial Revolution, when a Pennsylvania engineer named Frank Taylor (1856-1915) experimented with shovel sizes and shapes and found that they had a big impact on the volume of coal that a miner could handle in a given amount of time. That evolved into the first time-and-motion studies, which were conducted by the husband-and-wife team of Frank and Lillian Gilbreth. They were industrial engineers and efficiency experts: they had to be as they raised 12 children.
A Russian researcher named Vladimir Nikolayevich Myasishchev had a problem with what he perceived as both Taylor’s and the Gilbreths’ efforts to turn people into machines. He argued that dull work wasn’t very efficient and suggested that the scientific world adopt a new discipline named “ergonology.” That concept found considerable support in major industries such as car and plane manufacturing and eventually trickled down into the industries that supported those fields.
Today, ergonomics is the guiding principle in the way that we design kitchens, schools, offices and institutional casework. From quiet compressors to manageable air hoses or easy starts in cold weather to guns that do their job without creating more work for us filling holes, we have a lot to thank old Vladimir Nikolayevich for.
This article originally appeared in the June 2015 issue.
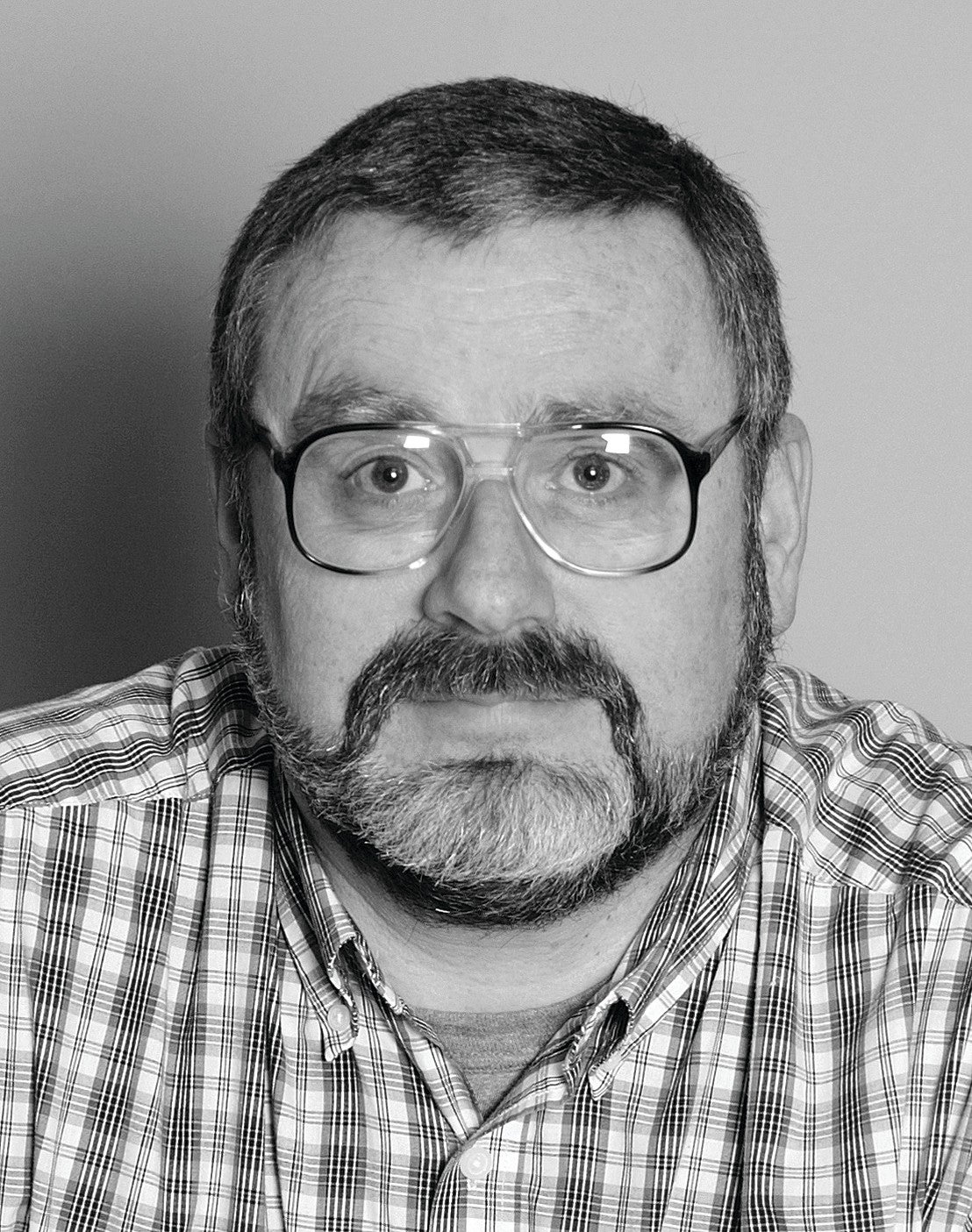